« Procédé Kaldo » : différence entre les versions
m destiné |
transfert de l'article depuis mon espace brouillon Balise : Liens d’homonymie |
||
Ligne 1 : | Ligne 1 : | ||
[[ |
[[image:Kaldokonverter07100011.jpg|vignette|upright=1.2|Ancien [[Convertisseur (métallurgie)|convertisseur]] Kaldo sur ses [[Galet (mécanique)|galets]] à [[Borlänge]] ([[Suède]]).|alt=photo d'une cornue dans un parc]] |
||
Le '''procédé |
Le '''procédé Kaldo''' est un ancien procédé d'[[Affinage (métallurgie)|affinage]] utilisé en [[sidérurgie]] pour traiter la [[fonte brute]] [[phosphore]]use. Il s'agit d'un modèle particulier de [[Convertisseur (métallurgie)|convertisseur]] à l'[[oxygène]] pur, dans lequel le brassage du métal en [[Fusion (métallurgie)|fusion]] est assuré par la rotation de la [[Cornue (industrie)#Convertisseur|cornue]], à l'instar d'une [[bétonnière]]. Le nom « Kaldo » est un [[mot-valise]], construit à partir du nom de son inventeur, le professeur [[Bo Kalling]], et de l'usine qui, en 1948, a développé et industrialisé le procédé, la [[Usine sidérurgique de Borlänge|Domnarvets Jernverk]]. |
||
Le convertisseur a été adapté à la métallurgie des métaux non ferreux, où il est souvent appelé '''TBRC''' (pour ''{{Langue|en|Top Blown Rotary Converter}}''). Il y est un outil très polyvalent, autant pour la fusion de [[Déchets d'équipements électriques et électroniques|déchets riches en cuivre]] ou en [[Métal précieux|métaux précieux]], que pour l'affinage des [[Matte (métallurgie)|mattes]] de [[cuivre]], de [[nickel]], d'[[étain]] ou de [[plomb]]. |
|||
En dépit de ses coûts en [[Matériau réfractaire|réfractaires]] élevés, le procédé Kaldo a été très populaire dans les années 1960 car il a été premier convertisseur à l'oxygène à la fois capable d'affiner efficacement les fontes phosphoreuses, d'élaborer précisément une gamme étendue d'[[alliage]]s et de recycler une grande quantité de [[ferraille]]s. Mais, dépassé quelques années après par les progrès du [[procédé LD]], plus simple et plus compétitif, il disparait en 1982, avec l'arrêt des deux kaldos géants de l'[[Usine sidérurgique de Gandrange-Rombas|aciérie de Gandrange]]. |
|||
Dans l'élaboration des métaux non ferreux, le TBRC a aussi failli disparaitre, avant de redevenir, au début du {{s-|XXI}}, un outil apprécié pour recycler les [[déchets d'équipements électriques et électroniques]]. Sa flexibilité correspond bien à la complexité des charges à traiter, ainsi qu'à des rythmes de production variables. Il est également l'outil le plus efficace pour l'extraction [[Pyrométallurgie|pyrométallurgique]] de métaux précieux présents dans des [[sous-produit]]s d'usine métallurgiques. |
|||
== Histoire == |
== Histoire == |
||
=== Contexte : mise au point du convertisseur à l'oxygène |
=== Contexte : mise au point du convertisseur à l'oxygène === |
||
[[ |
[[image:Schéma Bessemer métallurgie.svg|vignette|lang=fr|upright=0.9|Principe du [[Convertisseur (métallurgie)|convertisseur]] [[Procédé Bessemer|Bessemer]]/[[Procédé Thomas|Thomas]].|alt=schéma]] |
||
{{article général|position=section|Histoire de la production de l'acier}} |
{{article général|position=section|Histoire de la production de l'acier}} |
||
Ligne 17 : | Ligne 21 : | ||
|périodique= Revue de Métallurgie |
|périodique= Revue de Métallurgie |
||
|numéro= 10 |mois= Octobre |année= 2002 |
|numéro= 10 |mois= Octobre |année= 2002 |
||
|pages= 825-837}}</ref>, l'utilisation d'[[dioxygène|oxygène]] pur au lieu d' |
|pages= 825-837}}</ref>, l'utilisation d'[[dioxygène|oxygène]] pur au lieu d'air serait une amélioration logique des [[Procédé Bessemer|convertisseurs Bessemer]] et [[Procédé Thomas|Thomas]]. En effet : |
||
* |
* 78 % de l'air est composé d'[[diazote|azote]] qui n'a aucun rôle utile dans l'[[Affinage (métallurgie)|affinage]] de la [[Fonte brute|fonte]]. Injecter inutilement de l'azote représente une perte thermique, à peine compensée par le bilan [[Réaction exothermique|exothermique]] des réactions chimiques : {{citation|chaque m{{3}} d'azote sortant du convertisseur emporte sensiblement la chaleur nécessaire à la [[Fusion (métallurgie)|fusion]] d'un peu plus d'un kilogramme de ferraille<ref>{{ouvrage |langue=fr |
||
|prénom1= H. |nom1= Lecompte |
|prénom1= H. |nom1= Lecompte |
||
|titre= Cours d'aciérie |
|titre= Cours d'aciérie |
||
Ligne 24 : | Ligne 28 : | ||
|année= 1962 |
|année= 1962 |
||
|pages totales= 309}}</ref>}} ; |
|pages totales= 309}}</ref>}} ; |
||
* la basse teneur de l'air en oxygène limite la vitesse des réactions chimiques |
* la basse teneur de l'air en oxygène limite la vitesse des réactions chimiques ; le soufflage dure plus longtemps parce qu'on ne peut pas augmenter le débit d'air sans risquer un débordement ; |
||
* l'azote se dissout dans l'acier liquide et une fraction y reste quand l'acier se solidifie |
* l'azote se dissout dans l'acier liquide et une fraction y reste quand l'acier se solidifie. Or l'azote est un élément [[Fragilité|fragilisant]] pour l'acier alors qu'une bonne [[ductilité]] est essentielle à de nombreuses applications, notamment la [[Constructeur automobile|construction automobile]] qui recherche des aciers faciles à [[Emboutissage|emboutir]]<ref name=NewSientist244>{{article |langue= en |
||
|prénom1= Donald |nom1= Garmonsway |
|prénom1= Donald |nom1= Garmonsway |
||
|titre= A survey of oxygen steelmaking |
|titre= A survey of oxygen steelmaking |
||
Ligne 32 : | Ligne 36 : | ||
|numéro= 244 |
|numéro= 244 |
||
|page= 153-155 |
|page= 153-155 |
||
|lire en ligne= https://books.google.co.uk/books?id=6NKgGccPRF0C&pg=PA153&hl=fr#v=onepage&q&f=false}}</ref>, avec des teneurs en azote inférieures à {{unité|50|[[Partie par million|ppm]]}}, |
|lire en ligne= https://books.google.co.uk/books?id=6NKgGccPRF0C&pg=PA153&hl=fr#v=onepage&q&f=false}}</ref>, avec des teneurs en azote inférieures à {{unité|50|[[Partie par million|ppm]]}}, inaccessibles avec le procédé Thomas<ref name=NewSientist38>{{article |langue= en |
||
|prénom1= D. J. O. |nom1= Brandt |
|prénom1= D. J. O. |nom1= Brandt |
||
|titre= British steelmaking today and tomorrow |
|titre= British steelmaking today and tomorrow |
||
Ligne 52 : | Ligne 56 : | ||
|mois= juin |année= 1975}}</ref>. |
|mois= juin |année= 1975}}</ref>. |
||
[[ |
[[image:Schéma LD métallurgie.svg|gauche|vignette|lang=fr|upright=0.9|Principe du convertisseur LD.|alt=schéma]] |
||
En 1949, le métallurgiste suisse [[Robert Durrer (métallurgiste)|Robert Durrer]] et l'ingénieur autrichien [[Theodor Eduard Suess]] trouvent une solution satisfaisante : ils mettent au point, à l'[[aciérie]] [[Voestalpine|Vöest]] à [[Linz]] (Autriche), le soufflage d'oxygène au moyen d'une [[Lance thermique|lance]] pénétrant verticalement dans la [[Cornue (industrie)|cornue]]. L'invention apparaît vite comme une [[technologie de rupture]] : six mois après le premier essai, le prototype |
En 1949, le métallurgiste suisse [[Robert Durrer (métallurgiste)|Robert Durrer]] et l'ingénieur autrichien [[Theodor Eduard Suess]] trouvent une solution satisfaisante : ils mettent au point, à l'[[aciérie]] [[Voestalpine|Vöest]] à [[Linz]] (Autriche), le soufflage d'oxygène au moyen d'une [[Lance thermique|lance]] pénétrant verticalement dans la [[Cornue (industrie)|cornue]]. L'invention apparaît vite comme une [[technologie de rupture]] : six mois après le premier essai, le prototype s'avère plus économique que les meilleurs convertisseurs classiques ! En effet, ils combinent l'avantage des [[Procédé Martin-Siemens|convertisseurs Martin]] {{incise|l'absence d'azote dans l'acier}} avec la productivité des convertisseurs Bessemer et Thomas {{incise|une conversion rapide et sans apport de combustible}}. Plus efficaces et donc moins nombreux que leurs équivalents à l'air, les nouveaux [[Procédé LD|convertisseurs LD]] ne demandent qu'un investissement environ deux tiers, et des coûts d'exploitation limités à 55 % de ceux d'une usine traditionnelle de capacité comparable<ref>{{Lien web |langue= de |
||
|prénom1= Roman |nom1= Sandgruber |
|prénom1= Roman |nom1= Sandgruber |
||
|titre= Das LD-Verfahren erobert die Welt (Les LD conquièrent le monde) |
|titre= Das LD-Verfahren erobert die Welt (Les LD conquièrent le monde) |
||
Ligne 61 : | Ligne 65 : | ||
|éditeur= Oberösterreichische Nachrichten}}</ref>. |
|éditeur= Oberösterreichische Nachrichten}}</ref>. |
||
Dans le convertisseur LD, le brassage est assuré par la remontée de bulles de [[monoxyde de carbone]] (CO) produites par la [[décarburation]] de la |
Dans le convertisseur LD, le brassage est assuré par la remontée de bulles de [[monoxyde de carbone]] (CO) produites par la [[décarburation]] de la fonte. Mais ce mouvement, efficace en début de soufflage, tend à ralentir lorsque le carbone dissous passe en dessous de 0,1 %, et le brassage avec le [[Laitier (métallurgie)|laitier]] diminue corrélativement. Or, l'[[Réaction d'oxydoréduction|oxydation]] du [[phosphore]] ne se produit qu'après le départ de tout le carbone, et la capture de l'[[Pentoxyde de phosphore|oxyde {{fchim|P|2|O|5}}]] nécessite un brassage énergique avec la [[Chaux (matière)|chaux]] du laitier. L'histoire se répète : comme jadis le convertisseur de Bessemer, le procédé LD révolutionne la [[sidérurgie]] mais se révèle inadapté à l'affinage des fontes phosphoreuses<ref name="Soleild'acier"/>. |
||
Enfin, les convertisseurs à l'oxygène pur |
Enfin, les convertisseurs à l'oxygène pur génèrent d'énormes quantités de fumées rousses, chargées en [[oxyde de fer]]. Le [[Assainissement particulaire de l'air|dépoussiérage]] de ces fumées est incontournable. Même si ces fumées contiennent du [[gaz de convertisseur]] (monoxyde de carbone, CO) combustible ({{unité|0.7|GJ/tonne}} d'acier<ref name="Soleild'acier"/>), avant le [[premier choc pétrolier]] de 1973, le coût d'investissement du système de dépoussiérage pénalise le procédé LD<ref name=NewSientist244/>. |
||
=== Développement du convertisseur rotatif === |
=== Développement du convertisseur rotatif === |
||
Depuis les années 1940, en Suède, la [[Domnarvets Jernverk]], mène d'actives recherches pour mettre au point un procédé à l'oxygène pur capable de traiter les fontes phosphoreuses. En effet, la [[fonte brute]] traitée par l'[[aciérie]] de Domnarvet contenant de 1,8 à 2 % de [[phosphore]], l'efficacité |
Depuis les années 1940, en Suède, la [[Usine sidérurgique de Borlänge|Domnarvets Jernverk]], mène d'actives recherches pour mettre au point un procédé à l'oxygène pur capable de traiter les fontes phosphoreuses. En effet, la [[fonte brute]] traitée par l'[[aciérie]] de Domnarvet contenant de 1,8 à 2 % de [[phosphore]], l'efficacité de la déphosphoration est un point incontournable<ref>{{Ouvrage |langue= en |
||
|prénom1= James Albert |nom1= Allen |
|prénom1= James Albert |nom1= Allen |
||
|titre= Studies in Innovation in the Steel and Chemical Industries |
|titre= Studies in Innovation in the Steel and Chemical Industries |
||
Ligne 74 : | Ligne 78 : | ||
|pages totales= 246 |
|pages totales= 246 |
||
|isbn= 0678067902 |isbn2= 978-0678067901 |
|isbn= 0678067902 |isbn2= 978-0678067901 |
||
|passage= 138}}</ref>. Jusqu'ici, dans un pays où le [[minerai de fer]] est bien plus abondant que les [[ferraille]]s, le moyen le plus pertinent pour traiter ce type de fonte est le |
|passage= 138}}</ref>. Jusqu'ici, dans un pays où le [[minerai de fer]] est bien plus abondant que les [[ferraille]]s, le moyen le plus pertinent pour traiter ce type de fonte est le convertisseur Thomas. Mais l'injection d'oxygène dans le convertisseur amène une destruction rapide des [[Matériau réfractaire|réfractaires]]. Bien qu'en 1940, à [[Oberhausen (Rhénanie-du-Nord-Westphalie)|Oberhausen]] ([[Allemagne]]), l'ingénieur américain d'origine [[Estoniens|estonienne]] [[Otto Lellep]] parvient à décarburer de la fonte avec de l'oxygène pur, il ne parvient pas à la déphosphorer : avec l'oxygène pur, l'oxydation du phosphore est trop [[Réaction exothermique|exothermique]] pour les tuyères du convertisseur<ref name=LWS/>. |
||
Pour dépasser 40 % d'oxygène, il faut des diluants plus efficaces que l'azote, et surtout moins nocifs vis-à-vis des propriétés de l'acier car l'azote [[Fragilité|fragilise]] l'acier. L'aciérie de Domnarvet adopte alors le [[dioxyde de carbone]] ({{Fchim|CO|2}}) dont le [[Thermolyse (chimie)|craquage]] à haute température, [[réaction endothermique|endothermique]], permet de refroidir sensiblement le |
Pour dépasser 40 % d'oxygène, il faut des diluants plus efficaces que l'azote, et surtout moins nocifs vis-à-vis des propriétés de l'acier car l'azote [[Fragilité|fragilise]] l'acier. L'aciérie de Domnarvet adopte alors le [[dioxyde de carbone]] ({{Fchim|CO|2}}) dont le [[Thermolyse (chimie)|craquage]] à haute température, [[réaction endothermique|endothermique]], permet de refroidir sensiblement le réfractaire. En 1947-1949, en fin de soufflage, les convertisseurs Thomas de Domnarvet soufflent ainsi un mélange gazeux contenant jusqu'à 58 % d'oxygène<ref>{{article |langue= fr |
||
|nom1= Kalling et al. |
|nom1= Kalling et al. |
||
|titre= Emploi d'oxygène-acide carbonique au lieu d'air pour le soufflage final dans le procédé Thomas |
|titre= Emploi d'oxygène-acide carbonique au lieu d'air pour le soufflage final dans le procédé Thomas |
||
Ligne 82 : | Ligne 86 : | ||
|mois= janvier |année= 1954}}</ref>. |
|mois= janvier |année= 1954}}</ref>. |
||
[[ |
[[image:Kaldo Converter.svg|droite|vignette|lang=fr|upright=1.2|Principe du convertisseur Kaldo.|alt=schéma d'un Kaldo]] |
||
Mais mélanger l'oxygène avec un refroidissant ne peut être une solution satisfaisante. Pour injecter de l'oxygène pur, il faut momentanément<ref group=note>Le soufflage d'oxygène pur par le fond ne sera mis au point que dans les années 1970, avec les procédés de type OBM (''{{Langue|de|Oxygen-Bottom Maxhütte}}'').</ref> renoncer au soufflage par le fond, et assurer le brassage du métal par un autre moyen. Dans ce contexte, la rotation du convertisseur s'impose comme une des rares configurations techniquement réaliste et compatible avec une injection d'oxygène par une [[Lance thermique|lance]]<ref name=LWS/>. |
Mais mélanger l'oxygène avec un refroidissant ne peut être une solution satisfaisante. Pour injecter de l'oxygène pur, il faut momentanément<ref group=note>Le soufflage d'oxygène pur par le fond ne sera mis au point que dans les années 1970, avec les procédés de type OBM (''{{Langue|de|Oxygen-Bottom Maxhütte}}'').</ref> renoncer au soufflage par le fond, et assurer le brassage du métal par un autre moyen. Dans ce contexte, la rotation du convertisseur s'impose comme une des rares configurations techniquement réaliste et compatible avec une injection d'oxygène par une [[Lance thermique|lance]]<ref name=LWS/>. |
||
Ligne 95 : | Ligne 99 : | ||
|volume= 2 |
|volume= 2 |
||
|page= 86-88 |
|page= 86-88 |
||
|lire en ligne= https://repositorio.cepal.org/bitstream/handle/11362/26694/S5700174_es.pdf}}</ref> avec un prototype d'une capacité interne de {{ |
|lire en ligne= https://repositorio.cepal.org/bitstream/handle/11362/26694/S5700174_es.pdf}}</ref> avec un prototype d'une capacité interne de {{unité|3|tonnes}}, puis un pilote de {{unité|15|tonnes}}. Le premier démonstrateur industriel, de {{unité|30|tonnes}}, est construit en 1954 et est opérationnel en 1956<ref name=Bhardwaj>{{ouvrage |langue= en |
||
|prénom1= B.P. |nom1= Bhardwaj |
|prénom1= B.P. |nom1= Bhardwaj |
||
|titre= Steel and Iron Handbook |
|titre= Steel and Iron Handbook |
||
Ligne 104 : | Ligne 108 : | ||
|passage= 302-313}}</ref>. |
|passage= 302-313}}</ref>. |
||
Ce convertisseur est appelé « Kaldo », un [[mot-valise]], construit à partir du nom de son inventeur, le professeur [[Bo Kalling]], et de l'usine qui a développé et industrialisé le procédé, la Domnarvets Jernverk. Il se révèle être un succès technique. La possibilité de jouer sur la vitesse de rotation et l'inclinaison de la lance apporte une flexibilité unique. Notamment, grâce à la rotation, la |
Ce convertisseur est appelé « Kaldo », un [[mot-valise]], construit à partir du nom de son inventeur, le professeur [[Bo Kalling]], et de l'usine qui a développé et industrialisé le procédé, la Domnarvets Jernverk. Il se révèle être un succès technique. La possibilité de jouer sur la vitesse de rotation et l'inclinaison de la lance apporte une flexibilité unique. Notamment, grâce à la rotation, la décarburation n'a plus à assurer le brassage du bain et l'injection d'oxygène peut être moins violente. L'oxygène, qui se répand alors dans la cornue, brûle le monoxyde de carbone en [[dioxyde de carbone]], apportant une chaleur supplémentaire qui peut être utilisée pour refondre des [[ferraille]]s. Le gaz ainsi brûlé n'ayant plus de potentiel comme combustible, son traitement se limite à un dépoussiérage sans récupération. Cette simplification compense, en partie, la complexité mécanique due à la rotation<ref name=Bhardwaj/>. |
||
=== Adoption du procédé === |
=== Adoption du procédé === |
||
Les sidérurgistes [[Lorraine|lorrains]], dont le |
Les sidérurgistes [[Lorraine|lorrains]], dont le minerai local, la [[Minette lorraine|minette]], est riche en phosphore, s'intéressent de près au procédé. Convaincus par la nécessité de passer au convertisseur à l'oxygène, ils sont, en 1960, à l'origine du deuxième convertisseur Kaldo. Celui-ci, installé à l'[[usine sidérurgique de Florange]], représente un saut capacitaire notable par rapport à son aîné : il peut affiner {{unité|110|tonnes}} de fonte phosphoreuse<ref name="Soleild'acier"/>. Il s'agit aussi du plus gros convertisseur à l'oxygène pur présent en [[Lorraine]]. Sa capacité est par la suite progressivement augmentée jusqu'à {{unité|140|tonnes}}<ref name=Thouvenin/>. |
||
[[ |
[[image:Convertisseur Kaldo de Florange - Coupe transversale.svg|center|upright=2.5|vignette|Coupe transversale de l’aciérie Kaldo de [[Florange]] ([[Lorraine]]), en service de 1960 à 1980.|alt=plan de l'aciérie, coupe transversale Nord-Sud]] |
||
Dans les années suivantes, le procédé est systématiquement évalué comme une alternative au procédé LD et à ses dérivés. Dès 1965, 10 usines utilisent le procédé Kaldo, en France, Suède, États-Unis, Japon et surtout au Royaume-Uni. Les capacités des nouveaux convertisseurs se situent entre {{unité/2|50|et=140|tonnes}}<ref name= |
Dans les années suivantes, le procédé est systématiquement évalué comme une alternative au procédé LD et à ses dérivés. Dès 1965, 10 usines utilisent le procédé Kaldo, en France, Suède, États-Unis, Japon et surtout au Royaume-Uni. Les capacités des nouveaux convertisseurs se situent entre {{unité/2|50|et=140|tonnes}}<ref name=Allen141>{{Harvsp|Allen|1967|p=141}}</ref>. Mais l'avenir du procédé semble déjà compromis : dès 1967, le [[métallurgie|métallurgiste]] James Albert Allen estime que {{citation|Avec une plus grande consommation de capitaux, des problèmes techniques et une consommation en réfractaire plus élevée, il apparaît plutôt douteux qu'il puisse rivaliser efficacement avec les procédés LD, LD-AC ou leurs évolutions.<ref>{{Harvsp|Allen|1967|p=140}}</ref>}} |
||
{| class="wikitable center" style="text-align:center; width:60%;" |
{| class="wikitable center" style="text-align:center; width:60%;" |
||
|+ |
|+ Comparaison des coûts relatifs (en %), pour une aciérie produisant {{unité|1|Mt/an}} d'acier à partir de fonte non phosphoreuse, en 1965<ref>{{article |langue= sl |format électronique= pdf |
||
|périodique= Železar |
|périodique= Železar |
||
|titre= Zgradili Bomo Kaldo Konvertor |
|titre= Zgradili Bomo Kaldo Konvertor |
||
|jour= 1 |mois= mai |année= 1965 |
|jour= 1 |mois= mai |année= 1965 |
||
|passage= 5-7 |
|passage= 5-7 |
||
|lire en ligne= http://www.jlib.si/pdfs/1965-018.pdf}}</ref> |
|lire en ligne= http://www.jlib.si/pdfs/1965-018.pdf}}</ref> : |
||
! |
|||
! Coûts (%) |
|||
! {{nobr|[[Procédé Martin-Siemens]]}} {{nobr|( |
! {{nobr|[[Procédé Martin-Siemens]]}} {{nobr|(référence)}} |
||
! Procédé Kaldo |
! Procédé Kaldo |
||
! [[Procédé LD]] |
! [[Procédé LD]] |
||
Ligne 131 : | Ligne 135 : | ||
| 50 |
| 50 |
||
|- |
|- |
||
! scope=row | Coût de fonctionnement |
! scope=row | {{nobr|Coût de fonctionnement}} |
||
| 100 |
| 100 |
||
| 72,5 |
| 72,5 |
||
Ligne 137 : | Ligne 141 : | ||
|} |
|} |
||
En effet, au début des années 1960, des variantes du [[procédé LD]] capables de traiter les fontes phosphoreuses sont mises au point : le convertisseur LD-AC, qui permet d'injecter de la [[Chaux (matière)|chaux]] (CaO) en poudre en la mélangeant avec l'oxygène démontre la flexibilité du soufflage par le haut<ref name="NewSientist244" />. D'autres variantes sont ensuite développées sur ce principe (LBE, LD-Pompey, OLP{{etc}}). Cependant, le procédé LD perd beaucoup de son intérêt dès qu'on l'emploie à l'affinage des fontes phosphoreuses<ref name="Soleild'acier" />. Surtout, tous ces procédés mettent en œuvre des réactions chimiques très rapides. Dans les années qui suivent leur apparition, les convertisseurs LD et leurs dérivés sont exclus de l'élaboration d'aciers de qualité<ref>{{Harvsp|Allen|1967|p=196}}</ref>. L'apparition de la [[coulée continue]], qui exige un excellent contrôle de la température de l'acier en fusion, nécessite aussi un bon contrôle de l'affinage<ref>{{Harvsp|Allen|1967|p=202}}</ref>. |
|||
En effet, au début des années 1960, des variantes du procédé LD capables de traiter les fontes phosphoreuses sont mises au point : le procédé LD-AC, qui consiste à injecter de la [[Chaux (matière)|chaux]] en poudre en la mélangeant avec l'oxygène démontre la flexibilité du soufflage par le haut<ref name=NewSientist244/>. D'autres variantes sont ensuite développées sur ce principe (LBE, LD-Pompey, OLP{{etc}}).Cependant, le procédé LD perd beaucoup de son intérêt dès qu'on l'emploie à l'affinage des fontes phosphoreuses<ref name="Soleild'acier"/>. Surtout, tous ces procédés mettent en œuvre des réactions chimiques très rapides. Dans les années qui suivent leur apparition, les convertisseurs LD et leurs dérivés sont exclus de l'élaboration d'aciers de qualité<ref>{{Harvsp|Allen|1967|p=196}}</ref>. L'apparition de la [[coulée continue]], qui exige un excellent contrôle de la température de l'acier en fusion, nécessite aussi un bon contrôle de l'affinage<ref>{{Harvsp|Allen|1967|p=202}}</ref>. |
|||
[[Image:Acierie de Gandrange.JPG|vignette|upright=1.2|L'[[Usine sidérurgique de Gandrange-Rombas|aciérie de Gandrange]], fermée en 2009. Les derniers et les plus gros convertisseurs sidérurgiques Kaldo du monde y ont été exploités de 1969 à 1982<ref name="Thouvenin">{{article |
|||
[[image:Acierie de Gandrange.JPG|vignette|upright=1.2|L'[[Usine sidérurgique de Gandrange-Rombas|aciérie de Gandrange]], fermée en 2009. Les derniers et les plus gros convertisseurs sidérurgiques Kaldo du monde y ont été exploités de 1969 à 1982<ref name=Thouvenin>{{article |
|||
|prénom1= Monique |nom1= Thouvenin |
|prénom1= Monique |nom1= Thouvenin |
||
|titre= De Wendel-Sidélor à Sacilor-Sollac : 1968-1980. 13 années de mutations difficiles en Lorraine. |
|titre= De Wendel-Sidélor à Sacilor-Sollac : 1968-1980. 13 années de mutations difficiles en Lorraine. |
||
Ligne 148 : | Ligne 153 : | ||
|lire en ligne= http://www.persee.fr/doc/rgest_0035-3213_1981_num_21_1_1483}}</ref>.|alt=photo de l'aciérie]] |
|lire en ligne= http://www.persee.fr/doc/rgest_0035-3213_1981_num_21_1_1483}}</ref>.|alt=photo de l'aciérie]] |
||
C'est ainsi que, en 1969, {{citation|D'autres [[Ordre mevlevi|derviches]] métallurgiques devaient succéder […], notamment les deux Kaldo de {{ |
C'est ainsi que, en 1969, {{citation|D'autres [[Ordre mevlevi|derviches]] métallurgiques devaient succéder […], notamment les deux Kaldo de {{unité|240|tonnes}} de [[Usinor#Sacilor|Sacilor]] à [[Gandrange]].<ref name="Soleild'acier"/>}} Ces énormes engins de {{unité|1500|tonnes}}<ref>{{Ouvrage |format électronique= pdf |
||
|prénom1= Jean-Yves |nom1= Debost |
|prénom1= Jean-Yves |nom1= Debost |
||
|prénom2= Bernard |nom2= Réal |
|prénom2= Bernard |nom2= Réal |
||
Ligne 155 : | Ligne 160 : | ||
|année= 1975 |mois= mars |
|année= 1975 |mois= mars |
||
|passage= 48 |partie= 2 |
|passage= 48 |partie= 2 |
||
|lire en ligne= http://temis.documentation.developpement-durable.gouv.fr/docs/Temis/0002/Temis-0002676/3240_1.pdf}}</ref> qui tournent à {{ |
|lire en ligne= http://temis.documentation.developpement-durable.gouv.fr/docs/Temis/0002/Temis-0002676/3240_1.pdf}}</ref> qui tournent à {{unité|30|tour/min}} sont deux fois plus gros que n'importe quel autre convertisseur Kaldo ! Mais deux ans plus tard, deux convertisseurs OLP de {{unité|240|tonnes}} sont mis en service dans la même aciérie alors que le troisième Kaldo prévu est annulé. La course à la taille, censée favoriser les [[Économie d'échelle|économies d'échelle]], a tué le procédé au lieu de le sauver : la limite technologique est atteinte, les coûts augmentent avec les dimensions alors que c'est l'inverse qui était escompté<ref name=Freyssenet1979>{{Ouvrage |langue=fr |format électronique= pdf |
||
|prénom1= Michel |nom1= Freyssenet |
|prénom1= Michel |nom1= Freyssenet |
||
|titre= La sidérurgie française 1945-1979 |sous-titre= L'histoire d'une faillite. Les solutions qui s'affrontent. |
|titre= La sidérurgie française 1945-1979 |sous-titre= L'histoire d'une faillite. Les solutions qui s'affrontent. |
||
Ligne 170 : | Ligne 175 : | ||
{{Détail image |image= Chemetco Metallo-Chimique Kaldo converters after disassembly.jpg |largeur initiale= 900 |largeur détail= 250 |hauteur détail= 230 |point haut= 50 |point gauche = 0 |position= gauche |légende= Le premier Kaldo de la [[Chemetco]], en 2011, avant son démantèlement. |alt=Photo d'une cornue sur socle béton}} |
{{Détail image |image= Chemetco Metallo-Chimique Kaldo converters after disassembly.jpg |largeur initiale= 900 |largeur détail= 250 |hauteur détail= 230 |point haut= 50 |point gauche = 0 |position= gauche |légende= Le premier Kaldo de la [[Chemetco]], en 2011, avant son démantèlement. |alt=Photo d'une cornue sur socle béton}} |
||
En 1958, soit deux ans après la mise en service industrielle du premier Kaldo sidérurgique de {{ |
En 1958, soit deux ans après la mise en service industrielle du premier Kaldo sidérurgique de {{unité|30|tonnes}} à Domnarvet, l'entreprise canadienne [[Inco]] commence à évaluer la déclinaison de ce procédé à la [[Extraction du nickel|métallurgie extractive du nickel]]. Elle envoie quelques ingénieurs en Suède pour explorer la conversion à l'oxygène pur de la [[Matte (métallurgie)|matte]] de nickel avec le prototype originel de {{unité|3|tonnes}}. Tous leurs essais ayant réussi, Inco construit un convertisseur expérimental de {{unité|7|tonnes}} dans son centre de recherche de [[Port Colborne]]<ref name=OxygenCopperCliff>{{article |langue= en |
||
|périodique= The Minerals, Metals & Materials Society |
|périodique= The Minerals, Metals & Materials Society |
||
|prénom1= Paul E. |nom1= Queneau |
|prénom1= Paul E. |nom1= Queneau |
||
Ligne 183 : | Ligne 188 : | ||
|périodique= The telegraph |lieu= Alton |
|périodique= The telegraph |lieu= Alton |
||
|passage= 1 ; 9 |
|passage= 1 ; 9 |
||
|lire en ligne= https://newspaperarchive.com/alton-telegraph-oct-31-2001-p-1/}}</ref>, une entreprise américaine qui met en service cette année-là un Kaldo de {{ |
|lire en ligne= https://newspaperarchive.com/alton-telegraph-oct-31-2001-p-1/}}</ref>, une entreprise américaine qui met en service cette année-là un Kaldo de {{unité|70|tonnes}} de capacité construit par [[Krupp (entreprise)|Krupp]]<ref name=Verney>{{article |langue= en |
||
|titre= Pyrometallurgy |
|titre= Pyrometallurgy |
||
|prénom= L. R. |nom= Verney |
|prénom= L. R. |nom= Verney |
||
Ligne 191 : | Ligne 196 : | ||
|lire en ligne= https://link.springer.com/article/10.1007%2FBF03354304}}</ref>. |
|lire en ligne= https://link.springer.com/article/10.1007%2FBF03354304}}</ref>. |
||
Si la Métallo-Chimique semble la première entreprise à utiliser un kaldo industriel de {{ |
Si la Métallo-Chimique semble la première entreprise à utiliser un kaldo industriel de {{unité|70|tonnes}}{{note|Il est difficile de déterminer la date précise de mise en service du premier Kaldo de la [[Metallo-Chimique]]. Le convertisseur rotatif y a été adopté pendant les années 1960 pour se généraliser en 1974<ref name=metallo/>, mais le premier brevet (n° CA979224A) ne date que de 1970. Celui-ci traite de principes généraux sur l'affinage de métaux non ferreux, tout en évoquant des cas industriels relatifs à un convertisseur de {{unité|70|tonnes}}. Par ailleurs, ce brevet, comme les suivants, est déposé uniquement au Canada et aux États-Unis. Il vise donc à éviter tout blocage de la part du concurrent Inco, dont les brevets pourraient gêner une pratique discrètement mise au point<ref name=CA979224A>{{lien web |lang= en |
||
|titre= Process for recovering copper from copper-bearing materials (CA 979224 A) |
|titre= Process for recovering copper from copper-bearing materials (CA 979224 A) |
||
|jour= 14 mois= octobre |mois= 1970 |
|jour= 14 mois= octobre |mois= 1970 |
||
|url= https://worldwide.espacenet.com/publicationDetails/biblio?locale=fr_EP&II=8&FT=D&CC=CA&DB=EPODOC&NR=986721A&date=19760406&ND=3&KC=A&adjacent=true}}</ref>, mais aussi à protéger les activités de la Chemetco, créée cette année-là sous l'égide des Belges<ref name=TheTelegraph/>.|name=metallo-chimique|group=note}} pour l'affinage des métaux non ferreux, c'est Inco qui, par la mise en service en 1971 de deux convertisseurs de {{ |
|url= https://worldwide.espacenet.com/publicationDetails/biblio?locale=fr_EP&II=8&FT=D&CC=CA&DB=EPODOC&NR=986721A&date=19760406&ND=3&KC=A&adjacent=true}}</ref>, mais aussi à protéger les activités de la Chemetco, créée cette année-là sous l'égide des Belges<ref name=TheTelegraph/>.|name=metallo-chimique|group=note}} pour l'affinage des métaux non ferreux, c'est Inco qui, par la mise en service en 1971 de deux convertisseurs de {{unité|50|tonnes}} à Copper Cliff ([[Grand Sudbury]]), lance véritablement l'utilisation du Kaldo dans la production des non ferreux. Cette adaptation est renommée TBRC (pour ''{{Langue|en|Top Blown Rotary Converter}}''). Elle structure la stratégie d'Inco et s'avère un succès : en 1979, ces deux convertisseurs ont déjà élaboré un million de tonnes de nickel<ref name=OxygenCopperCliff/>{{,}}{{note|Ce sont les ingénieurs Paul Queneau et John Feick, responsables de l'exploitation des [[convertisseur Peirce-Smith|convertisseurs Peirce-Smith]] d'[[Inco]], aidés par John Thompson, ingénieur chimiste et [[directeur général]] qui, en 1958, vont explorer la conversion à l'oxygène pur des mattes de nickel. Les TBRC d'Inco deviennent la première étape de la transformation de composés métalliques complexes, jusqu'à l'obtention de nickel pur à 99,98 % par le [[procédé Mond]]<ref name=OxygenCopperCliff/>.|group=note}}, et produisent encore, {{unité|45|ans}} après leur mise en service<ref name=Vale>{{lien web |lang= en |
||
|titre= Nickel refinery in Canada optimizes the process of rotary converter exchange |
|titre= Nickel refinery in Canada optimizes the process of rotary converter exchange |
||
|jour= 10 |mois= juillet |année= 2015 |
|jour= 10 |mois= juillet |année= 2015 |
||
Ligne 200 : | Ligne 205 : | ||
|url= http://www.vale.com/brasil/EN/aboutvale/news/Pages/refinaria-niquel-canada-otimiza-processo-troca-conversor-rotativo.aspx}}</ref>. |
|url= http://www.vale.com/brasil/EN/aboutvale/news/Pages/refinaria-niquel-canada-otimiza-processo-troca-conversor-rotativo.aspx}}</ref>. |
||
Très semblables aux kaldos, les convertisseurs TBRC intègrent le fait que l' |
Très semblables aux kaldos, les convertisseurs TBRC intègrent le fait que l'oxydation des mattes étant beaucoup moins exothermique que l'oxydation de la [[Fonte brute|fonte]]{{note|L'affinage de la fonte au convertisseur est facile car la combustion des éléments indésirables est fortement exothermique : l'oxydation du [[silicium]] et du [[carbone]] y produit respectivement {{unité/2|32.8|et=10.3|[[Joule|kilojoules]]}} par kilogramme<ref>{{ouvrage |langue=fr |
||
|prénom1= Adolf |nom1= Ledebur |lien auteur= Adolf Ledebur |
|prénom1= Adolf |nom1= Ledebur |lien auteur= Adolf Ledebur |
||
|traducteur= Barbary de Langlade revu et annoté par F. Valton |
|traducteur= Barbary de Langlade revu et annoté par F. Valton |
||
Ligne 242 : | Ligne 247 : | ||
|lire en ligne= https://businessdocbox.com/Metals/70837337-Emc-91-non-ferrous-metallurgy-present-and-future.html}}</ref>. |
|lire en ligne= https://businessdocbox.com/Metals/70837337-Emc-91-non-ferrous-metallurgy-present-and-future.html}}</ref>. |
||
En 1976, l'entreprise suédoise [[Boliden AB]] met en service dans son [[usine métallurgique de Rönnskär|usine de Rönnskär]] le premier TBRC produisant du [[plomb]]. L'extraction de ce métal nécessite une étape supplémentaire consistant en une |
En 1976, l'entreprise suédoise [[Boliden AB]] met en service dans son [[usine métallurgique de Rönnskär|usine de Rönnskär]] le premier TBRC produisant du [[plomb]]. L'extraction de ce métal nécessite une étape supplémentaire consistant en une réduction, qui se déroule après la fusion et l'oxydation de la charge<ref name=Ronnskar>{{lien web |langue= en |
||
|titre= Rönnskär's history |
|titre= Rönnskär's history |
||
|éditeur= Boliden AB |lien éditeur= Boliden AB |
|éditeur= Boliden AB |lien éditeur= Boliden AB |
||
|url= https://www.boliden.com/operations/smelters/boliden-ronnskar/history |
|url= https://www.boliden.com/operations/smelters/boliden-ronnskar/history |
||
|consulté le= 29-12-2022}}</ref>. Cette |
|consulté le= 29-12-2022}}</ref>. Cette réduction est obtenue en brûlant un combustible riche en carbone ([[coke de pétrole]], [[wikt:poussier|poussier]] de [[Coke (charbon)|coke]]{{etc}}) dans le convertisseur, de manière à y créer une atmosphère réductrice riche en [[Monoxyde de carbone|CO]] tout en apportant de la chaleur<ref name=BlazyJdidPyro/>{{,}}<ref name=EMC91/>. Initialement dédié à l'extraction du plomb contenu dans les poussières issues de la production de cuivre, le TBRC de Boliden devient en 1980 un outil polyvalent, recyclant soit des [[Déchets d'équipements électriques et électroniques|déchets électroniques]] contenant du cuivre, soit des déchets riches en plomb<ref name=Ronnskar/>. |
||
En 1978, la [[fonderie d'étain de Texas City]] met en service un TBRC entièrement |
En 1978, la [[fonderie d'étain de Texas City]] met en service un TBRC entièrement dédié à la fusion réductrice de minerais concentrés de [[cassitérite]] ({{Fchim|SnO|2}}). Tout comme pour le plomb, il s'agit de réaliser une [[oxycombustion]] qui apportera la chaleur et les gaz réducteurs nécessaires à la désoxydation du [[dioxyde d'étain]]. À la fin de la fusion réductrice, l'étain métallique est coulé. Mais les scories restant dans le convertisseur contiennent encore une quantité non négligeable d'étain combiné avec du fer<ref name=Cuyper>{{chapitre |langue= fr |
||
|prénom1= Jacques |nom1= de Cuyper |
|prénom1= Jacques |nom1= de Cuyper |
||
|titre chapitre= Métallurgie et recyclage de l’étain - Traitements métallurgiques |
|titre chapitre= Métallurgie et recyclage de l’étain - Traitements métallurgiques |
||
Ligne 254 : | Ligne 259 : | ||
|éditeur= [[Éditions techniques de l'ingénieur]] |
|éditeur= [[Éditions techniques de l'ingénieur]] |
||
|jour= 10 |mois= mars |année= 1999}}</ref>. La méthode d'extraction de cet étain scorifié, mise au point en 1974 par la Metallo-Chimique<ref name=metallo/>, consiste en une addition de [[soufre]] ([[Soufre (minéral)|soufre]] pur ou [[pyrite]]) qui, en se combinant à l'étain, permet aux [[Or mussif|sulfures d'étain]] de s'échapper sous forme gazeuse<ref name=Cuyper/>. |
|jour= 10 |mois= mars |année= 1999}}</ref>. La méthode d'extraction de cet étain scorifié, mise au point en 1974 par la Metallo-Chimique<ref name=metallo/>, consiste en une addition de [[soufre]] ([[Soufre (minéral)|soufre]] pur ou [[pyrite]]) qui, en se combinant à l'étain, permet aux [[Or mussif|sulfures d'étain]] de s'échapper sous forme gazeuse<ref name=Cuyper/>. |
||
== Le procédé == |
|||
=== Le convertisseur === |
|||
[[image:Kaldo Converter sketch en.png|gauche|vignette|lang=fr|upright=1.5|Croquis d'un convertisseur Kaldo.|alt=schéma en perspective]] |
|||
Le convertisseur est conçu comme une [[bétonnière]]. En fonctionnement, il est légèrement incliné par rapport à l'horizontale et tourne à environ {{unité|30|tr/min}}. L'oxygène est injecté par une lance, et les additions destinées à amender le laitier par une autre. La rotation assure un bon mélange, et accélère les réactions chimiques ; mais elle augmente considérablement les coûts de construction comme d'entretien<ref name=NewSientist244/>. Par contre, l'agitation de bain étant moins violente que dans le procédé LD, le laitier mousse peu et il est alors plus facile de suivre l'évolution de l'affinage<ref name=Bhardwaj/>. |
|||
L'autre originalité du procédé réside dans l'injection partielle de l'oxygène dans le bain pour l'affinage proprement dit. L'oxygène excédentaire est consommé par la combustion du [[Monoxyde de carbone|CO]] en [[Dioxyde de carbone|{{fchim|CO|2}}]] dans l'enceinte du four. La chaleur produite par la réaction est absorbée par les réfractaires, qui la restituent au métal lorsque le mouvement de rotation les met en contact. Ainsi, les réfractaires, outre leur sollicitation mécanique due à la rotation, subissent un cycle thermique extrêmement sévère puisque c'est le métal en fusion qui les refroidit<ref name=Bhardwaj/>{{,}}<ref name=DanielRivet/>! |
|||
La vitesse de rotation est variable selon les phases du soufflage. Elle dépasse rarement {{unité|30|tr/min}}. Le convertisseur peut également s'incliner dans toutes les positions. Pendant le soufflage, l'inclinaison se situe entre 16° et 20° par rapport à l'horizontale. De même, la lance à oxygène, refroidie à l'eau, est inclinée entre 20° et 37° par rapport à l'horizontale. Elle est souvent animée d'un mouvement oscillant{{note|L'oscillation de la lance peut être utile en début de soufflage, pour balayer les réfractaires afin d'éviter qu'une croute isolante de laitier se forme et limite l'échange de chaleur entre le métal et le revêtement réfractaire.|group=note}}. Les fumées, chaudes, sont évacuées par une hotte refroidie qui vient se plaquer contre le bec du convertisseur. Cette hotte est conçue de manière à permettre le passage de la lance à oxygène ainsi que la jetée d'additions dans la cornue<ref name=Bhardwaj/>. |
|||
L'émulsion du laitier étant assez limitée, les Kaldos sont plus petits que les convertisseurs LD de capacité identique. On compte en général un volume interne de {{unité|0.5|m³/t<sub>acier</sub>}}, contre {{unité|0.75|m³/t<sub>acier</sub>}} pour les convertisseurs LD, sachant que les fontes riches en phosphore nécessitent un laitier abondant, qui occupe l'espace au détriment du métal<ref name=Bhardwaj/>. |
|||
Le revêtement réfractaire peut être celui mis au point par [[Sidney Gilchrist Thomas]], c'est-à-dire en [[dolomie]] cuite avec du [[goudron]]. Mais ce revêtement, quoique bon marché, ne permet pas d'élaborer plus d'une soixantaine de charges<ref name=ProcedimientoStoraKal-Do/>{{,}}<ref name=Bhardwaj/> : les briques en [[magnésie]] sont généralement nécessaires pour permettre une production sans interruption. En effet, étant donnée la courte durée de vie du revêtement réfractaire, un minimum de deux convertisseurs est nécessaire : pendant qu'un convertisseur est en maçonnage, l'autre est opérationnel. Quand le convertisseur est de petite taille, la cornue est amovible et un [[pont roulant]] la transporte vers un atelier de maçonnage<ref name=Bhardwaj/>. Pour les gros Kaldos sidérurgiques, l'entretien des mécanismes devient critique et il devient préférable d'avoir deux convertisseurs complets, les outils nécessaires étant amenés sur le convertisseur en réfection<ref name=Johansson>{{lien web |langue= en |
|||
|titre= The Kaldo Process |
|||
|jour= 2 |mois= octobre |année= 1963 |
|||
|prénom1= F. |nom1= Johansson |
|||
|lire en ligne= https://open.unido.org/api/documents/4688082/download/THE%20KALDO%20PROCESS%20(03598.en)}}</ref>. |
|||
Les convertisseurs à l'oxygène pur ne peuvent pas fonctionner sans une unité de traitement des gaz chauds, mais le Kaldo ne nécessite qu'un petit dépoussiérage classique. En effet, les convertisseurs à l'oxygène sont soit équipés d'une installation complexe de récupération du gaz pour une autre utilisation, soit brûlent leur gaz à sa sortie du convertisseur, avant de traiter les fumées obtenues dans un dépoussiérage compatible avec les volumes et les températures générées. En comparaison, le Kaldo génère des volumes réduits de fumées essentiellement constituées de poussières, de {{fchim|CO|2}} et d'une faible quantité de CO<ref name=Johansson/>. |
|||
Dans la métallurgie des non ferreux, en particulier celle concernant le recyclage de déchets ou le traitement de [[Élément-trace métallique|métaux lourds]], les Kaldos-TBRC sont installés dans des enceintes closes en légère dépression<ref name=BREF/>. |
|||
=== Conversion de la fonte === |
|||
==== Déroulement d'un soufflage ==== |
|||
Le principe général de l'affinage est identique à tous les convertisseurs : il s'agit d'une oxydation des éléments indésirables comme le carbone, le silicium, le phosphore{{etc}}<ref name=Bhardwaj/> |
|||
La chaux et les ferrailles sont enfournées en premier, puis la fonte en fusion. On limite la quantité de ferrailles pour éviter que la fonte ne se solidifie complètement sur la masse de ferrailles. Le reste de ferrailles, qui peut atteindre la moitié de la quantité totale, est enfourné au plus tôt {{unité|10|minutes}} après le début du soufflage<ref name=Bhardwaj/>. |
|||
[[image:Affinage convertisseur Kaldo.svg|vignette|gauche|upright=1.9|lang=fr|Évolution de la composition chimique pendant le soufflage. La teneur en fer est relative au laitier, les autres éléments sont pris dans le métal.|alt=courbes de la composition chimique]] |
|||
Le soufflage commence immédiatement après la mise en place de la hotte, et atteint son maximum au bout de quelques minutes. La vitesse de rotation est également maximale, soit environ {{unité|30|tr/min}}. Le métal tombe en pluie dans l'atmosphère oxydante du convertisseur, ce qui favorise sa décarburation. De même, les réactions avec le laitier sont favorisées par l'augmentation de la surface de réaction : combinée avec le milieu oxydant, cette configuration permet de commencer la déphosphoration immédiatement{{note|rappeler la chimie du procédé thomas|group=note}}{{,}}<ref name=Bhardwaj/>. |
|||
{{unité|20|minutes}} après le début de soufflage, toutes ferrailles sont refondues. Le débit d'oxygène est alors réduit de moitié, la rotation est ralentie entre {{unité|10|et=12|tr/min}}. La lance souffle au ras du bain : l'objectif est d'oxyder au maximum la charge pour continuer la déphosphoration. Mais le laitier, dont la basicité est maintenue, voire renforcée, par des additions de chaux, s'enrichi en FeO : il devient alors de plus en plus visqueux, jusqu'à former un garni isolant à l'intérieur du convertisseur. Le métal ne peut plus recevoir de chaleur du réfractaire, tandis que les pertes en fer augmentent<ref name=Bhardwaj/>. |
|||
Par conséquent, il est nécessaire de vidanger le laitier tant que celui-ci est encore fluide et dépourvu de fer. Mais la déphosphoration nécessite une certaine quantité de laitier. Avec une addition de chaux, on recrée donc une faible quantité de laitier, mais celui-ci est pur et fortement basique<ref name=Bhardwaj/>. |
|||
Pendant la déphosphoration, le convertisseur tourne de plus en plus lentement, entre {{unité|6|et=8|tr/min}}. Le laitier, très visqueux, devient progressivement une croûte solide. À la fin du soufflage, on perce cette croûte, et le métal est vidangé tandis que le laitier reste dans le convertisseur<ref name=Bhardwaj/>. |
|||
À la coulée suivante, ce laitier, riche en chaux, en fer et en oxygène, réagit la fonte<ref name=Bhardwaj/> : |
|||
* l'oxyde de fer est réduit par le carbone de la fonte : il y a production de monoxyde de carbone et le laitier restitue le fer ; |
|||
* le silicium de la fonte est oxydé en silice : le laitier perd son caractère ultra-basique et redevient fluide. |
|||
La chaleur produite par la combustion du CO en {{fchim|CO|2}} est le triple de celle obtenue par la formation du CO. La combustion totale du carbone apporte {{unité|25121|kJ/kg}} et, avec une gestion appropriée de la lance, il est possible d'oxyder 90 % du carbone de la fonte<ref name=Johansson/>. |
|||
==== Performances ==== |
|||
Contrairement aux procédés anciens (Bessemer, Martin ou Thomas) dopés avec l'adjonction d'oxygène qui conservent de strictes impositions sur la qualité de la fonte traitée, le procédé Kaldo est capable de traiter n'importe quel type de fonte. La charge peut être composée de 25 %<ref name=NewSientist38/> à 45 % de ferrailles<ref name=NewSientist399>{{article |langue= en |
|||
|prénom1= Fred |nom1= Wheeler |
|||
|titre= Computer chain of command in a steelworks |
|||
|périodique= New Scientist |lien périodique= New Scientist |
|||
|jour= 9 |mois= juillet |année= 1964 |
|||
|volume= 23 |numéro= 399 |
|||
|page= 83-84 |
|||
|lire en ligne= https://books.google.fr/books?id=zN9RssYgpvEC&pg=PA83#v=onepage&q&f=false}}</ref>. Un des grands avantages du procédé Kaldo est de pouvoir favoriser la déphosphoration indépendamment de la décarburation, en orientant le jet d'oxygène à l'interface métal-laitier afin de favoriser les réactions entre ces deux liquides<ref name=SharonKaldo>{{article |langue=en |
|||
|prénom1= R. N. |nom1= Merk |
|||
|prénom2= D. R. |nom2= Berg |
|||
|mois= septembre |année= 1961 |volume= 13 |
|||
|périodique= JOM (Journal of the Minerals, Metals & Materials Society) |
|||
|titre= Sharon Steel's Kaldo Furnaces first in US |
|||
|passage= 635-636 |
|||
|lire en ligne= https://link.springer.com/article/10.1007%2FBF03378107}}</ref> : |
|||
{| class="wikitable center" style="text-align:center; width:50%;" |
|||
|+ Influence des paramètres de soufflage<ref name=Bhardwaj/> : |
|||
!scope="col" width="20%" | |
|||
!scope="col" | Vitesse de rotation |
|||
!scope="col" | Vitesse du jet d'oxygène |
|||
!scope="col" | Hauteur de la lance |
|||
!scope="col" | Angle lance/bain |
|||
|- |
|||
! scope=row | Désilication |
|||
| rapide |
|||
| faible |
|||
| |
|||
| |
|||
|- |
|||
! scope=row | Décarburation |
|||
| rapide |
|||
| élevée |
|||
| bas |
|||
| pénétrant |
|||
|- |
|||
! scope=row | Déphosphoration |
|||
| lent |
|||
| faible |
|||
| haut |
|||
| rasant |
|||
|- |
|||
! scope=row | Combustion du CO |
|||
| rapide |
|||
| |
|||
| |
|||
| rasant |
|||
|} |
|||
Le transfert de chaleur se fait de gaz à liquide, ce qui explique des durées d'affinage plus importante que les dérivés du LD, où peu d'échanges de chaleur ont lieu<ref name=Johansson/> : {{unité|70|minutes}} contre 40 pour une charge LD<ref name="Soleild'acier"/>. Dans les [[années 1960]] le principal procédé concurrent du Kaldo est le procédé LD-AC. Un critère de choix du LD-AC au détriment du Kaldo est la rapidité d'affinage : ainsi, les usines habituées au [[procédé Thomas]] (comme la {{Lien|Stewarts & Lloyds}} à [[Corby]]) ont souvent préféré les dérivés du procédé LD, alors que celles qui exploitaient le [[procédé Martin-Siemens]] (comme la [[Park Gate iron manufacturing company|Park Gate]] à [[Rotherham]]), privilégiant la qualité à la productivité, ont préféré le Kaldo<ref>{{Harvsp|Allen|1967|p=203-205}}</ref>. |
|||
L'usure du réfractaire est le gros inconvénient du Kaldo : à l'[[Usine sidérurgique de Gandrange-Rombas|aciérie de Gandrange]], {{unité|425|m³}} de réfractaires étaient consommés en 160 coulées (une semaine de production), contre 250 coulées à la même époque pour l'OLP<ref name=JeanRivet/>. En 1978, les réfractaires de l'OLP tiennent 400 coulées, ceux du LD 600 coulées, alors que ceux du Kaldo n'ont pas du tout progressé<ref name=DanielRivet>{{ouvrage |
|||
|prénom1= Daniel |nom1= Rivet |
|||
|titre= [[Référence:L'acier et l'industrie sidérurgique (Daniel Rivet)|L'acier et l'industrie sidérurgique]] |
|||
|collection= Que sais-je? |numéro dans collection= 561 |
|||
|éditeur= Presses universitaires de France |lien éditeur= Presses universitaires de France |
|||
|lieu= Paris |année= 1978 |
|||
|pages totales= 128 |
|||
|passage= 37 |
|||
|isbn= 2 13 035632 X}}</ref>. |
|||
{| class="wikitable center" style="text-align:center; width:50%;" |
|||
|+ Durée de vie du revêtement réfractaire : |
|||
!scope="col" width="20%" | |
|||
!scope="col" | Kaldo<br>{{petit|Dolomie-goudron}} |
|||
!scope="col" | Kaldo<br>{{petit|Briques magnésiennes}} |
|||
!scope="col" | OLP<br>{{petit|Briques magnésiennes}} |
|||
!scope="col" | LD<br>{{petit|Briques magnésiennes}} |
|||
|- |
|||
! scope=row | Domnavert (1963)<ref name=Johansson/> |
|||
| 85 |
|||
| 272 |
|||
| |
|||
| |
|||
|- |
|||
! scope=row | Gandrange (1969)<ref name=DanielRivet/> |
|||
| |
|||
| 160 |
|||
| 250 |
|||
| |
|||
|- |
|||
! scope=row | Gandrange (1974)<ref name=DanielRivet/> |
|||
| |
|||
| 160 |
|||
| 400 |
|||
| 600 |
|||
|} |
|||
Un convertisseur Kaldo coûte 50 % plus cher qu'un convertisseur LD de capacité interne identique. L'usure des réfractaires est 30 à 50 % plus rapide : les maçonnages qui immobilisent le convertisseur limitent sa production annuelle à 50 à 60 % de celle d'un convertisseur LD de capacité identique<ref>{{ouvrage |langue =en |
|||
|titre= The Planning of Iron and Steelworks |
|||
|prénom1= Friedrich August Karl |nom1= Lüth |
|||
|prénom2= Horst |nom2= König |
|||
|éditeur= Springer-Verlag |lien éditeur= Springer Science+Business Media |
|||
|édition= 3 |année= 1967 |
|||
|pages totales= 193 |
|||
|passage= 79 |
|||
|isbn= 978-3-662-28160-4 |isbn2= 978-3-662-29671-4 |
|||
|lire en ligne= https://books.google.fr/books?id=k0ftCAAAQBAJ&pg=PA79#v=onepage&q&f=false}}</ref>. Et si on prend en compte les plus longues durées de soufflage, la capacité annuelle passe sous les 50 %<ref name="Soleild'acier"/>. |
|||
=== Utilisation dans la métallurgie des non ferreux === |
|||
La différence essentielle entre l'affinage de la fonte par le Kaldo, et le traitement des métaux non ferreux par le TBRC réside en l'utilisation fréquente d'un brûleur [[Oxycombustion|oxy-fuel]] en lieu et place de la lance oxygène<ref name=BackgroundEPA>{{ouvrage |langue= en |format électronique= pdf |
|||
|titre= Background Information For New Source Performance Standards Primary Copper, Zinc, and Lead Smelters Vol I Proposed Standards |
|||
|éditeur= EPA |lien éditeur= Environmental Protection Agency |
|||
|mois= octobre |année= 1974 |
|||
|volume= 1 |passage= 3-115 ; 3-117 |
|||
|lire en ligne= https://nepis.epa.gov/Exe/ZyPDF.cgi/2000X8PS.PDF?Dockey=2000X8PS.PDF}}</ref>. Alors que la lance à oxygène ne permet d'obtenir qu'une oxydation exothermique, le brûleur permet, outre la fusion de métal, d'entretenir des réactions endothermiques. Mais surtout, des réactions de réduction deviennent possibles, élargissant l'utilisation du TBRC à l'affinage de presque tous les métaux. |
|||
La diversité des procédés envisageables (oxydants, réducteurs, avec ou sans [[Scorie (métallurgie)|scorie]]s, exothermiques{{etc}}) fait qu'il n'existe pas, à proprement parler, de « procédé TBRC », mais d'un outil, le convertisseur rotatif, dans lequel un très grand nombre de réactions sont possibles, notamment parce que le brassage du contenu est indépendant de la réaction en cours. Ainsi, l'utilisation du TBRC s'apparente à celle d'un [[four à réverbère]] dont les échanges sont améliorés par l'agitation du bain<ref name=SharonKaldo/>. |
|||
{{Détail image |image= Chemetco Metallo-Chimique Kaldo converters before disassembly.jpg |largeur initiale= 600 |largeur détail= 600 |hauteur détail= 300 |point haut= 50 |point gauche = 0 |position= centre |légende= Alignement des 4 TBRC de la [[Chemetco]] et d'un mélangeur (à droite), en 2011, avant leur démantèlement. Une grande variété de déchets métalliques était traitée en combinant ces outils.|alt= Photo d'un alignement de convertisseurs}} |
|||
==== Traitement du cuivre ==== |
|||
L’utilisation du TBRC pour la fusion des minerais concentrés de [[Sulfure (minéral)|sulfures]] de nickel ([[pentlandite]]) et de cuivre ([[chalcopyrite]]) a été mis au point dans les années 1960 par Inco. Le procédé consiste généralement en trois étapes : la fusion du concentré, l'oxydation de la matte puis sa réduction en métal<ref name=BlazyJdidPyro/>. |
|||
La fusion du minerai peut être réalisée dans un TBRC dédié. Après la phase de chargement du minerai, la charge est portée à fusion (soit {{tmp|1350|°C}}<ref name=BlazyJdidPyro/>) par une lance brûlant du [[gaz naturel]] et de l’oxygène. Le convertisseur est incliné de 15° à 18° mais la rotation ne commence qu’après la formation d’un bain de matte liquide. Du minerai concentré et des [[Fondant (chimie)|fondants]] sont alors ajoutés continuellement jusqu’à ce que la quantité désirée ait été enfournée<ref name=BackgroundEPA/>. |
|||
Le soufflage d’oxygène pur est destiné à évacuer le soufre sous la forme de [[dioxyde de soufre]] ({{fchim|SO|2}}). L’oxydation exothermique des sulfures prolonge la chauffe sans apport de combustible, même si une partie du potentiel thermique a été déjà consommée lors de la phase précédente de fusion (dans le cas ou la fusion a été a été menée de manière oxydante, c’est-à-dire avec un excès d’oxygène)<ref name=BackgroundEPA />. A la fin de cette phase, le convertisseur tourne de {{unité|10|à=25|tr/min}} et la température du bain atteint {{tmp|1600|°C}}. Les fortes températures mises en œuvre nécessitent l’emploi d’un revêtement réfractaire en briques de chrome-[[magnésite]]. Malgré leurs performances, ces briques subissent une usure considérable : pour éviter que la scorie ne dissolve rapidement le réfractaire, on la sature en [[Oxyde de magnésium|magnésie]] et on diminue la température de coulée<ref name=BlazyJdidPyro/>. Le résultat de cette fusion est une [[Matte (métallurgie)#Définitions|matte blanche]], qui ne contient presque plus de fer, mais reste riche en soufre<ref name=BackgroundEPA/>. |
|||
La dernière phase de réduction est obtenue par du coke de pétrole<ref name=BlazyJdidPyro/>. Elle peut être réalisée dans un second TBRC dédié, le premier TBRC recyclant les scories qui se sont enrichies en [[Oxyde de cuivre|oxydes de cuivre]]. Dans ce cas, elle sert essentiellement à récupérer les métaux précieux ([[or]], [[argent]], [[Groupe du platine|platinoïdes]]) contenus dans le minerai<ref name= BackgroundEPA />. |
|||
[[image:RönnskärsverkenRAÄ.jpg|vignette|upright=1.2|L'[[usine métallurgique de Rönnskär]], en [[Suède]], est l'archétype du complexe métallurgique procédant à une valorisation poussée des [[Déchets d'équipements électriques et électroniques|déchets de cuivre]] grâce au TBRC.|alt=skyline d'une usine métallurgique]] |
|||
Cependant, l’extraction de cuivre primaire, c'est-à-dire à partir de minerai concentré, avec un TBRC a été abandonnée dans les années 1970-1980, au profit du soufflage par le fond ([[procédé Manhès-David]] avec un [[convertisseur Peirce-Smith]]), plus productif<ref name=BlazyJdidPyro/>{{,}}<ref name=EMC91/>. À partir des années 1990, Inco réserve le TBRC à la toute dernière étape d’affinage pyrométallurgique, après une [[Séparation par flottaison|flottation]] sélective du « {{lang|en|[[wikt:blister|blister]]}} de cuivre-nickel ». L’étape de fusion est en effet dorénavant réalisée par une [[fusion flash]] et l’oxydation est assurée par un convertisseur Peirce-Smith. Comme pour la sidérurgie, l’utilisation de plusieurs outils spécialisés s'est révélée plus adaptée à la production de masse qu'un unique outil polyvalent<ref name=OxygenCopperCliff/>. Les coûts d’exploitation élevés ont également condamné cette utilisation : |
|||
{{début citation}}Les convertisseurs rotatifs à soufflage par le haut (TBRC) ont été aussi utilisés dans le passé pour l'extration du cuivre primaire. Ils ne sont plus utilisé pour l'extraction primaire, essentiellement à cause des coûts d'exploitation élevés, mais ce type de four est utilisé pour l'extraction secondaire<ref name=BREF/>.{{fin citation|G. Cusano et al.|Best Available Techniques ([[Meilleure technique disponible|BAT]]) Reference Document for the Non-Ferrous Metals Industries}} |
|||
En effet, le TBRC est un four idéal pour le recyclage de [[Déchets d'équipements électriques et électroniques|déchets cuivreux]], qui brûlent très bien dans le four rotatif. Il est possible de constituer une charge composée à 25 % de mélanges cuivreux lors d'un fonctionnement à l'oxygène pur, ou de n'utiliser que des déchets en brûlant du fioul et de l'oxygène avec la lance<ref name=EMC91/>. Par ailleurs, ces déchets peuvent être de nature très variable, avec une teneur en cuivre descendant jusqu'à 10 %<ref>{{lien web |langue= en |format électronique= pdf |
|||
|titre= Outotec Kaldo furnace for copper and lead |
|||
|éditeur= Outotec |lien éditeur= Outotec |
|||
|lois= décembre |année= 2012 |
|||
|url= http://www.outotec.com/ImageVaultFiles/id_933/d_1/cf_2/OTE_Outotec_Kaldo_Furnace_for_copper_and_lead_eng_.PDF}}</ref>. |
|||
Les scories issues du recyclage du cuivre sont chargées en [[Élément-trace métallique|métaux lourds]] mais un petit TBRC dédié s'avère capable d'en récupérer le plomb et l'étain. Ainsi, un [[alliage plomb-étain]] peut être obtenu comme [[sous-produit]] du recyclage du cuivre<ref name=BREF/>{{,}}<ref name=Cuyper/>. Dans ce petit TBRC, le plomb et l’étain sont extraits des scories par une réduction, en présence de [[ferraille]]s et de [[Canette (alimentaire)|cannettes]] [[Étamage|étamées]]. L'alliage est affiné ensuite dans d'autres outils dédiés qui ôtent le cuivre, le nickel et le fer<ref name=BREF/>''. |
|||
==== Traitement du nickel ==== |
|||
Étant données les similitudes entre la [[Extraction du nickel|métallurgie extractive du nickel]] et du cuivre, les procédés mis au point pour l’extraction du nickel sont comparables à l'[[Extraction du cuivre|extraction de cuivre]] à partir de minerai concentré<ref name=BackgroundEPA/>. Le TBRC oxyde la matte de nickel, qui est généralement riche en cuivre, afin d'en retirer le soufre et le fer. Le retrait du fer prépare l'étape suivante d'extraction du nickel par [[carbonylation]] ([[procédé Mond]]){{sfn|Krundwell|Moats|Ramachandran|Robinson|2011|p=271-275}}. |
|||
Comme pour l'extraction de cuivre, l'utilisation d'un TBRC pour le nickel est une alternative au procédé Manhès-David et au [[procédé Ausmelt]]. Mais sa capacité à effectuer une réduction lui permet de traiter plus efficacément des minerais complexes et d'extraire le métal des scories<ref name=ExtractiveNickel>{{ouvrage |langue= en |
|||
|titre= Extractive Metallurgy of Nickel, Cobalt and Platinum Group Metals |
|||
|prénom1= Frank K. |nom1= Krundwell |
|||
|prénom2= Michael S. |nom2= Moats |
|||
|prénom3= Venkoba |nom3= Ramachandran |
|||
|prénom4= Timothy G. |nom4= Robinson |
|||
|prénom5= William G. |nom5= Davenport |
|||
|éditeur= Elsevier |lien éditeur= Elsevier (éditeur) |
|||
|année= 2011 |
|||
|passage= 579-581 |
|||
|pages totales= 610 |
|||
|isbn= 978-0-08-096809-4}}</ref>. |
|||
==== Traitement du plomb ==== |
|||
L'extraction du plomb, industrialisée par l'entreprise suédoise [[Boliden AB]] en 1976 dans son [[usine métallurgique de Rönnskär|usine de Rönnskär]], consiste en trois étapes : la fusion, l'oxydation puis la réduction<ref name=Ronnskar/>. |
|||
La fusion est oxydante. Suivant la nature de la charge, elle peut se faire de deux manières : |
|||
* pour la fusion de minerai concentré (à 72 %<ref name=ForeignNonferrousTechnology>{{ouvrage |langue= en |format électronique= pdf |
|||
|prénom1= A. Christian |nom1= Worrell |
|||
|prénom2= Mary A. |nom2= Taft |
|||
|titre= Overview of foreign nonferrous smelter technology |
|||
|éditeur= EPA |lien éditeur= Environmental Protection Agency |
|||
|mois= juin |année= 1980 |
|||
|passage= 38 |
|||
|lire en ligne= https://nepis.epa.gov/Exe/ZyPDF.cgi/91018I2W.PDF?Dockey=91018I2W.PDF}}</ref>), l'oxydation des minerais sulfurés avec l'oxygène apporté par la lance (air à 60 % d'{{fchim|O|2}}<ref name=ForeignNonferrousTechnology/>) est suffisante pour obtenir la fusion de la [[Matte (métallurgie)|matte]] sans apport de combustible<ref name=EMC91/> ; |
|||
* pour le recyclage de déchets, une lance [[Oxycombustion|oxygène-gaz naturel]] chauffe la charge jusqu'à {{tmp|1050|°C}}<ref name=BlazyJdidPlomb>{{chapitre |langue=fr |
|||
|prénom1= Pierre |nom1= Blazy |
|||
|prénom2= El-Aïd |nom2= Jdid |
|||
|titre chapitre= Métallurgie du Plomb - Procédés modernes et sources secondaires - Procédés BSF |
|||
|titre ouvrage= Techniques de l'ingénieur. Élaboration et recyclage des métaux |
|||
|éditeur= [[Éditions techniques de l'ingénieur]] |
|||
|jour= 10 |mois= septembre |année= 2011}}</ref>. |
|||
L'oxydation du plomb, qui suit la fusion, prolonge cette chauffe car elle est exothermique. Le but de cette étape est d'oxyder un maximum d'impuretés. Dans le cas de la fusion de minerai concentré, il s'agit du soufre qui est évacué sous forme gazeuse ([[Dioxyde de soufre|{{fchim|SO|2}}]]). Les scories s'enrichissent en plomb, jusqu'à contenir 30 % de plomb sous forme de [[litharge]] ([[Oxyde de plomb(II)|PbO]])<ref name=EMC91/>. Dans le cas du recyclage de déchets, de l’oxygène pur est soufflé jusqu'à ce que le bain atteigne une température de {{tmp|1350|°C}}<ref name=BlazyJdidPlomb/>. |
|||
Après cette phase oxydante, qui élimine partiellement les impuretés, on termine dans le même four par une phase de réduction. Cette phase consiste à brûler{{note|Le carbone n'est pas injecté directement dans les scories car la [[Réaction endothermique|réaction est endothermique]]. La réaction entre le coke et le PbO se décompose en effet ainsi : |
|||
{{Retrait|{{Spaces|10}} |
|||
{{fchim|C <small>''(s)''</small> + CO|2| <small>''(g)''</small> → 2 CO <small>''(g)''</small>}}{{Spaces|10}} consommant {{unité|165.4|kJ/mol}} de CO |
|||
}} |
|||
{{Retrait|{{Spaces|10}} |
|||
{{fchim|PbO <small>''(s)''</small> + CO <small>''(g)''</small> → Pb <small>''(l)''</small> + CO|2| <small>''(g)''</small> }}{{Spaces|10}} produisant {{unité|95.8|kJ/mol}} de PbO |
|||
}} |
|||
Le bilan thermique de ces deux réactions est déficitaire : il est alors nécessaire d'apporter de la chaleur<ref name=treatise>{{ouvrage |langue= en |
|||
|prénom1= H. Y. |nom1= Sohn |
|||
|prénom2= M. |nom2= Olivas-Martinez |
|||
|titre= Treatise on Process Metallurgy |
|||
|éditeur= [[Elsevier]] |
|||
|année= 2014 |
|||
|volume= 3 |partie= A |
|||
|isbn= 978-0-08-100000-7 |
|||
|passage= 686-688 |
|||
|lire en ligne= https://books.google.fr/books?id=1p69Wl9rXo4C&pg=PA686#v=onepage&q&f=false}}</ref>.|group=note}} du [[wikt:poussier|poussier]] de [[Coke (charbon)|coke]] de pétrole avec un déficit d'oxygène afin de produire le [[monoxyde de carbone]] chaud qui est le gaz réducteur<ref name=EMC91/>. La [[Réaction carbothermique|carboréduction]] transforme l'oxyde de plomb des scories en plomb métallique, qui retourne dans le bain de métal en fusion<ref name=BlazyJdidPlomb/>. |
|||
Malgré la consommation de {{unité|40|kg}} de coke et {{unité|30|L}} de fioul par tonne de plomb<ref name=BREF/>, ainsi que l'électricité nécessaire à la production d'oxygène, le TBRC est plus économe en énergie que les chauffes nécessaires aux procédés alternatifs<ref name=ForeignNonferrousTechnology/>. Mais ce procédé n’est pas compatible avec de grandes capacités de production. Il est cependant flexible et peut traiter des matériaux très divers (batteries, scraps, etc.)<ref name=BlazyJdidPlomb/>. |
|||
==== Traitement de l'étain ==== |
|||
L'utilisation du TBRC à la métallurgie extractive de l'[[étain]], mise au point en 1974 par la Metallo-Chimique<ref name=metallo/>, consiste à extraire l'étain en deux étapes : une fusion réductrice de concentrés de [[cassitérite]] permet d'obtenir du zinc métallique en fusion, puis une [[Sulfuration (chimie)|sulfuration]] permet de créer du [[Sulfure d'étain(II)|sulfure d'étain]] (SnS) gazeux, qui est capté par le système de traitement des fumées<ref name=Cuyper/>. |
|||
La lance brûle premièrement du combustible (mazout ou gaz) avec de l'oxygène pur, déficitaire vis-à-vis de la [[stœchiométrie]] afin d'obtenir une atmosphère réductrice. Après l'achèvement de cette phase de fusion réductrice du minerai concentré, l'étain métallique brut, qui s'est rassemblé au fond du convertisseur, est coulé<ref name=Cuyper/>. |
|||
La scorie restant dans le four est traitée par plusieurs additions de [[pyrite]], tout en augmentant la vitesse de rotation et en maintenant un rapport {{fchim|O|2}}/gaz naturel de 1,5/1 (de façon à maintenir l'atmosphère réductrice). L'étain de la scorie se combine alors au soufre afin de créer du sulfure d'étain. Ce composé, qui se volatilise au-delà de {{tmp|1180|°C}}, est expulsé hors du four par un jet d'air qui remplace le jet d'oxygène{{note|La [[fonderie d'étain de Texas City]] avait initialement envisagé d'extraire l'étain vaporisé sous la forme de [[dioxyde d'étain]]. Mais cette extraction s'est avérée lente et pénalisante la productivité. Quelques mois plus tard, l'extraction sous la forme de [[Sulfure d'étain(II)|sulfure d'étain]] a été mise au point, multipliant la productivité par quatre<ref name=NoA2408>{{lien web |langue= en |
|||
|titre= State v. Associated Metals & Minerals Corp., No. A2408 |
|||
|jour= 1 |mois= avril |année= 1981 |
|||
|url=https://case-law.vlex.com/vid/state-v-associated-metals-892429169 |
|||
|consulté le=05-05-2023}}</ref>.|group=note}}. La vitesse de rotation est également accrue jusqu’à ce que la scorie ne contienne plus qu'une teneur en étain négligeable (jusqu'à moins de 0,1 % en masse)<ref name=Cuyper/>. |
|||
À la [[fonderie d'étain de Texas City]], aux États-Unis, l'adoption du TBRC à l'extraction de l'étain en 1978 a permis de passer d'un procédé complexe combinant plusieurs fours, à une seule opération dans un TBRC tournant à grande vitesse<ref name=TexTinRecordDecision>{{ouvrage |langue= en |format électronique= pdf |
|||
|titre= Superfund record of decision : Texas Tin Corporation Site OU 1, Texas City, TX. |
|||
|éditeur= EPA |lien éditeur= Environmental Protection Agency |
|||
|jour= 17 |mois= mai |année= 1999 |
|||
|passage= 17 |
|||
|lire en ligne= https://nepis.epa.gov/Exe/ZyPDF.cgi/10002M14.PDF?Dockey=10002M14.PDF}}</ref>. Concentrer les opérations dans un seul outil a notamment simplifié la mise en conformité environnementale de l'usine<ref name=NoA2408/>. |
|||
''Pour l'extraction de l'étain,'' l’emploi d'oxygène pur minimisant le volume des fumées, four rotatif peut transférer efficacement leur chaleur au bain<ref name=Cuyper/>. |
|||
==== Traitement des métaux précieux ==== |
|||
L'extraction des [[Métal précieux|métaux précieux]], notamment ceux du [[groupe du platine]], se caractérise par les faibles quantités de produits à traiter, notamment dans les étapes finales. Dans ce contexte, certains procédés ne sont pas adaptés : l'affinage des [[Matte (métallurgie)|mattes]] concentrées en éléments précieux, obtenues lors du traitements de minerais sulfurés de nickel et de cuivre ne peut pas être fait classiquement dans un [[convertisseur Peirce-Smith]] car son soufflage sous le bain impose de mettre en œuvre une quantité minimale (plusieurs tonnes) de produit. Le TBRC est alors utilisé car, même miniaturisé, il reste efficace : la raffinerie de platine d'[[Acton (Londres)|Acton]] opère ainsi un TBRC de {{unité|0.25|m|3}} tournant à {{unité|2|tr/min}}<ref name=ExtractiveNickel/>. |
|||
Les faibles quantités condamnent également les procédés continus. Le TBRC étant capable de refondre des lots de produits, il est systématiquement utilisé comme outil de fusion. Après un affinage pyrométallurgique, généralement oxydant et souvent suivi d'une réduction, il prépare la matte pour l'étape suivante de séparation des éléments par [[lixiviation]]<ref name=ExtractiveNickel/>. |
|||
Les TBRC sont adaptés au traitement d'une grande variété de produits contenant des métaux précieux : les [[Procédé Merrill-Crowe|précipités de Merrill-Crowe]], les croutes de zinc issues de la désargentisation du plomb, les boues d'anodes issues de l’[[Électrolyse|affinage électrolytique]] du plomb et du cuivre, des déchets électroniques, des chûtes et des déchets de [[Pellicule photographique|pellicules photographiques]]<ref name=Proceedings>{{Chapitre |langue= en |
|||
|auteurs ouvrage= George Kachaniwsky, Chris Newman |
|||
|titre ouvrage= The impact of oxygen on the productivity of non-ferrous metallurgical processes |
|||
|titre chapitre= Bulk oxygen use in the refining of precious metals |
|||
|prénom1= J.G. |nom1= Cooper |
|||
|prénom2= J.W. |nom2= Matousek |
|||
|prénom3= J.G. |nom3= Whellock |
|||
|volume= 2 |titre volume= Proceedings of the Metallurgical Society of the Canadian Institute of Mining |
|||
|lieu= Winninpeg |éditeur= [[Pergamon Press]] |
|||
|jour= 23-26 |mois= août |année= 1987 |
|||
|isbn= 0-08-035767-9 |
|||
|lire en ligne= https://books.google.fr/books?id=mAMcBQAAQBAJ&pg=PA116&lpg=PA116#v=onepage&q&f=false |
|||
|passage= 116-118}}</ref>, des cendres, des poussières, des boues<ref name=BREF/>… Dans tous ces usages, ils ont remplacé les [[Four à réverbère|fours à réverbères]] traditionnellement utilisés, à cause de leur plus grande efficacité et productivité<ref name=Proceedings/>. |
|||
La valeur, la complexité et les volumes traités impliquent des méthodes de travail particulières. Par exemple, l'[[usine métallurgique de Rönnskär]], en [[Suède]], dont un des 3 TBRC qu'elle opère est dédié à la récupération des métaux précieux, isole cette activité dans une unité distincte<ref>{{ouvrage |langue= en |format électronique= pdf |
|||
|titre= Mapping of settling processes at Boliden Rönnskär and Harjavalta smelters |
|||
|prénom= Jane |nom= Mulenshi |
|||
|éditeur= [[Université de technologie de Luleå]] |
|||
|nature ouvrage= thèse |
|||
|jour= 15 |mois= juin |année= 2015 |
|||
|lire en ligne= http://www.diva-portal.se/smash/get/diva2:1026572/FULLTEXT02.pdf}}</ref>. |
|||
==== Autres métallurgies ==== |
|||
[[image:Tilting Rotary Furnace.svg|droite|vignette|lang=fr|upright=1.2|Principe du four TRF (''{{Langue|en|texte=Tilting Rotary Furnace}}''), un TBRC simplifié.|alt=schéma du TRF]] |
|||
Le TBRC est un outil adapté au [[Crasse (métallurgie)#Crasses d'aluminium|traitement des crasses d'aluminium]]<ref name=Wibner>{{article |langue= en |
|||
|prénom1= Stefan |nom1= Wibner |
|||
|prénom2= Helmut |nom2= Antrekowitsch |
|||
|prénom3= Thomas C. |nom3= Meisel |
|||
|titre= Studies on the Formation and Processing of Aluminium Dross with Particular Focus on Special Metals |
|||
|périodique= Metals |
|||
|éditeur= [[MDPI]] |
|||
|date= 12-07-2021 |volume= 11 |passage= 1108 |
|||
|lire en ligne= https://www.mdpi.com/2075-4701/11/7/1108 |
|||
|doi= 10.3390/met11071108}}</ref>. Les procédés les plus courants consistent à refondre{{note|Certains auteurs qualifient l'utilisation du TBRC de [[centrifugation]]<ref name=Langlois/>. Mais la vitesse de rotation, de {{unité|1|tr/min}}, est bien trop faible pour produire cet effet<ref name=Wibner/>. Surtout, la description détaillée du procédé ECOCENT indique que les [[Crasse (métallurgie)|crasses]] d'aluminium sont centrifugées dans un outil distinct<ref name=Pollmann>{{Brevet|CA|2915784A1|"{{Langue|en|texte=Aluminium dross processing}}", Frank Pollmann, 2014.}}</ref>.|group=note}} à environ {{tmp|800|°C}} dans un four rotatif les particules d'[[aluminium]] retirées des [[Crasse (métallurgie)|crasses]] de fonderie, les variantes consistant essentiellement à limiter l'oxydation du métal pendant cette fusion par l'amélioration de la méthode de chauffe (oxycombustion, [[arc électrique]], [[torche à plasma]],…) ou par la protection du bain (protégé par une couche de [[sel fondu]])<ref name=Langlois>{{ouvrage |format électronique= pdf |
|||
|titre= Revue des technologies de traitement des écumes des écumes d'aluminium et applicabilité dans un cadre de développement durable au Québec |
|||
|prénom= Simon |nom= Langlois |
|||
|nature ouvrage= thèse |
|||
|mois= juillet |année= 2012 |
|||
|lieu= [[Sherbrooke]] |
|||
|éditeur= [[Université de Sherbrooke]] |
|||
|lire en ligne= https://www.usherbrooke.ca/environnement/fileadmin/sites/environnement/documents/Essais2012/Langlois_S__13-07-2012_.pdf}}</ref>. Pour cette application, cependant, le TRF (''{{Langue|en|texte=Tilting Rotary Furnace}}''), un four similaire au TBRC mais doté d'un mécanisme de basculement plus simple et d'angle limité, est un choix industriellement plus économique<ref name=TRF>{{lien web |langue= en |
|||
|titre= Rotary-tilting furnace of the company INTEC (Germany) with the liner of the company "Spetsogneuporkomplekt" |
|||
|url= http://www.spetsogneupor.ru/en/stati/stati-10-rotor-pech.html |
|||
|consulté le= 20-02-2023}}</ref>. |
|||
Le TBRC peut-être également utilisé pour extraire des éléments par [[vaporisation]]. Le traitement des fumées permet de récupérer les poussières émises : le [[sélénium]] est, par exemple, efficacement récupéré par cette méthode<ref name=BREF/>. |
|||
=== Élaboration des aciers inoxydables === |
|||
Le procédé Kaldo a eu une brêve descendance dans l'élaboration des [[acier inoxydable|aciers inoxydables]], avec le procédé Kaldo-réacteur (ou Kaldo-Vac<ref name=Saleil>{{article |format électronique= pdf |
|||
|url= https://www.mattech-journal.org/articles/mattech/pdf/2020/01/mt190075.pdf |
|||
|titre= La production des aciers inoxydables : Histoire de son développement et des procédés de fabrication |sous-titre= Partie II. Évolutions de l’élaboration des aciers inoxydables au four électrique à arc. La tentation de la fonte au chrome et la production d’aciers inoxydables dans l’usine intégrée |
|||
|prénom1= Jean |nom1= Saleil |
|||
|prénom2= Marc |nom2= Mantel |
|||
|prénom3= Jean |nom3= Le Coze |
|||
|périodique= Matériaux & Techniques |volume= 108 |numéro= 1 |
|||
|jour= 15 |mai= mai |année= 2020 |
|||
|éditeur= Société Chimique de France |lien éditeur= Société chimique de France |
|||
|doi= /10.1051/mattech/2020017}}</ref>) mis au point en 1955 par [[Ugitech|Ugine]] à son usine d'[[Aiguebelle (Savoie)|Aiguebelle]]<ref name="Soleild'acier">{{Lien web |
|||
|url= http://soleildacier.ouvaton.org/savoir/fr/02W1115A.HTM |
|||
|titre= Un siècle d'oxygène en sidérurgie |
|||
|auteur= Olivier C. A. Bisanti |
|||
|date= 15 janvier 2003 |
|||
|éditeur= Soleil d'acier}}</ref>. En effet, la production d’[[Acier inoxydable|aciers inoxydables]] présente des particularités qui rejoignent les points forts du procédé : élaboration à partir de ferrailles et obtention économique de hautes températures (plus de {{tmp|1700|°C}}). Il ne manque alors qu'à terminer l’affinage oxydant en raccordant la cornue à un [[Pompe à vide|générateur de vide]], afin de décarburer sans oxyder le chrome, jusqu’aux très basses teneurs en carbone requises par les aciers inoxydables<ref name=Saleil/>. La combinaison entre ce convertisseur et l'installation de vide a abouti à un outil aussi original que performant : |
|||
{{début citation}}Cet appareil était un pur fruit de la culture uginoise, un vrai délire d'ingénieur : exploité en Kaldo durant la première partie du soufflage, la bétonnière était ensuite arrêtée et mise en position verticale ; une cloche à vide venait alors se [[wikt:clamper|clamper]] sur le bec afin de provoquer une décarburation sous vide. Le savoir-faire d'Ugine avait su faire porter la durée de la campagne d'un garnissage à {{unité|1000|coulées}}<ref name="Soleild'acier"/>.{{fin citation|Olivier C. A. Bisanti|Un siècle d'oxygène en sidérurgie}} |
|||
Deux convertisseurs de {{unité|70|tonnes}} sont construits dans ses usines de [[Moûtiers]] et de [[Laudun-l'Ardoise|L'Ardoise]]<ref name="Soleild'acier"/>. Ugine avait également projeté une installation identique à [[Fos-sur-Mer]], pour élargir à la production d'acier inoxydable son usine démarrée en 1973 et dédiée principalement aux aciers à roulements. Mais la crise qui sinistre la métallurgie à partir du milieu des années 1970 a raison du projet. La généralisation du [[procédé AOD]] marginalise ensuite le Kaldo-réacteur : en 1982 l'usine de [[Moûtiers]] ferme, victime de sa faible taille et de son obsolescence<ref>{{Ouvrage |langue= fr |
|||
|auteur1= Louis Chabert |
|||
|titre= Histoire de l'électrochimie et de l'électrométallurgie en Savoie |
|||
|lieu= Chambéry |
|||
|éditeur= [[Société savoisienne d'histoire et d'archéologie]] |
|||
|année= 1987 |
|||
|pages totales= 36 |
|||
|passage= 19-36}}</ref>, et l’usine de L’Ardoise s'équipe d'un convertisseur AOD<ref name=Saleil/> de {{unité|110|tonnes}} destiné à remplacer son Kaldo-réacteur qui s'arrête en 1986<ref name="Soleild'acier"/>. |
|||
== Usines construites == |
|||
=== Sidérurgie === |
|||
{| class="wikitable center" style="width:100%;" |
|||
|+ Usines {{note|Les convertisseurs expérimentaux ne sont pas détaillés. Dans cette catégorie, on peut signaler le Kaldo prototype initial de Domnarvet d'une capacité de {{unité|3|tonnes}} et celui du {{Lien |fr=Swerea MEFOS |lang=sv |trad= Swerea MEFOS |texte= MEFOS}} à [[Luleå]] de {{unité|5|tonnes}}. Les convertisseurs qui n'ont pas connus d'histoire industrielle, notamment les 2 Kaldos de {{unité|60|tonnes}} que la ''Sanyo Special Steel Co.'' a commandé à [[Krupp (entreprise)|Krupp]] pour l'aciérie d'[[Himeji]] en 1965, soit au moment de sa faillite et de son passage à la production au [[four à arc électrique]], et pour lesquels aucune production n'a été relevée<ref>{{lien web |lang= en |
|||
|titre= History |
|||
|éditeur= Sanyo Special Steel |
|||
|url= http://www.sanyo-steel.co.jp/english/company/history.html}}</ref>{{,}}<ref>{{article |langue=en |
|||
|périodique= Metal Bulletin Journals |
|||
|titre= World Kaldo steel plants |
|||
|année= 1971 |mois= février |
|||
|passage= 57}}</ref>, ne sont pas retenus. De même, le Kaldo-LD {{unité|70|tonnes}} qui aurait été installé en 1973 à [[Cockerill-Sambre|Cockerill]]-[[Marcinelle]]<ref name=Bhardwaj/>, qui n'apparait dans aucune archive relative à l'usine et dont la date de construction correspond en fait à la fermeture de l’aciérie Thomas où il aurait dû être installé, a certainement été abandonné au profit du procédé OBM<ref>{{article |
|||
|prénom1= H. |nom1= Jacobs |
|||
|prénom2= A. |nom2= Marlot |
|||
|prénom3= L. |nom3= Philippe |
|||
|prénom4= E. |nom4= Lété |
|||
|périodique= Revue de Métallurgie |lieu= Paris |
|||
|volume= 79 |numéro= 1 |mois= janvier |année= 1982 |
|||
|passage= 13–27 |
|||
|titre= L’aciérie OBM de Cockerill-Sambre à Marcinelle |
|||
|doi= 10.1051/metal/198279010013 |
|||
|lire en ligne= https://www.metallurgical-research.org/articles/metal/abs/1982/01/metal19827901p13/metal19827901p13.html}}</ref>.|group=note}} Kaldo construites |
|||
!scope="col" width="7%" | Nombre de fours |
|||
!scope="col" width="12%" | Emplacement |
|||
!scope="col" width="12%" | Propriétaire<br>à la mise en service |
|||
!scope="col" width="8%" | Capacité (t) |
|||
!scope="col" width="8%" | Date de mise en service |
|||
!scope="col" width="8%" | Date d’arrêt |
|||
!scope="col" width="45%" | Remarques |
|||
|- |
|||
| 1 || [[Usine sidérurgique de Borlänge|Domnarvets Jernverk]]<br>(Suède) || [[Stora AB|Stora Kopparbergs Bergslags AB]] || 30 || 1956<ref name=Allen141/>{{,}}<ref name=Bhardwaj/> || 1974<ref name=YearBook1976>{{ouvrage |langue= en |
|||
|titre= Year Book - Association of Iron and Steel Engineers |
|||
|passage= 83 |
|||
|année= 1976}}</ref> || Démonstrateur industriel. Transformé en OBM de {{unité|35|t}} en 1974<ref name=YearBook1976/>. |
|||
|- |
|||
| 1 || [[Usine sidérurgique de Florange|Aciérie de Florange]]<br>(France) || [[Sollac]] || 110<ref name="Soleild'acier"/><br>porté à 140<ref name=Thouvenin/> || 1960 || 1980 || Arrêté en même temps que 4 convertisseurs Thomas de {{unité|65|tonnes}} modifiés en LWS, et 4 Martin, au moment de la mise en service des 2 convertisseurs LWS de {{unité|240|tonnes}}<ref name=Thouvenin/>. |
|||
|- |
|||
| 2 || [[Usine sidérurgique d'Oxelösund|Oxelösunds Järnverks]]<br>(Suède) || [[Gränges|Gränges AB]] || 130 || 1961<ref name=Allen141/> || 1977<ref name=YearBook1984>{{ouvrage |langue= en |
|||
|titre= Year Book - Association of Iron and Steel Engineers |
|||
|passage= 439 |
|||
|année= 1984}}</ref> || En 1967, 2 Kaldos supplémentaires sont annoncés<ref name=yearbook1967>{{ouvrage |langue= en |format électronique= pdf |
|||
|prénom1= John W. |nom1= Thatcher |
|||
|titre= Mineral yearbook |
|||
|année= 1967 |
|||
|passage= 601 |
|||
|lire en ligne= http://images.library.wisc.edu/EcoNatRes/EFacs2/MineralsYearBk/MinYB1967v1and2/reference/econatres.minyb1967v1and2.jthatcher.pdf}}</ref>, mais un seul LD-LBE de {{unité|170|t}} à cornue remplaçable<ref name=YearBook1984/> remplace les 2 Kaldos en 1977<ref name=Handelsstals>{{ouvrage |langue= sv |format électronique= pdf |
|||
|titre= Handelsståls industrin inför 1980-talet |
|||
|année= 1977 |lieu= Stockholm |
|||
|passage= 92-93 ; 97 |
|||
|isbn= 91-38-03332-1 |issn= 0375-250X |
|||
|lire en ligne= http://weburn.kb.se/sou/329/urn-nbn-se-kb-digark-3281121.pdf}}</ref>. |
|||
|- |
|||
| 2 || Roemer Works<br>(États-Unis) || [[Sharon Steel Corporation]] || 140<br>porté à 150<ref>{{ouvrage |langue= en |
|||
|titre= Basic oxygen process furnaces |
|||
|mois= janvier |année= 1977 |
|||
|éditeur= United States Environmental Protection Agency |lien éditeur= Environmental Protection Agency |
|||
|passage= 3-5 |
|||
|lire en ligne= http://nepis.epa.gov/Exe/ZyNET.exe/9100Z099.txt?ZyActionD=ZyDocument&Client=EPA&Index=2011%20Thru%202015%7C1995%20Thru%201999%7C1981%20Thru%201985%7C2006%20Thru%202010%7C1991%20Thru%201994%7C1976%20Thru%201980%7C2000%20Thru%202005%7C1986%20Thru%201990%7CPrior%20to%201976%7CHardcopy%20Publications&Docs=&Query=%28kaldo%29%20OR%20FNAME%3D%229100Z099.txt%22%20AND%20FNAME%3D%229100Z099.txt%22&Time=&EndTime=&SearchMethod=1&TocRestrict=n&Toc=&TocEntry=&QField=&QFieldYear=&QFieldMonth=&QFieldDay=&UseQField=&IntQFieldOp=0&ExtQFieldOp=0&XmlQuery=&File=D%3A%5CZYFILES%5CINDEX%20DATA%5C76THRU80%5CTXT%5C00000020%5C9100Z099.txt&User=ANONYMOUS&Password=anonymous&SortMethod=h%7C-&MaximumDocuments=15&FuzzyDegree=0&ImageQuality=r85g16/r85g16/x150y150g16/i500&Display=hpfr&DefSeekPage=x&SearchBack=ZyActionL&Back=ZyActionS&BackDesc=Results%20page&MaximumPages=10&ZyEntry=1#}}</ref> || 1962<ref name=Allen141/> || 1980<ref name=IronAndSteel1981>{{article |langue= en |
|||
|périodique= Year Book - Association of Iron and Steel Engineers |
|||
|titre= Worldwide LD steelmaking capacity shows pause |
|||
|prénom1= Joseph K. |nom1= Stone |
|||
|prénom2= Eduard M. |nom2= Michaelis |
|||
|année=1981 |
|||
|passage= 225}}</ref> || Durée de vie du garnissage de {{unité|220|t}}<ref name=SharonKaldo/> : {{unité|120|coulées}}. Charge constituée de fonte non phosphoreuse<ref name=Johansson/> et de 50% de ferrailles. Projet pour un 3{{e}} Kaldo en 1964<ref name=yearbook1964/>. Installation d'un LD {{unité|150|tonnes}} en 1977, puis d'un deuxième en 1980, qui remplacent les Kaldos<ref name=IronAndSteel1981/>. Mais les 2 Kaldos sont {{citation|virtuellement supplantés}} par un seul convertisseur LD dès 1977<ref name=EPAdevelopment>{{ouvrage |langue= en |
|||
|titre= Development of thechnology for controlling BOP charging emissions |
|||
|mois= octobre |année= 1977 |
|||
|éditeur= United States Environmental Protection Agency |lien éditeur= Environmental Protection Agency |
|||
|passage= 11 ; 18 ; 21 |
|||
|lire en ligne= http://nepis.epa.gov/Exe/ZyNET.exe/91016YAJ.txt?ZyActionD=ZyDocument&Client=EPA&Index=2011%20Thru%202015%7C1995%20Thru%201999%7C1981%20Thru%201985%7C2006%20Thru%202010%7C1991%20Thru%201994%7C1976%20Thru%201980%7C2000%20Thru%202005%7C1986%20Thru%201990%7CPrior%20to%201976%7CHardcopy%20Publications&Docs=&Query=%28kaldo%29%20OR%20FNAME%3D%2291016YAJ.txt%22%20AND%20FNAME%3D%2291016YAJ.txt%22&Time=&EndTime=&SearchMethod=1&TocRestrict=n&Toc=&TocEntry=&QField=&QFieldYear=&QFieldMonth=&QFieldDay=&UseQField=&IntQFieldOp=0&ExtQFieldOp=0&XmlQuery=&File=D%3A%5CZYFILES%5CINDEX%20DATA%5C76THRU80%5CTXT%5C00000024%5C91016YAJ.txt&User=ANONYMOUS&Password=anonymous&SortMethod=h%7C-&MaximumDocuments=15&FuzzyDegree=0&ImageQuality=r85g16/r85g16/x150y150g16/i500&Display=hpfr&DefSeekPage=x&SearchBack=ZyActionL&Back=ZyActionS&BackDesc=Results%20page&MaximumPages=10&ZyEntry=20}}</ref>. |
|||
|- |
|||
| 2 || [[Park Gate iron manufacturing company|Park Gate Works]]<br>(Grande-Bretagne) || [[TI Group|Tube Investments]] || 75<br>porté à 80<ref name=Allen141/> || 1964 || 1975<ref>{{article |
|||
|périodique= Revue de métallurgie |lien périodique= Revue de métallurgie |
|||
|titre= Informations économiques |
|||
|année= 1975 |mois= décembre |
|||
|volume= 72 |
|||
|page= 237}}</ref> || Premiers Kaldos britanniques<ref name=NewSientist399/>. |
|||
|- |
|||
| 2 || Aciérie de [[Consett]]<br>(Grande-Bretagne) || [[Consett Iron Company]] || 100<br>porté à 120<ref>{{Harvsp|Allen|1967|p=191}}</ref> || 1964<ref name=Allen141/> || 1968-1971<ref name=IronandSteel1972>{{article |langue= en |
|||
|périodique= Iron and Steel |
|||
|titre= Consett |
|||
|année= 1972 |
|||
|volume= 45 |
|||
|prénom1= Louis |nom1= Cassier |
|||
|éditeur= IPC Science and Technology Press}}</ref> || Aciérie équipée de 2 convertisseurs LD (et non pas LD-AC) et 2 Kaldos, tous de {{unité|100|tonnes}} de capacité. 2 Kaldos supplémentaires étaient prévus<ref>{{lien web |langue= en |
|||
|titre= Consett Iron Company Limited |
|||
|site= derwentside.com |
|||
|url= http://www.derwentside.com/the-consett-story/chapter-three-local-industry}}</ref> mais ne furent jamais construits. En 1966, la production Kaldo est devenue marginale <ref>{{ouvrage |langue= en |
|||
|titre= Some aspects of the effect of atmospheric pollution on the Lichen Flora to the West of Consett Co. Durham |
|||
|prénom1= John L. |nom1= Griffith |
|||
|année= 1966 |
|||
|passage= 14 |
|||
|lire en ligne= http://etheses.dur.ac.uk/9151/1/9151_6082.PDF?UkUDh:CyT}}</ref>, les minerais à bas phosphore devenant bon marché tandis que les performances du LD s'améliorent. En 1968, un Kaldo est transformé en troisième LD de {{unité|150|tonnes}} et, en 1971, le dernier Kaldo transformé de la même manière<ref name=IronandSteel1972/>. |
|||
|- |
|||
| 2 || [[Shelton Bar]]<br>(Grande-Bretagne) || [[John Summers & Sons]] || 50<br>porté à 55<ref name=Shelton150>{{lien web |langue= en |
|||
|titre= 150 years of the Shelton Works |
|||
|site= thepotteries.org |
|||
|url= http://www.thepotteries.org/shelton/150/index.htm |
|||
|passage= 29-33}}</ref> || 1964<ref name=Allen141/> || 1978<ref name=Shelton150/> || Construction associée à celle d'une [[coulée continue]] de [[Bloom (sidérurgie)|blooms]]<ref name=Shelton150/>. |
|||
|- |
|||
| 1 || [[Usine sidérurgique de Luleå|Norrbottens Järnverk]]<br>(Suède)|| [[Usine sidérurgique de Luleå|Norrbottens Järnverk AB]] || 70 || 1964<ref name=Allen141/> || 1974<ref name=Handelsstals/> || En 1971, décision de remplacer l'aciérie Kaldo par une aciérie LD et des coulées continues afin de retrouver la rentabilité<ref>{{ouvrage |langue= en |format électronique= pdf |
|||
|prénom1= F. E. |nom1= Brantley |
|||
|titre= Mineral yearbook |
|||
|année= 1971 |
|||
|passage= 617 ; 619 |
|||
|lire en ligne= http://images.library.wisc.edu/EcoNatRes/EFacs2/MineralsYearBk/MinYB1971v1/reference/econatres.minyb1971v1.fbrantley.pdf}}</ref>. L'investissement a été réalisé en 1974-1975<ref>{{lien web |langue= sv |format électronique= pdf |
|||
|titre= om kapitaltillskott till Norrbottens Jämverk AB |
|||
|prénom1= Nisl G. |nom1= Åsling |
|||
|année= 1976 |mois= décembre |jour= 22 |
|||
|passage= 4 |
|||
|url= http://www.riksdagen.se/sv/dokument-lagar/dokument/proposition/om-kapitaltillskott-till-norrbottens-jamverk-ab_G00357}}</ref> et a permis l'abandon de la filière Kaldo<ref name=Handelsstals/>. |
|||
|- |
|||
| 1 || Stanton Ironworks<br>(Grande-Bretagne) || [[Staveley Coal and Iron Company]] || 70 || 1965<ref name=Allen141/> || 1967<ref name=IndustrialAperture>{{lien web |langue= en |
|||
|url= http://www.industrialaperture.com/Pages/Galleries/Structures/ |
|||
|titre= Stanton Ironworks Demolition |
|||
|éditeur= Industrial Aperture}}</ref> || Four destiné à l'affinage de fonte phosphoreuse. Procédé abandonné au bout de 2 ans<ref name=IndustrialAperture/>. |
|||
|- |
|||
| 1 || La Providence de [[Marchienne-au-Pont|Marchienne]]<br>(Belgique) || [[Forges de la Providence]] || 35<ref>{{article |langue= en |
|||
|titre= The LD-Kaldo process |
|||
|prénom1= J. |nom1= Ledune |
|||
|prénom2= p. |nom2= Nilles |
|||
|périodique= Journal of Materials |
|||
|mois= avril |année= 1966 |
|||
|doi= 10.1007/BF03378430 |
|||
|passage= 485–490 |
|||
|lire en ligne= https://docplayer.net/98305912-The-ld-kaldo-process.html}}</ref> || 1965<ref name=Bhardwaj/> || 1980<ref>{{lien web |langue= de |
|||
|url= http://www.steel-photo.org/tag/marchienne/ |
|||
|titre= Forges de La Providence |
|||
|date= 07-05-2020 |
|||
|consulté le= 07-04-2023}}</ref> || Convertisseur LD-Kaldo, qui a été également utilisé comme outil de recherche. Seul le soufflage final déphosphorant est réalisé en mode Kaldo<ref name=CECA1973>{{ouvrage |format électronique= pdf |
|||
|titre= Affinage des fontes phosphoreuses en une phase avec décrassage en cours de soufflage |
|||
|éditeur= Communauté européenne du charbon et de l'acier |lien éditeur= Communauté européenne du charbon et de l'acier |
|||
|mois= mars |année= 1973 |
|||
|lire en ligne= http://aei.pitt.edu/44404/1/A7047.pdf}}</ref>. La combinaison des deux procédés permet de ménager les réfractaires tout en conservant les performances métallurgiques du Kaldo. Mais la disparition de la première phase de combustion du CO pénalise le recyclage des ferrailles<ref name=Bhardwaj/>. |
|||
|- |
|||
| 2 || [[Usine sidérurgique de Borlänge|Domnarvets Jernverk]]<br>(Suède) || [[Stora AB|Stora Kopparbergs Bergslags AB]] || 80<br>porté à 100<ref>{{article |
|||
|périodique= Revue de métallurgie |lien périodique= Revue de métallurgie |
|||
|titre= Cahiers d'informations techniques |
|||
|année= 1980 |
|||
|volume= 77 |
|||
|page= 284}}</ref> || 1965<ref name=Allen141/>{{,}}<ref name=yearbook1965/> || 1981<ref>{{lien web |langue= de |
|||
|titre= SSAB, Borlänge |
|||
|jour= 26 |mois= janvier |année= 2014 |
|||
|url= http://www.steel-photo.org/category/works/page/4/}}</ref> || Ces fours pouvaient réaliser une [[réduction directe]] du [[minerai de fer]] et une fusion. Le procédé, nommé ''Dored'', n'a jamais atteint le stade industriel<ref>{{ouvrage |langue= en |
|||
|prénom1= Amit |nom1= Chatterjee |
|||
|prénom2= Ramesh |nom2= Singh |
|||
|prénom3= Banshidhar |nom3= Pandey |
|||
|titre= Metallics for Steelmaking: Production and Use |
|||
|éditeur= Allied Publisher Ltd. |
|||
|année= 2001 |
|||
|passage= 409 |
|||
|isbn= 81-7764-130-1 |
|||
|lire en ligne= https://books.google.fr/books?id=NFqltO13iasC&pg=PA409#v=onepage&q&f=false}}</ref>. Le remplacement des Kaldos par des LD est évoqué dès le début des années 1970<ref name=Handelsstals/>. |
|||
|- |
|||
| 2 || [[Usine sidérurgique de Gandrange-Rombas|Aciérie de Gandrange]]<br>(France) || [[Usinor|Sacilor]] || 240 || 1969 || 1982<ref name=Thouvenin/> || Durée de vie du garnissage : 160 coulées. Plus grands convertisseurs Kaldo jamais mis en service<ref name=JeanRivet>{{lien web |format électronique= pdf |
|||
|prénom1= Jean |nom1= Rivet |
|||
|titre= La sidérurgie, des origines à nos jours |
|||
|jour= 25 |mois= octobre |année= 2006 |
|||
|url= https://docs.google.com/file/d/0BzYimQYWYSBeT0plZUZYOFZfZUk/edit}}</ref>. Arrêtés après la modernisation des 2 convertisseurs OLP construits en 1971 dans la même aciérie<ref name=Thouvenin/>. |
|||
|} |
|||
=== Métaux non ferreux === |
|||
{| class="wikitable center" style="width:100%;" |
|||
|+ Usines TBRC construites<ref name=Irandoc>Sauf mention contraire, la liste des TBRC et leurs caractéristiques sont issues de [http://idochp2.irandoc.ac.ir/FulltextManager/fulltext15/th/0/384.pdf]</ref> (liste non exhaustive{{note|Les convertisseurs expérimentaux ne sont pas détaillés. Dans cette catégorie, on peut signaler le Kaldo prototype d'INCO à Port Colborne de {{unité|7|tonnes}} qui a servi à généraliser le TBRC à la métallurgie extractive du cuivre<ref name=OxygenCopperCliff/>, celui du ''Warren Spring Laboratory'' à [[Stevenage]] de {{unité|200|kg}}, celui du [[Colorado School of Mines]] à [[Golden (Colorado)|Golden]] de {{unité|200|kg}}<ref name=Irandoc/>{{etc}} Les très petits convertisseurs sont également omis, comme celui de {{unité|0.25|m³}} de l'''Acton Pt Refinery'' à [[Londres]]<ref name=ExtractiveNickel/>.|group=note}}) |
|||
!scope="col" width="7%" | Nombre de fours |
|||
!scope="col" width="12%" | Emplacement |
|||
!scope="col" width="10%" | Propriétaire<br>à la mise en service |
|||
!scope="col" width="10%" | Capacité<br/>(t ou m³<ref group=note>En raison de la diversité des produits traités par un même convertisseur, et de leurs densités (de 4 pour une matte pauvre en cuivre, à 11,3 pour le plomb), il est parfois préférable de n'évoquer que le volume de métal traité.</ref>) |
|||
!scope="col" width="8%" | Date mise en service |
|||
!scope="col" width="8%" | Date d’arrêt |
|||
!scope="col" width="45%" | Remarques |
|||
|- |
|||
| 1 || [[Beerse]]<br>(Belgique) || [[Metallo-Chimique]] || {{unité|70|t de cuivre}} || années 1960<ref name=metallo-chimique group=note/> || || Recyclage de [[déchets d'équipements électriques et électroniques|déchets cuivreux]]. Production d'un cuivre noir pur à 98 %, ou d'un alliage cuivre-nickel à 10 % de nickel<ref name=Beerse2011>{{lien web |lang= vls |format électronique= pdf |
|||
|titre= Besluit van de deputatie van de provincie Antwerpen |
|||
|url= https://www.milieuinfo.be/dms/d/d/workspace/SpacesStore/35ec3873-1009-4753-bb41-5b50758f90bf/MLAV1%201000000420.pdf |
|||
|jour= 24 |mois= février |année= 2011 |
|||
|éditeur= Metallo-Chimique NV |lien éditeur= Metallo-Chimique}}</ref>. |
|||
|- |
|||
| 1 || [[Chouteau Township (Illinois)|Chouteau Township]]<br>(États-Unis) || [[Chemetco]] || {{unité|70|t de cuivre}} || 1970<ref name=<ref name=Verney/> || 2001<ref name=EPA>{{lien web |lang= en |
|||
|titre= Case Summary: Settlement reached at the Chemetco Superfund Site |
|||
|éditeur= Environmental Protection Agency |lien éditeur= Environmental Protection Agency |
|||
|url= https://www.epa.gov/enforcement/case-summary-settlement-reached-chemetco-superfund-site}}</ref> || Recyclage de déchets cuivreux, procédé développé par la Metallo-Chimique<ref name=TheTelegraph/>. Usine fermée pour pollution de l'eau<ref name=EPA/>. |
|||
|- |
|||
| 2 || [[Grand Sudbury|Copper Cliff]]<br>(Canada) || [[Inco]] || 20 m³<br/>{{unité|50|t de nickel}}<ref name=OxygenCopperCliff/> || 1971<ref name=OxygenCopperCliff/> || 2002<ref>{{ouvrage |langue= en |format électronique= pdf |
|||
|titre= Mathematical Programming of Peirce-Smith Converting |
|||
|prénom1= Alessandro |nom1= Navarra |
|||
|année= 1992 |mois= août |
|||
|passage= 187 |
|||
|éditeur= [[Polytechnique Montréal]] |
|||
|nature ouvrage= thèse |
|||
|lire en ligne= https://publications.polymtl.ca/1230/1/2013_AlessandroNavarra.pdf}}</ref> || Premiers convertisseurs industriels Kaldos dédiés à la métallurgie des non ferreux et nommés TBRC par [[Inco]]. Ils sont dédiés à l'affinage de matte de nickel<ref name=OxygenCopperCliff/>. |
|||
|- |
|||
| 2 || [[Tennant Creek]]<br>(Australie) || Peko Wallsend || 25 t || 1973<ref name=smh>{{lien web |lang= en |
|||
|titre= Tennant Creek |
|||
|jour= 8 |mois= février |année= 2004 |
|||
|url= http://www.smh.com.au/news/northern-territory/tennant-creek/2005/02/17/1108500201673.html}}</ref> || 1975<ref name=pyrometallurgy/> || Conversion de minerai cuivreux contenant du [[bismuth]]<ref name=smh/>. |
|||
|- |
|||
| 2 || [[Beerse]]<br>(Belgique) || Metallo-Chimique || 13 m³<br/>{{unité|70|t de cuivre}} || 1974<ref name=metallo/> || || Traitement du laitier riche en étain, en plomb, en cuivre et en nickel, issu du recyclage du cuivre dans le premier TBRC<ref name=Beerse2011/>{{,}}<ref name=EPAdecree>{{lien web |langue= en |format électronique= pdf |
|||
|titre= Lodged consent decree - Appendices A through O - Case 3:00-CV-00670-DRH-DGW |
|||
|url= https://semspub.epa.gov/work/05/909495.pdf |
|||
|éditeur= EPA |lien éditeur= Environmental Protection Agency |
|||
|jour= 18 |mois= juillet |année= 2013 |
|||
|passage= 205 ; 292-298}}</ref>. |
|||
|- |
|||
| 1 || [[Beerse]]<br>(Belgique) || Metallo-Chimique || {{unité|10|t de [[Alliage plomb-étain|plomb-étain]]}} || 1974<ref name=metallo/> || || Recyclage de déchets ou d'oxydes de plomb et d'étain<ref name=Beerse2011/>. |
|||
|- |
|||
| 1 || [[usine métallurgique de Rönnskär|Rönnskärsverken]]<br>(Suède) || [[Boliden AB]] || {{unité|13|m³}}<br/>{{unité|90|t de plomb}}<ref name=EMC91/> || 1976 || || Premier Kaldo au monde affinant de la matte de plomb. Initialement dédié au traitement des poussières issues de la production de cuivre, puis est devenu un outil polyvalent, recyclant déchets de cuivre et de plomb<ref name=Ronnskar/>. |
|||
|- |
|||
| 3 || [[Soroako]]<br>(Indonésie) || [[Inco]] || 20 m³ || 1977<ref name=Review>{{article |langue= en |format électronique= pdf |
|||
|titre= A Review of Nickel Pyrometallurgical Operation |
|||
|prénom1= C. M. |nom1= Diaz |
|||
|prénom2= C. A. |nom2= Landolt |
|||
|prénom3= Anthony E. M. |nom3= Warner |
|||
|prénom4= Ahmed |nom4= Vahed |
|||
|périodique= JOM (Journal of the Minerals, Metals & Materials Society) |
|||
|url= https://www.researchgate.net/profile/Ahmed_Vahed/publication/257285680_A_Review_of_Nickel_Pyrometallurgical_Operation/links/558435bb08aeb0cdaddbb178/A-Review-of-Nickel-Pyrometallurgical-Operation.pdf |
|||
|doi= 10.1007/BF03258548 |
|||
|mois= septembre |année= 1988}}</ref> || 1987-1988 || Conversion d'une matte à 32 % de nickel en [[ferronickel]]. 2 Kaldos remplacés par 2 [[Convertisseur Peirce-Smith|convertisseurs Peirce-Smith]], le 3{{e}} étant stoppé<ref name=Review/>. |
|||
|- |
|||
| 1 || [[Usine métallurgique de Rönnskär|Rönnskärsverken]]<br>(Suède) || [[Boliden AB]] || {{unité|13|m³}} || 1978 || 1989 || Production de matte de cuivre riche (60-65% Cu) à partir de minerai concentré. Arrêté pour manque de disponibilité de minerai<ref name=EMC91/>. Revendu et redémarré en Inde en 2002<ref name=FurnaceFabrica>{{lien web |langue= en |format électronique= pdf |
|||
|titre= Turnkey Process Plant Solutions |
|||
|url= http://furnacefabrica.com/wp-content/uploads/2016/08/FFIL-Corporate-Presentation.pdf |
|||
|mois= août |année= 2016 |
|||
|éditeur= Furnace Fabrica}}</ref>. |
|||
|- |
|||
| 1 || [[Mine d'Afton-Ajax]]<br>(Canada) || [[Teck Resources|Teck Mining]] || 20 m³<ref name=Irandoc/><br>{{unité|45|t}} de cuivre<ref name=MercuryAfton>{{article |langue= en |
|||
|titre= An Assessment of Mercury Emissions from the Afton Copper Smelter, British Columbia, Canada |
|||
|prénom1= J. D. |nom1= Robertson |
|||
|prénom2= C. J. |nom2= Price |
|||
|périodique= Journal of the Air Pollution Control Association |
|||
|jour= 8 |mois= mars |année= 2012 |
|||
|url= http://www.tandfonline.com/doi/pdf/10.1080/00022470.1986.10466115 |
|||
|doi= 10.1080/00022470.1986.10466115 |issn= 0002-2470}}</ref> || 1978<ref name=pyrometallurgy>{{article |langue= en |
|||
|titre= Pyrometallurgy |
|||
|prénom1= P. J. |nom1= Mackey |
|||
|prénom2= G. C. |nom2= Balfour |
|||
|périodique= JOM (Journal of the Minerals, Metals & Materials Society) |
|||
|url= http://link.springer.com/article/10.1007%2FBF03354363#page-1 |
|||
|doi= 10.1007/BF03354363 |issn= 1543-1851 |
|||
|mois= avril |année= 1978 |volume= 30 |passage= 36-43}}</ref> || 1983<ref name=MercuryAfton/> || Fusion directe de concentrés de cuivre en blister. |
|||
|- |
|||
| 1 || [[Philadelphie]]<br>(États-Unis) || Franklin Smelting & Refining Company || 15 t || || 1996<ref name=Jolly>{{ouvrage |langue= en |format électronique= pdf |
|||
|prénom1= Janice L. |nom1= Jolly |
|||
|titre= 2012 Technical Report |sous-titre= The U.S. Copper-base Scrap Industry and Its By-products |
|||
|mois= juin |année= 2012 |
|||
|éditeur= Copper Development Association Inc |
|||
|passage= 24 ; 85 |
|||
|lire en ligne= http://plone.environmentalhealthnews.org/news/2013/pdf-links/Copper%20scrap%20report.pdf}}</ref> |
|||
|| Conversion de cuivre noir en blister (initialement). Usine fermée à cause des contraintes environnementales<ref name=Jolly/>. |
|||
|- |
|||
| 1 || Philadelphie<br>(États-Unis) || Franklin Smelting & Refining Company || 25 t || || 1996<ref name=Jolly/> || Conversion de cuivre noir en blister (initialement). Usine fermée à cause des contraintes environnementales<ref name=Jolly/>. |
|||
|- |
|||
| 1 || [[Fonderie d'étain de Texas City|Tex-Tin]]<br>(États-Unis) || Gulf Chemical and Metallurgical Company || ? || 1978 || 1991<ref name=TexTinRecordDecision/> || Fusion de concentrés d'étain et réduction des scories d'étain<ref name=Cuyper/>. Abandonné en 1989 par pénurie de minerais concentrés importés compétitifs, et reconverti dans le traitement du cuivre. Arrêt définitif en 1991 à la suite de l'effondrement du convertisseur<ref name=TexTinRecordDecision/>. |
|||
|- |
|||
| 3<ref>{{ouvrage |langue= en |
|||
|prénom1= M. K. |nom1= Snyder |
|||
|prénom2= F. D. |nom2= Shobe |
|||
|titre= Source Category Survey: Secondary Copper Smelting and Refining Industry |
|||
|éditeur= EPA |lien éditeur= Environmental Protection Agency |
|||
|jour= 9 |mois= mai |année= 1980 |
|||
|passage= 45 |
|||
|lire en ligne= https://nepis.epa.gov/Exe/ZyPURL.cgi?Dockey=000021NM.txt}}</ref> || Chouteau Township<br>(États-Unis) || [[Chemetco]] || 13 m³<br/>{{unité|70|t de cuivre}}<ref name=chemetcoestate>{{lien web |lang= en |
|||
|titre= Top Blown Rotary Converter (TBRC) Détails |
|||
|jour= 27 |mois= juin |année= 2006 |
|||
|url= http://www.chemetcoestate.com/html/converter.html}}</ref> || 1981-1982<ref name=chemetcoestate/> || 2001 || Recyclage de déchets cuivreux riches à 50 %, ainsi que la récupération d'étain. Usine fermée pour pollution de l'eau<ref name=EPA/>. Convertisseurs identiques aux 2 Kaldo de {{unité|70|tonnes}} de la Metallo-Chimique<ref name=EPAdecree/>. |
|||
|- |
|||
| 1 || [[Zandjan|Zanjan]]<br>(Iran) || National Iranian Lead and Zinc || 13 m³<ref name=Ullmann>{{Chapitre |langue= en |
|||
|titre chapitre= Lead |
|||
|auteurs ouvrage= Alistair Davidson, Jessica Ryman, Charles A. Sutherland, Edward F. Milner, Robert C. Kerby, Herbert Teindl, Albert Melin, Hermann M. Bolt |
|||
|titre ouvrage= [[Ullmann's Encyclopedia of Industrial Chemistry]] |
|||
|éditeur= Wiley-VCH |lien éditeur= Wiley-VCH |
|||
|année= 2002 |
|||
|doi= DOI: 10.1002/14356007.a15_193.pub3}}</ref> || 1983<ref name=Ullmann/> || 2013<ref name=MetalNews>{{article |langue= en |
|||
|titre= Iran's Lead and Zinc Overview |
|||
|périodique= Metal News |
|||
|url= http://www.metalsnews.ir/index.php/en/base-metals/titles/lead-and-zinc/item/484-iran-lead-and-zinc-overview |
|||
|jour= 29 |mois= novembre |année= 2016}}</ref> || Coupellation de matte de plomb<ref name=Ullmann/>{{,}}<ref>{{ouvrage |lang= es |
|||
|titre= Manual de evaluación técnico-económica de proyectos mineros de inversión |
|||
|prénom= Ricardo |nom= Arteaga Rodriguez |et al.= oui |
|||
|éditeur= Instituto Tecnológico Geominero de España |
|||
|isbn= 8478403051 |isbn2= 9788478403059 |
|||
|mois= septembre |année= 1997 |numéro d'édition= 2 |
|||
|passage= 510 |
|||
|lire en ligne= https://books.google.fr/books?id=Eu9Qb5R655AC&pg=PA510&lpg=PA510#v=onepage&q&f=false}}</ref>. Usine fermée en mi-2013 pour des raisons environnementales<ref name=MetalNews/>. |
|||
|- |
|||
| 1 || [[Francfort-sur-le-Main]]<br>(Allemagne) || [[Evonik|Degussa]] || 6 t || || || [[Coupellation]] de matte de plomb. |
|||
|- |
|||
| 1 || [[usine métallurgique de Rönnskär|Rönnskärsverken]]<br>(Suède) || [[Boliden AB]] || 6 t || || || Coupellation de matte de plomb. |
|||
|- |
|||
| 1 || [[Columbus (Montana)|Columbus]]<br>(États-Unis) || {{lien|Stillwater Mining Company}} || 7 m³<ref>{{article |lang=en |format électronique= pdf |
|||
|titre= JOM World Nonferrous Smelter Survey, Part II: Platinum Group Metals |
|||
|prénom= Rodney |nom= Jones |
|||
|mois= décembre |année= 2004 |numéro= 56 |
|||
|périodique= The journal of the Minerals, Metals & Materials Society |
|||
|passage= 59-63 |
|||
|doi= 10.1007/s11837-004-0238-8 |
|||
|lire en ligne= https://www.pyrometallurgy.co.za/Mintek/Files/2004JonesPGMSmelterSurvey.pdf}}</ref>{{,}}{{note|Une source évoque une taille de TBRC de la Stillwater Co. de {{unité|0.15|m³}}, soit {{unité|1.5|t de matte}}<ref name=JOM1992>{{article |langue= en |
|||
|titre= Converting practices at the stillwater precious metals smelter |
|||
|prénom1= Greg K. |nom1= Roset |
|||
|prénom2= Jan W. |nom2= Matousek |
|||
|prénom3= Paul J. |nom3= Marcantonio |
|||
|périodique= Review of Extractive Metallurgy |
|||
|année= 1992 |mois= avril |volume= 44 |
|||
|passage= 39–42 |
|||
|éditeur= JOM |
|||
|lire en ligne= https://link.springer.com/article/10.1007/BF03222819}}</ref>.|group=note}}<br/>5 t de matte<ref>{{Chapitre |lang= en |
|||
|titre chapitre= Granulation as it pertains to electric furnace matte, converter slag, and converter matte in a PGM smelter |
|||
|prénom1= Greg |nom1= Roset |
|||
|prénom2= Dayle |nom2= Flynn |
|||
|prénom3= Jacob |nom3= Bummer |
|||
|titre ouvrage= International Smelting Technology Symposium: Incorporating the 6th Advances |
|||
|auteurs ouvrage= Jerome P. Downey, Thomas P. Battle, Jesse F. White |
|||
|éditeur= The Minerals, Metals & Materials Society |
|||
|isbn= 978-1-11829-116-0 |
|||
|mois= mars |année= 2012 |
|||
|passage= 23-30 |
|||
|lire en ligne= https://books.google.fr/books?id=J2jw2UMDSzIC&printsec=frontcover&hl=fr#v=onepage&q&f=false}}</ref> || 1990<ref name=JOM1992/> || || Fusion d'une matte riche en [[Groupe du platine|platinoïdes]] et oxydation pour obtenir un métal blanc contenant 75 % Cu+Ni et 2,5 % de métaux précieux<ref name=JOM1992/>. |
|||
|- |
|||
| 1 || [[Marghera]]<br>(Italie) || SIMAR SpA || || 1992<ref name=ricerca>http://ricerca.gelocal.it/nuovavenezia/archivio/nuovavenezia/2010/04/04/VMHPO_VMH01.html?refresh_ce</ref> || 2000 || Affinage de cuivre. Fermé par manque de déchets cuivreux disponibles<ref name=pratclif>http://pratclif.com/mines/kamoto/copperDirectory02-Jan.pdf</ref>, tentative de relance en 2010<ref name=ricerca/>. |
|||
|- |
|||
| 1 || [[District de Bharuch|Bharuch]]<br>(Inde) || SWIL || 13 m³<ref name=FurnaceFabrica/><br/>{{unité|60|t de cuivre}}<ref>http://www.tcs.com/sitecollectiondocuments/case%20studies/tcs_innovation_case_jhagadia-copper.pdf</ref> || 2002<ref name=pratclif/>{{,}}<ref name=FurnaceFabrica/> || || Produit en 12 heures une matte d'environ 70% de cuivre à partir de déchets cuivreux.</br>Il s'agit du convertisseur de Bolinden arrêté en 1989 et relocalisé en Inde<ref name=FurnaceFabrica/>. Arrêté de 2009<ref>{{lien web |langue= en |
|||
|titre= Gujarat Copper Project (GCP) at Bharuch, Gujarat |
|||
|url= http://hindustancopper.com/oldapp/GCPPlant.asp |
|||
|éditeur= Hindustan Copper}}</ref> à 2017<ref>{{lien web |langue= en |
|||
|url= http://www.hindustancopper.com/Content/Admin/NewsFiles/8cbe9473-62f7-415e-bd3c-6b26728fd5d8.pdf |
|||
|titre= Kaldo Furnace inauguration |
|||
|jour= 6 |mois= août |année= 2017 |
|||
|éditeur= Hindustan Copper}}</ref>. |
|||
|- |
|||
| 1 || Xiangguang Yanggu Smelter || || || || || Récupération de métaux précieux dans la matte de cuivre<ref>http://www.xiangguang.com/esalegy.asp</ref> |
|||
|- |
|||
| 1 || || [[Jiangxi Copper]] || || 2009 || || Recyclage de cuivre Cu>70%. Associé à un four à réverbère<ref name=ENFI>{{lien web |langue= en |
|||
|titre= The technological developments of scrap copper smelters in China |
|||
|prénom1= Tang |nom1= Xulong |
|||
|url= https://docplayer.net/53304484-The-technological-developments-of-scrap-copper-smelters-in-china.html |
|||
|éditeur= ENFI}}</ref>. |
|||
|- |
|||
| 1 || Western Mining Co., à [[Xining]]<br>(Chine) || Qinghai Xiyu Nonferrous || 13 m³<ref name=Boliden2003/> || 2010<ref name=Ullmann/> || || Coupellation de matte de plomb<ref name=Ullmann/>. Remplace des [[haut fourneau|hauts fourneaux]] fermés à cause des contraintes environnementales. Technologie de Boliden<ref name=Boliden2003>{{lien web |langue= en |
|||
|titre= Boliden awarded a SEK 40 million Contract in China |
|||
|url= http://ir.boliden.com/en/pressreleases/boliden-awarded-a-sek-40-million-contract-in-china-25724 |
|||
|jour= 6 |mois= 3 |année= 2003 |
|||
|éditeur= Boliden |lien éditeur= Boliden AB}}</ref>. |
|||
|- |
|||
| 2 || Jinchuan smelter<br>(Chine) || [[Jinchuan Group]] || 13 m³<ref name=ENFI/> || 2011 || || Recyclage de cuivre Cu>80%. Associé à un four à sole oscillante<ref name=ENFI/>. |
|||
|- |
|||
| 1 || [[Lünen]]<br>(Allemagne) || [[Aurubis]] || {{unité|100|t}} de cuivre<ref>https://docplayer.org/55975548-Sms-siemag-fuehrend-in-sekundaermetallurgie.html</ref> || 2011 || || Addition de déchets dans du cuivre noir (80% Cu) pour en faire du cuivre à 95 %. L'étain et le plomb y sont retirés avec le laitier<ref>https://www.aurubis.com/binaries/content/assets/aurubis-en/dateien/responsibility/updatedenvironmstatem-hh_luenen_2013.pdf</ref> |
|||
|- |
|||
| 1 || [[usine métallurgique de Rönnskär|Rönnskärsverken]]<br>(Suède) || [[Boliden AB]] || || 2012|| || Recyclage de déchets électroniques cuivreux<ref>{{lien web |langue= en |format électronique= pdf |
|||
|titre= 2012 annual report |
|||
|éditeur= Boliden AB |lien éditeur= Boliden AB |
|||
|url= http://ir.boliden.com/afw/files/press/boliden/201303076769-1.pdf |
|||
|page= 48}}</ref>. |
|||
|- |
|||
| 1 || [[Wuzhou]] Recycling Industrial Park<br>(Chine)<ref>{{Ouvrage |langue=en |format électronique=pdf |
|||
|prénom1= Pui-Kwan |nom1= Tse |
|||
|titre= 2012 Minerals Yearbook |
|||
|éditeur= USGS |lien éditeur= Institut d'études géologiques des États-Unis |
|||
|année= 2015 |mois= février |
|||
|passage= 8.7 |
|||
|lire en ligne= https://d9-wret.s3.us-west-2.amazonaws.com/assets/palladium/production/mineral-pubs/country/2012/myb3-2012-ch.pdf}}</ref> || {{lien|Guangxi Non-ferrous Metals}} || || 2012 || || Recyclage de cuivre 20%<Cu<90%. Associé à un four à réverbère<ref name=ENFI/>. Repris en 2018 après la faillite de Guangxi Non-ferrous Metals, pour recycler des déchets >10% Cu<ref>{{lien web |lang= en |
|||
|titre= Present situation and Prospect of Guangxi Copper Industry chain in 2020 |
|||
|url= https://news.metal.com/newscontent/101169201/[smm-investigation]-present-situation-and-prospect-of-guangxi-copper-industry-chain-in-2020/ |
|||
|date= 20-06-2020 |
|||
|éditeur= SMM |
|||
|consulté le= 05-06-2022}}</ref>. |
|||
|- |
|||
| 1 || Zijin Copper<br>(Chine) || [[Jinchuan Group]] || || 2013<ref>https://docplayer.net/amp/36105792-Greetings-from-outotec-smelting.html</ref> || || Affinage de matte de cuivre issue d'un four de [[fusion flash]]<ref name=ENFI/>. |
|||
|- |
|||
| 4 || [[Comté de Richmond (Géorgie)|Richmond]]<br>(États-Unis) || [[Aurubis]] || 12 m³<ref>{{lien web |lang= en |
|||
|titre= Aurubis Richmond LLC SIP Permit Application |
|||
|url= https://www.aurubis.com/en/richmond/aurubis-doubles-u-s--investment-in-multimetal-recycling-facility |
|||
|date= 11-04-2022 |
|||
|éditeur= [[Aurubis]] |
|||
|consulté le= 08-05-2023}}</ref> || 2024-2026 (prév.)<ref name=AurubisDoubles>{{lien web |lang= en |
|||
|titre= Aurubis doubles U.S. investment in multimetal recycling facility |
|||
|url= https://www.aurubis.com/en/richmond/aurubis-doubles-u-s--investment-in-multimetal-recycling-facility |
|||
|date= 20-12-2022 |
|||
|éditeur= [[Aurubis]] |
|||
|consulté le= 08-05-2023}}</ref> || || Recyclage de déchets électroniques cuivreux<ref name=AurubisDoubles/>. |
|||
|} |
|||
== Évolutions et disparition == |
|||
=== Sidérurgie === |
|||
Au moment de son apparition, le procédé Kaldo combine beaucoup d'avantages : il traite les fontes phosphoreuses, permet de recyclage d'une grande quantité de ferrailles et permet un contrôle facile de l'affinage. Mais sa complexité le pénalise : c'est {{citation|un procédé élégant sur le papier mais d'une exploitation difficile}}<ref name="Soleild'acier"/>. |
|||
{{multiple image |
|||
|direction= vertical |
|||
|width= 250 |
|||
|image1= Rotor Converter.svg |
|||
|alt1= Schéma du Rotor |
|||
|caption1= Principe du convertisseur Rotor, un convertisseur rotatif contemporain du Kaldo. |
|||
|image2= Kaldo converter LD-Kaldo mixed design cropped.png |
|||
|alt2= Photo d'un alignement de convertisseurs |
|||
|caption2= Kaldo-LD de {{unité|35|tonnes}} à [[Marchienne-au-Pont]]. On distingue la hotte LD au-dessus de la cornue. |
|||
|footer= }} |
|||
Partant de ce constat, des convertisseurs rotatifs contemporains du Kaldo ont été évalués comme alternative : |
|||
* le procédé Rotor, industrialisé au début des années 1950 à l'usine d'[[Oberhausen (Rhénanie-du-Nord-Westphalie)|Oberhausen]] est également un convertisseur à l'oxygène rotatif<ref>|langue= de |format= pdf |
|||
|Périodique= Echo der Arbeit |
|||
|date= 26-11-1956 |numéro= 21 |
|||
|titre= Neue Wege zum Stahl |
|||
|passage= 244-245 |
|||
|lire en ligne= https://www.archive.nrw.de/sites/default/files/media/files/Echo%20der%20Arbeit%2021.1956.pdf}}</ref>. Il s'agit d'un procédé plus simple et plus conventionnel : le four tubulaire s'incline peu et n'effectue qu'une rotation toutes les {{unité|2|minutes}}. La rotation est plus destinée à homogénéiser l'usure des réfractaires qu'à accélérer les réactions chimiques. Celles-ci sont gérées par deux lances à oxygène : une pour la décarburation, l'autre pour la post-combustion des fumées au sein du four<ref name=NewSientist244/>{{,}}<ref name=MetalsReference>{{ouvrage |langue= en |
|||
|prénom1= Colin J. |nom1= Smithells |
|||
|titre= Metals Reference Book |
|||
|éditeur= Butterworths |
|||
|année= 1976 |édition= 5 |
|||
|isbn= 0408706279 |
|||
|passage= 1432 ; 1434 |
|||
|pages totales= 1582 |
|||
|lire en ligne= https://books.google.fr/books?id=hUIvBQAAQBAJ&printsec=frontcover&hl=fr#v=onepage&q&f=false}}</ref> ; |
|||
* le Kaldo-LD installé en 1965 dans l'aciérie de [[Marchienne-au-Pont]] est un Kaldo doté d'une lance et d'un dépoussiérage vertical de type LD. La combinaison des deux procédés permet d'améliorer la durée de vie des réfractaires tout en conservant la flexibilité et les performances métallurgiques du Kaldo. Le soufflage commence en mode LD, c'est-à-dire verticalement, puis la déphosphoration en mode Kaldo. Cependant, outre la complexité accrue, ce séquencement supprime la première phase de combustion du CO propre au Kaldo, et donc la possibilité de refondre de grandes quantités de ferrailles<ref name=Bhardwaj/>. Et la suppression du trou de coulée latéral LD dégrade la qualité de la vidange de la cornue, qui est un point fort du LD<ref name=CECA1973/>. |
|||
Les limitations de ces procédés alternatifs les rendent moins attractifs que le Kaldo. Mais les inconvénients du Kaldo sont évidents. Outre la tenue des réfractaires, la chaleur dégagée par la combustion du CO sollicite également la carcasse métallique, notamment la piste de roulement circulaire<ref name=yearbook1965>{{ouvrage |langue= en |format électronique= pdf |
|||
|prénom1= Robert A. |nom1= Whitman |
|||
|titre= Mineral yearbook |
|||
|année= 1965 |
|||
|passage= 524 ; 525 ; 528 |
|||
|lire en ligne= http://images.library.wisc.edu/EcoNatRes/EFacs2/MineralsYearBk/MinYB1965v1/reference/econatres.minyb1965v1.rwhitman.pdf}}</ref>. À la fin des années 1950, les convertisseurs à l'oxygène soufflent des charges de {{unité|50|à=75|tonnes}}. Dans les années 1960, la plupart des nouveaux convertisseurs ont une capacité de {{unité/2|220|à=300|tonnes}}. Mais la taille des convertisseurs Kaldo plafonne alors à {{unité|100|tonnes}} : elle évolue donc beaucoup moins vite que celle des convertisseurs LD<ref name=yearbook1964>{{ouvrage |langue= en |format électronique= pdf |
|||
|prénom1= Robert A. |nom1= Whitman |
|||
|titre= Mineral yearbook |
|||
|année= 1964 |
|||
|passage= 619 |
|||
|lire en ligne= http://images.library.wisc.edu/EcoNatRes/EFacs2/MineralsYearBk/MinYB1964v1/reference/econatres.minyb1964v1.rwhitman.pdf}}</ref> et la tentative de rattrapage par l'aciérie de Gandrange sera un échec technique<ref name=Freyssenet1979/>. |
|||
En fait, le Kaldo est condamné par l'évolution du métier. En effet, c'est un convertisseur où le métallurgiste s'efforce de réaliser à la fois la conversion de la fonte en fer, la mise à nuance et la chauffe exacte avant la coulée. Or, à partir des années 1950, les exigences croissantes dues à l'évolution de la métallurgie comme à la généralisation de la [[coulée continue]] condamnent progressivement cette approche : seuls des outils spécialisés peuvent atteindre les exigences requises. Ainsi se développe la métallurgie en poche : le convertisseur fournit un acier de composition et de température approximatives, que des outils en aval traitent de manière plus fine. La spécialisation de chaque outil permet d'améliorer la productivité et compense le coût entraîné par la complexification des aciéries. Dans cette évolution, la productivité du procédé LD l'emporte sur la polyvalence du Kaldo<ref>{{chapitre |langue=fr |
|||
|prénom1= Bernard |nom1= Trentini |
|||
|titre chapitre= Aciéries - Évolution des procédés |
|||
|titre ouvrage= Techniques de l'ingénieur. Élaboration et recyclage des métaux |
|||
|éditeur= [[Éditions techniques de l'ingénieur]] |
|||
|jour= 10 |mois= octobre |année= 1991}}</ref>. Et si le rendement thermique du Kaldo est séduisant, en sidérurgie, le [[gaz de convertisseur]] généré par les procédés alternatifs, comme le LD, est riche en CO et peut être avantageusement brûlé dans les fours de l'usine. Or après le [[premier choc pétrolier]], ce type de gaz est devenu incontournable dans le bilan énergétique d'un complexe sidérurgique<ref name="Soleild'acier"/>. |
|||
=== Métaux non ferreux === |
|||
Dans les non ferreux, le TBRC a failli disparaitre avant de rencontrer, après les années 2010<ref>{{ouvrage |langue= en |
|||
|prénom1= Marc E. |nom1= Schlesinger |
|||
|prénom2= Matthew J. |nom2= King |
|||
|prénom3= Kathryn C. |nom3= Sole |
|||
|prénom4= William G. I. |nom4= Davenport |
|||
|titre= Extractive Metallurgy of Copper |
|||
|éditeur= Elsevier |lien éditeur= Elsevier (éditeur) |
|||
|numéro d'édition= 5 |année= 2011 |
|||
|isbn= 978-0-08-096789-9 |
|||
|passage= 393 |
|||
|lire en ligne= https://books.google.fr/books?id=bcwiQepD2yYC&printsec=frontcover&hl=fr&source=gbs_ge_summary_r&cad=0#v=onepage&q&f=false}}</ref>, un regain d'intérêt dans la fusion des déchets, notamment cuivreux, où sa flexibilité lui permet de s'adapter à des charges très variables<ref name=EMC91/>. Sa compacité et son aptitude à traiter des minerais contenant beaucoup d'impuretés le rendent également intéressant dans les fonderies de petites tailles ou pour des augmentations incrémentales de production dans des usines existantes<ref>{{article |lang= en |format= pdf |
|||
|prénom1= Heinrich R. |nom1= Traulsen |
|||
|prénom2= John C. |nom2= Taylor |
|||
|prénom3= David B. |nom3= George |
|||
|titre= Copper Smelting - An Overview |
|||
|périodique= JOM (Journal of the Minerals, Metals & Materials Society) |
|||
|mois= août |année= 1982 |numéro= 34 |passage= 35–40 |
|||
|doi= 10.1007/BF03338071 |
|||
|lire en ligne= https://pdfslide.net/documents/copper-smelting-an-overview.html?page=1}}</ref>. Des TBRC sont ainsi régulièrement installés : par exemple, au début du {{s-|XXI}}, l'entreprise [[SMS Group]] revendique avoir installé plus de 40 convertisseurs<ref>{{lien web |lang= en |
|||
|url= https://www.sms-group.com/plants/converters-for-non-ferrous-metals |
|||
|titre= Top blown rotary converter – TBRC and Kaldo |
|||
|éditeur= [[SMS Group]] |
|||
|consulté le= 04-05-2023}}</ref>, et son concurrent [[Outotec]] en compte 17<ref>{{lien web |lang= en |format= pdf |
|||
|url= http://www.slag-valorisation-symposium.eu/2013/images/papers/s2_1_pres_Reuter.pdf |
|||
|auteur= Markus A. Reuter |
|||
|titre= Review of Metal Recycling |
|||
|éditeur= [[Outotec]] |
|||
|année= 2013 |
|||
|consulté le= 04-05-2023}}</ref>. |
|||
Au-delà du cuivre, l'aptitude du TBRC à traiter la plupart des métaux les non ferreux est reconnue mais il s'est révélé inadapté à la production de masse<ref>{{ouvrage |langue=en |
|||
|prénom1= Vincent |nom1= Rich |
|||
|titre= The International Lead Trade |
|||
|éditeur= Woodhead Publishing |
|||
|année= 1994 |
|||
|isbn= 1855731037 |
|||
|lire en ligne= https://books.google.fr/books?id=pWQsKEsDTBoC&pg=PA50#v=onepage&q&f=false |
|||
|passage= 50}}</ref>. Mais les petits TBRC, d'une capacité de {{unité|0,5|à=10|tonnes}}, sont des outils sans équivalents dans la récupération de métaux précieux<ref name=Proceedings/>. Leur petite taille et une conception simplifiée font disparaitre les soucis mécaniques qui ont handicapé les engins sidérurgiques. La possibilité de réaliser beaucoup d'opérations successives dans le même réacteur limite les pertes et la pollution. La compacité et l'efficacité thermique du four ont amené le TBRC à remplacer les derniers fours à réverbères<ref name=Proceedings/>. |
|||
== Notes et références == |
== Notes et références == |
Version du 5 juin 2023 à 22:04
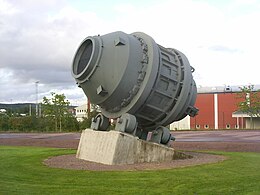
Le procédé Kaldo est un ancien procédé d'affinage utilisé en sidérurgie pour traiter la fonte brute phosphoreuse. Il s'agit d'un modèle particulier de convertisseur à l'oxygène pur, dans lequel le brassage du métal en fusion est assuré par la rotation de la cornue, à l'instar d'une bétonnière. Le nom « Kaldo » est un mot-valise, construit à partir du nom de son inventeur, le professeur Bo Kalling, et de l'usine qui, en 1948, a développé et industrialisé le procédé, la Domnarvets Jernverk.
Le convertisseur a été adapté à la métallurgie des métaux non ferreux, où il est souvent appelé TBRC (pour Top Blown Rotary Converter). Il y est un outil très polyvalent, autant pour la fusion de déchets riches en cuivre ou en métaux précieux, que pour l'affinage des mattes de cuivre, de nickel, d'étain ou de plomb.
En dépit de ses coûts en réfractaires élevés, le procédé Kaldo a été très populaire dans les années 1960 car il a été premier convertisseur à l'oxygène à la fois capable d'affiner efficacement les fontes phosphoreuses, d'élaborer précisément une gamme étendue d'alliages et de recycler une grande quantité de ferrailles. Mais, dépassé quelques années après par les progrès du procédé LD, plus simple et plus compétitif, il disparait en 1982, avec l'arrêt des deux kaldos géants de l'aciérie de Gandrange.
Dans l'élaboration des métaux non ferreux, le TBRC a aussi failli disparaitre, avant de redevenir, au début du XXIe siècle, un outil apprécié pour recycler les déchets d'équipements électriques et électroniques. Sa flexibilité correspond bien à la complexité des charges à traiter, ainsi qu'à des rythmes de production variables. Il est également l'outil le plus efficace pour l'extraction pyrométallurgique de métaux précieux présents dans des sous-produits d'usine métallurgiques.
Histoire
Contexte : mise au point du convertisseur à l'oxygène

Envisagée dès 1856 par Bessemer lui-même[1], l'utilisation d'oxygène pur au lieu d'air serait une amélioration logique des convertisseurs Bessemer et Thomas. En effet :
- 78 % de l'air est composé d'azote qui n'a aucun rôle utile dans l'affinage de la fonte. Injecter inutilement de l'azote représente une perte thermique, à peine compensée par le bilan exothermique des réactions chimiques : « chaque m3 d'azote sortant du convertisseur emporte sensiblement la chaleur nécessaire à la fusion d'un peu plus d'un kilogramme de ferraille[2] » ;
- la basse teneur de l'air en oxygène limite la vitesse des réactions chimiques ; le soufflage dure plus longtemps parce qu'on ne peut pas augmenter le débit d'air sans risquer un débordement ;
- l'azote se dissout dans l'acier liquide et une fraction y reste quand l'acier se solidifie. Or l'azote est un élément fragilisant pour l'acier alors qu'une bonne ductilité est essentielle à de nombreuses applications, notamment la construction automobile qui recherche des aciers faciles à emboutir[3], avec des teneurs en azote inférieures à 50 ppm, inaccessibles avec le procédé Thomas[4].
En 1895, l'ingénieur allemand Carl von Linde réussit la liquéfaction de l'air. Indépendamment, le physicien et chimiste français Georges Claude met en service le un procédé industriel de liquéfaction de l'air. Leurs brevets permettent la production industrielle, et surtout économique, de grandes quantités d'oxygène liquide : l'affinage à l'oxygène imaginé par Bessemer devient réalisable[5]. Mais le remplacement simple de l'air par de l'oxygène pur présente des difficultés considérables. Notamment, la réaction de l'oxygène pur avec la fonte mène à des températures de 2 500 à 2 700 °C : dans ces conditions, sans refroidissement des tuyères, le fond d'un convertisseur est détruit en quelques heures[6].

En 1949, le métallurgiste suisse Robert Durrer et l'ingénieur autrichien Theodor Eduard Suess trouvent une solution satisfaisante : ils mettent au point, à l'aciérie Vöest à Linz (Autriche), le soufflage d'oxygène au moyen d'une lance pénétrant verticalement dans la cornue. L'invention apparaît vite comme une technologie de rupture : six mois après le premier essai, le prototype s'avère plus économique que les meilleurs convertisseurs classiques ! En effet, ils combinent l'avantage des convertisseurs Martin — l'absence d'azote dans l'acier — avec la productivité des convertisseurs Bessemer et Thomas — une conversion rapide et sans apport de combustible —. Plus efficaces et donc moins nombreux que leurs équivalents à l'air, les nouveaux convertisseurs LD ne demandent qu'un investissement environ deux tiers, et des coûts d'exploitation limités à 55 % de ceux d'une usine traditionnelle de capacité comparable[7].
Dans le convertisseur LD, le brassage est assuré par la remontée de bulles de monoxyde de carbone (CO) produites par la décarburation de la fonte. Mais ce mouvement, efficace en début de soufflage, tend à ralentir lorsque le carbone dissous passe en dessous de 0,1 %, et le brassage avec le laitier diminue corrélativement. Or, l'oxydation du phosphore ne se produit qu'après le départ de tout le carbone, et la capture de l'oxyde P2O5 nécessite un brassage énergique avec la chaux du laitier. L'histoire se répète : comme jadis le convertisseur de Bessemer, le procédé LD révolutionne la sidérurgie mais se révèle inadapté à l'affinage des fontes phosphoreuses[5].
Enfin, les convertisseurs à l'oxygène pur génèrent d'énormes quantités de fumées rousses, chargées en oxyde de fer. Le dépoussiérage de ces fumées est incontournable. Même si ces fumées contiennent du gaz de convertisseur (monoxyde de carbone, CO) combustible (0,7 GJ/tonne d'acier[5]), avant le premier choc pétrolier de 1973, le coût d'investissement du système de dépoussiérage pénalise le procédé LD[3].
Développement du convertisseur rotatif
Depuis les années 1940, en Suède, la Domnarvets Jernverk, mène d'actives recherches pour mettre au point un procédé à l'oxygène pur capable de traiter les fontes phosphoreuses. En effet, la fonte brute traitée par l'aciérie de Domnarvet contenant de 1,8 à 2 % de phosphore, l'efficacité de la déphosphoration est un point incontournable[8]. Jusqu'ici, dans un pays où le minerai de fer est bien plus abondant que les ferrailles, le moyen le plus pertinent pour traiter ce type de fonte est le convertisseur Thomas. Mais l'injection d'oxygène dans le convertisseur amène une destruction rapide des réfractaires. Bien qu'en 1940, à Oberhausen (Allemagne), l'ingénieur américain d'origine estonienne Otto Lellep parvient à décarburer de la fonte avec de l'oxygène pur, il ne parvient pas à la déphosphorer : avec l'oxygène pur, l'oxydation du phosphore est trop exothermique pour les tuyères du convertisseur[6].
Pour dépasser 40 % d'oxygène, il faut des diluants plus efficaces que l'azote, et surtout moins nocifs vis-à-vis des propriétés de l'acier car l'azote fragilise l'acier. L'aciérie de Domnarvet adopte alors le dioxyde de carbone (CO2) dont le craquage à haute température, endothermique, permet de refroidir sensiblement le réfractaire. En 1947-1949, en fin de soufflage, les convertisseurs Thomas de Domnarvet soufflent ainsi un mélange gazeux contenant jusqu'à 58 % d'oxygène[9].

Mais mélanger l'oxygène avec un refroidissant ne peut être une solution satisfaisante. Pour injecter de l'oxygène pur, il faut momentanément[note 1] renoncer au soufflage par le fond, et assurer le brassage du métal par un autre moyen. Dans ce contexte, la rotation du convertisseur s'impose comme une des rares configurations techniquement réaliste et compatible avec une injection d'oxygène par une lance[6].
Les essais d'un convertisseur rotatif commencent à Domnarvet en 1948[10] avec un prototype d'une capacité interne de 3 tonnes, puis un pilote de 15 tonnes. Le premier démonstrateur industriel, de 30 tonnes, est construit en 1954 et est opérationnel en 1956[11].
Ce convertisseur est appelé « Kaldo », un mot-valise, construit à partir du nom de son inventeur, le professeur Bo Kalling, et de l'usine qui a développé et industrialisé le procédé, la Domnarvets Jernverk. Il se révèle être un succès technique. La possibilité de jouer sur la vitesse de rotation et l'inclinaison de la lance apporte une flexibilité unique. Notamment, grâce à la rotation, la décarburation n'a plus à assurer le brassage du bain et l'injection d'oxygène peut être moins violente. L'oxygène, qui se répand alors dans la cornue, brûle le monoxyde de carbone en dioxyde de carbone, apportant une chaleur supplémentaire qui peut être utilisée pour refondre des ferrailles. Le gaz ainsi brûlé n'ayant plus de potentiel comme combustible, son traitement se limite à un dépoussiérage sans récupération. Cette simplification compense, en partie, la complexité mécanique due à la rotation[11].
Adoption du procédé
Les sidérurgistes lorrains, dont le minerai local, la minette, est riche en phosphore, s'intéressent de près au procédé. Convaincus par la nécessité de passer au convertisseur à l'oxygène, ils sont, en 1960, à l'origine du deuxième convertisseur Kaldo. Celui-ci, installé à l'usine sidérurgique de Florange, représente un saut capacitaire notable par rapport à son aîné : il peut affiner 110 tonnes de fonte phosphoreuse[5]. Il s'agit aussi du plus gros convertisseur à l'oxygène pur présent en Lorraine. Sa capacité est par la suite progressivement augmentée jusqu'à 140 tonnes[12].

Dans les années suivantes, le procédé est systématiquement évalué comme une alternative au procédé LD et à ses dérivés. Dès 1965, 10 usines utilisent le procédé Kaldo, en France, Suède, États-Unis, Japon et surtout au Royaume-Uni. Les capacités des nouveaux convertisseurs se situent entre 50 et 140 tonnes[13]. Mais l'avenir du procédé semble déjà compromis : dès 1967, le métallurgiste James Albert Allen estime que « Avec une plus grande consommation de capitaux, des problèmes techniques et une consommation en réfractaire plus élevée, il apparaît plutôt douteux qu'il puisse rivaliser efficacement avec les procédés LD, LD-AC ou leurs évolutions.[14] »
Procédé Martin-Siemens (référence) | Procédé Kaldo | Procédé LD | |
---|---|---|---|
Coût d'investissement (convertisseurs seuls) |
100 | 58 | 50 |
Coût de fonctionnement | 100 | 72,5 | 56,4 |
En effet, au début des années 1960, des variantes du procédé LD capables de traiter les fontes phosphoreuses sont mises au point : le procédé LD-AC, qui consiste à injecter de la chaux en poudre en la mélangeant avec l'oxygène démontre la flexibilité du soufflage par le haut[3]. D'autres variantes sont ensuite développées sur ce principe (LBE, LD-Pompey, OLP, etc.).Cependant, le procédé LD perd beaucoup de son intérêt dès qu'on l'emploie à l'affinage des fontes phosphoreuses[5]. Surtout, tous ces procédés mettent en œuvre des réactions chimiques très rapides. Dans les années qui suivent leur apparition, les convertisseurs LD et leurs dérivés sont exclus de l'élaboration d'aciers de qualité[16]. L'apparition de la coulée continue, qui exige un excellent contrôle de la température de l'acier en fusion, nécessite aussi un bon contrôle de l'affinage[17].
C'est ainsi que, en 1969, « D'autres derviches métallurgiques devaient succéder […], notamment les deux Kaldo de 240 tonnes de Sacilor à Gandrange.[5] » Ces énormes engins de 1 500 tonnes[18] qui tournent à 30 tour/min sont deux fois plus gros que n'importe quel autre convertisseur Kaldo ! Mais deux ans plus tard, deux convertisseurs OLP de 240 tonnes sont mis en service dans la même aciérie alors que le troisième Kaldo prévu est annulé. La course à la taille, censée favoriser les économies d'échelle, a tué le procédé au lieu de le sauver : la limite technologique est atteinte, les coûts augmentent avec les dimensions alors que c'est l'inverse qui était escompté[19].
Adaptation aux métaux non ferreux
En 1958, soit deux ans après la mise en service industrielle du premier Kaldo sidérurgique de 30 tonnes à Domnarvet, l'entreprise canadienne Inco commence à évaluer la déclinaison de ce procédé à la métallurgie extractive du nickel. Elle envoie quelques ingénieurs en Suède pour explorer la conversion à l'oxygène pur de la matte de nickel avec le prototype originel de 3 tonnes. Tous leurs essais ayant réussi, Inco construit un convertisseur expérimental de 7 tonnes dans son centre de recherche de Port Colborne[20]. En Europe, une démarche similaire est entreprise par un producteur belge de cuivre, la Metallo-Chimique, qui construit un four Kaldo dans les années 1960[21]. Le procédé est un succès et elle brevète en 1970 le recyclage de cuivre par ce moyen[22] lorsqu'elle participe à la création de Chemetco[23], une entreprise américaine qui met en service cette année-là un Kaldo de 70 tonnes de capacité construit par Krupp[24].
Si la Métallo-Chimique semble la première entreprise à utiliser un kaldo industriel de 70 tonnes[note 2] pour l'affinage des métaux non ferreux, c'est Inco qui, par la mise en service en 1971 de deux convertisseurs de 50 tonnes à Copper Cliff (Grand Sudbury), lance véritablement l'utilisation du Kaldo dans la production des non ferreux. Cette adaptation est renommée TBRC (pour Top Blown Rotary Converter). Elle structure la stratégie d'Inco et s'avère un succès : en 1979, ces deux convertisseurs ont déjà élaboré un million de tonnes de nickel[20],[note 3], et produisent encore, 45 ans après leur mise en service[25].
Très semblables aux kaldos, les convertisseurs TBRC intègrent le fait que l'oxydation des mattes étant beaucoup moins exothermique que l'oxydation de la fonte[note 4], la lance à oxygène doit être remplacée par un brûleur oxygène-gaz naturel[28]. L'aptitude des convertisseurs TBRC à réaliser successivement la fusion et l'oxydation d'une charge métallique est immédiatement explorée par Inco dans son convertisseur expérimental de Port Colborne. Cet outil de recherche confirme les avantages de l'affinage à l'oxygène dans la métallurgie extractive du cuivre, et positionne le TBRC comme un outil capable de traiter n'importe quelle matte cuivreuse complexe[20]. Mais l'affinage avec le TBRC reste un procédé lent et coûteux : l'utiliser pour la production de cuivre obtenu à partir de minerai est un luxe. Le convertisseur rotatif ne se justifie que lorsqu'il s'agit de traiter des minerais très complexes, ou de recycler des déchets riches en métaux précieux[29],[30].
En 1976, l'entreprise suédoise Boliden AB met en service dans son usine de Rönnskär le premier TBRC produisant du plomb. L'extraction de ce métal nécessite une étape supplémentaire consistant en une réduction, qui se déroule après la fusion et l'oxydation de la charge[31]. Cette réduction est obtenue en brûlant un combustible riche en carbone (coke de pétrole, poussier de coke, etc.) dans le convertisseur, de manière à y créer une atmosphère réductrice riche en CO tout en apportant de la chaleur[28],[30]. Initialement dédié à l'extraction du plomb contenu dans les poussières issues de la production de cuivre, le TBRC de Boliden devient en 1980 un outil polyvalent, recyclant soit des déchets électroniques contenant du cuivre, soit des déchets riches en plomb[31].
En 1978, la fonderie d'étain de Texas City met en service un TBRC entièrement dédié à la fusion réductrice de minerais concentrés de cassitérite (SnO2). Tout comme pour le plomb, il s'agit de réaliser une oxycombustion qui apportera la chaleur et les gaz réducteurs nécessaires à la désoxydation du dioxyde d'étain. À la fin de la fusion réductrice, l'étain métallique est coulé. Mais les scories restant dans le convertisseur contiennent encore une quantité non négligeable d'étain combiné avec du fer[32]. La méthode d'extraction de cet étain scorifié, mise au point en 1974 par la Metallo-Chimique[21], consiste en une addition de soufre (soufre pur ou pyrite) qui, en se combinant à l'étain, permet aux sulfures d'étain de s'échapper sous forme gazeuse[32].
Le procédé
Le convertisseur
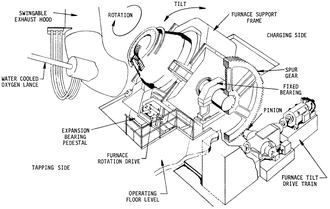
Le convertisseur est conçu comme une bétonnière. En fonctionnement, il est légèrement incliné par rapport à l'horizontale et tourne à environ 30 tr/min. L'oxygène est injecté par une lance, et les additions destinées à amender le laitier par une autre. La rotation assure un bon mélange, et accélère les réactions chimiques ; mais elle augmente considérablement les coûts de construction comme d'entretien[3]. Par contre, l'agitation de bain étant moins violente que dans le procédé LD, le laitier mousse peu et il est alors plus facile de suivre l'évolution de l'affinage[11].
L'autre originalité du procédé réside dans l'injection partielle de l'oxygène dans le bain pour l'affinage proprement dit. L'oxygène excédentaire est consommé par la combustion du CO en CO2 dans l'enceinte du four. La chaleur produite par la réaction est absorbée par les réfractaires, qui la restituent au métal lorsque le mouvement de rotation les met en contact. Ainsi, les réfractaires, outre leur sollicitation mécanique due à la rotation, subissent un cycle thermique extrêmement sévère puisque c'est le métal en fusion qui les refroidit[11],[33]!
La vitesse de rotation est variable selon les phases du soufflage. Elle dépasse rarement 30 tr/min. Le convertisseur peut également s'incliner dans toutes les positions. Pendant le soufflage, l'inclinaison se situe entre 16° et 20° par rapport à l'horizontale. De même, la lance à oxygène, refroidie à l'eau, est inclinée entre 20° et 37° par rapport à l'horizontale. Elle est souvent animée d'un mouvement oscillant[note 5]. Les fumées, chaudes, sont évacuées par une hotte refroidie qui vient se plaquer contre le bec du convertisseur. Cette hotte est conçue de manière à permettre le passage de la lance à oxygène ainsi que la jetée d'additions dans la cornue[11].
L'émulsion du laitier étant assez limitée, les Kaldos sont plus petits que les convertisseurs LD de capacité identique. On compte en général un volume interne de 0,5 m³/tacier, contre 0,75 m³/tacier pour les convertisseurs LD, sachant que les fontes riches en phosphore nécessitent un laitier abondant, qui occupe l'espace au détriment du métal[11].
Le revêtement réfractaire peut être celui mis au point par Sidney Gilchrist Thomas, c'est-à-dire en dolomie cuite avec du goudron. Mais ce revêtement, quoique bon marché, ne permet pas d'élaborer plus d'une soixantaine de charges[10],[11] : les briques en magnésie sont généralement nécessaires pour permettre une production sans interruption. En effet, étant donnée la courte durée de vie du revêtement réfractaire, un minimum de deux convertisseurs est nécessaire : pendant qu'un convertisseur est en maçonnage, l'autre est opérationnel. Quand le convertisseur est de petite taille, la cornue est amovible et un pont roulant la transporte vers un atelier de maçonnage[11]. Pour les gros Kaldos sidérurgiques, l'entretien des mécanismes devient critique et il devient préférable d'avoir deux convertisseurs complets, les outils nécessaires étant amenés sur le convertisseur en réfection[34].
Les convertisseurs à l'oxygène pur ne peuvent pas fonctionner sans une unité de traitement des gaz chauds, mais le Kaldo ne nécessite qu'un petit dépoussiérage classique. En effet, les convertisseurs à l'oxygène sont soit équipés d'une installation complexe de récupération du gaz pour une autre utilisation, soit brûlent leur gaz à sa sortie du convertisseur, avant de traiter les fumées obtenues dans un dépoussiérage compatible avec les volumes et les températures générées. En comparaison, le Kaldo génère des volumes réduits de fumées essentiellement constituées de poussières, de CO2 et d'une faible quantité de CO[34].
Dans la métallurgie des non ferreux, en particulier celle concernant le recyclage de déchets ou le traitement de métaux lourds, les Kaldos-TBRC sont installés dans des enceintes closes en légère dépression[29].
Conversion de la fonte
Déroulement d'un soufflage
Le principe général de l'affinage est identique à tous les convertisseurs : il s'agit d'une oxydation des éléments indésirables comme le carbone, le silicium, le phosphore, etc.[11]
La chaux et les ferrailles sont enfournées en premier, puis la fonte en fusion. On limite la quantité de ferrailles pour éviter que la fonte ne se solidifie complètement sur la masse de ferrailles. Le reste de ferrailles, qui peut atteindre la moitié de la quantité totale, est enfourné au plus tôt 10 minutes après le début du soufflage[11].
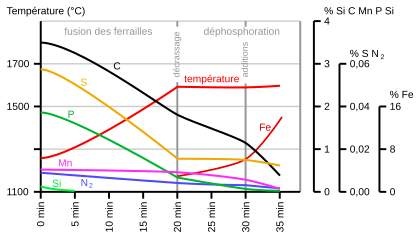
Le soufflage commence immédiatement après la mise en place de la hotte, et atteint son maximum au bout de quelques minutes. La vitesse de rotation est également maximale, soit environ 30 tr/min. Le métal tombe en pluie dans l'atmosphère oxydante du convertisseur, ce qui favorise sa décarburation. De même, les réactions avec le laitier sont favorisées par l'augmentation de la surface de réaction : combinée avec le milieu oxydant, cette configuration permet de commencer la déphosphoration immédiatement[note 6],[11].
20 minutes après le début de soufflage, toutes ferrailles sont refondues. Le débit d'oxygène est alors réduit de moitié, la rotation est ralentie entre 10 et 12 tr/min. La lance souffle au ras du bain : l'objectif est d'oxyder au maximum la charge pour continuer la déphosphoration. Mais le laitier, dont la basicité est maintenue, voire renforcée, par des additions de chaux, s'enrichi en FeO : il devient alors de plus en plus visqueux, jusqu'à former un garni isolant à l'intérieur du convertisseur. Le métal ne peut plus recevoir de chaleur du réfractaire, tandis que les pertes en fer augmentent[11].
Par conséquent, il est nécessaire de vidanger le laitier tant que celui-ci est encore fluide et dépourvu de fer. Mais la déphosphoration nécessite une certaine quantité de laitier. Avec une addition de chaux, on recrée donc une faible quantité de laitier, mais celui-ci est pur et fortement basique[11].
Pendant la déphosphoration, le convertisseur tourne de plus en plus lentement, entre 6 et 8 tr/min. Le laitier, très visqueux, devient progressivement une croûte solide. À la fin du soufflage, on perce cette croûte, et le métal est vidangé tandis que le laitier reste dans le convertisseur[11].
À la coulée suivante, ce laitier, riche en chaux, en fer et en oxygène, réagit la fonte[11] :
- l'oxyde de fer est réduit par le carbone de la fonte : il y a production de monoxyde de carbone et le laitier restitue le fer ;
- le silicium de la fonte est oxydé en silice : le laitier perd son caractère ultra-basique et redevient fluide.
La chaleur produite par la combustion du CO en CO2 est le triple de celle obtenue par la formation du CO. La combustion totale du carbone apporte 25 121 kJ/kg et, avec une gestion appropriée de la lance, il est possible d'oxyder 90 % du carbone de la fonte[34].
Performances
Contrairement aux procédés anciens (Bessemer, Martin ou Thomas) dopés avec l'adjonction d'oxygène qui conservent de strictes impositions sur la qualité de la fonte traitée, le procédé Kaldo est capable de traiter n'importe quel type de fonte. La charge peut être composée de 25 %[4] à 45 % de ferrailles[35]. Un des grands avantages du procédé Kaldo est de pouvoir favoriser la déphosphoration indépendamment de la décarburation, en orientant le jet d'oxygène à l'interface métal-laitier afin de favoriser les réactions entre ces deux liquides[36] :
Vitesse de rotation | Vitesse du jet d'oxygène | Hauteur de la lance | Angle lance/bain | |
---|---|---|---|---|
Désilication | rapide | faible | ||
Décarburation | rapide | élevée | bas | pénétrant |
Déphosphoration | lent | faible | haut | rasant |
Combustion du CO | rapide | rasant |
Le transfert de chaleur se fait de gaz à liquide, ce qui explique des durées d'affinage plus importante que les dérivés du LD, où peu d'échanges de chaleur ont lieu[34] : 70 minutes contre 40 pour une charge LD[5]. Dans les années 1960 le principal procédé concurrent du Kaldo est le procédé LD-AC. Un critère de choix du LD-AC au détriment du Kaldo est la rapidité d'affinage : ainsi, les usines habituées au procédé Thomas (comme la Stewarts & Lloyds à Corby) ont souvent préféré les dérivés du procédé LD, alors que celles qui exploitaient le procédé Martin-Siemens (comme la Park Gate à Rotherham), privilégiant la qualité à la productivité, ont préféré le Kaldo[37].
L'usure du réfractaire est le gros inconvénient du Kaldo : à l'aciérie de Gandrange, 425 m3 de réfractaires étaient consommés en 160 coulées (une semaine de production), contre 250 coulées à la même époque pour l'OLP[38]. En 1978, les réfractaires de l'OLP tiennent 400 coulées, ceux du LD 600 coulées, alors que ceux du Kaldo n'ont pas du tout progressé[33].
Kaldo Dolomie-goudron |
Kaldo Briques magnésiennes |
OLP Briques magnésiennes |
LD Briques magnésiennes | |
---|---|---|---|---|
Domnavert (1963)[34] | 85 | 272 | ||
Gandrange (1969)[33] | 160 | 250 | ||
Gandrange (1974)[33] | 160 | 400 | 600 |
Un convertisseur Kaldo coûte 50 % plus cher qu'un convertisseur LD de capacité interne identique. L'usure des réfractaires est 30 à 50 % plus rapide : les maçonnages qui immobilisent le convertisseur limitent sa production annuelle à 50 à 60 % de celle d'un convertisseur LD de capacité identique[39]. Et si on prend en compte les plus longues durées de soufflage, la capacité annuelle passe sous les 50 %[5].
Utilisation dans la métallurgie des non ferreux
La différence essentielle entre l'affinage de la fonte par le Kaldo, et le traitement des métaux non ferreux par le TBRC réside en l'utilisation fréquente d'un brûleur oxy-fuel en lieu et place de la lance oxygène[40]. Alors que la lance à oxygène ne permet d'obtenir qu'une oxydation exothermique, le brûleur permet, outre la fusion de métal, d'entretenir des réactions endothermiques. Mais surtout, des réactions de réduction deviennent possibles, élargissant l'utilisation du TBRC à l'affinage de presque tous les métaux.
La diversité des procédés envisageables (oxydants, réducteurs, avec ou sans scories, exothermiques, etc.) fait qu'il n'existe pas, à proprement parler, de « procédé TBRC », mais d'un outil, le convertisseur rotatif, dans lequel un très grand nombre de réactions sont possibles, notamment parce que le brassage du contenu est indépendant de la réaction en cours. Ainsi, l'utilisation du TBRC s'apparente à celle d'un four à réverbère dont les échanges sont améliorés par l'agitation du bain[36].
Traitement du cuivre
L’utilisation du TBRC pour la fusion des minerais concentrés de sulfures de nickel (pentlandite) et de cuivre (chalcopyrite) a été mis au point dans les années 1960 par Inco. Le procédé consiste généralement en trois étapes : la fusion du concentré, l'oxydation de la matte puis sa réduction en métal[28].
La fusion du minerai peut être réalisée dans un TBRC dédié. Après la phase de chargement du minerai, la charge est portée à fusion (soit 1 350 °C[28]) par une lance brûlant du gaz naturel et de l’oxygène. Le convertisseur est incliné de 15° à 18° mais la rotation ne commence qu’après la formation d’un bain de matte liquide. Du minerai concentré et des fondants sont alors ajoutés continuellement jusqu’à ce que la quantité désirée ait été enfournée[40].
Le soufflage d’oxygène pur est destiné à évacuer le soufre sous la forme de dioxyde de soufre (SO2). L’oxydation exothermique des sulfures prolonge la chauffe sans apport de combustible, même si une partie du potentiel thermique a été déjà consommée lors de la phase précédente de fusion (dans le cas ou la fusion a été a été menée de manière oxydante, c’est-à-dire avec un excès d’oxygène)[40]. A la fin de cette phase, le convertisseur tourne de 10 à 25 tr/min et la température du bain atteint 1 600 °C. Les fortes températures mises en œuvre nécessitent l’emploi d’un revêtement réfractaire en briques de chrome-magnésite. Malgré leurs performances, ces briques subissent une usure considérable : pour éviter que la scorie ne dissolve rapidement le réfractaire, on la sature en magnésie et on diminue la température de coulée[28]. Le résultat de cette fusion est une matte blanche, qui ne contient presque plus de fer, mais reste riche en soufre[40].
La dernière phase de réduction est obtenue par du coke de pétrole[28]. Elle peut être réalisée dans un second TBRC dédié, le premier TBRC recyclant les scories qui se sont enrichies en oxydes de cuivre. Dans ce cas, elle sert essentiellement à récupérer les métaux précieux (or, argent, platinoïdes) contenus dans le minerai[40].

Cependant, l’extraction de cuivre primaire, c'est-à-dire à partir de minerai concentré, avec un TBRC a été abandonnée dans les années 1970-1980, au profit du soufflage par le fond (procédé Manhès-David avec un convertisseur Peirce-Smith), plus productif[28],[30]. À partir des années 1990, Inco réserve le TBRC à la toute dernière étape d’affinage pyrométallurgique, après une flottation sélective du « blister de cuivre-nickel ». L’étape de fusion est en effet dorénavant réalisée par une fusion flash et l’oxydation est assurée par un convertisseur Peirce-Smith. Comme pour la sidérurgie, l’utilisation de plusieurs outils spécialisés s'est révélée plus adaptée à la production de masse qu'un unique outil polyvalent[20]. Les coûts d’exploitation élevés ont également condamné cette utilisation :
« Les convertisseurs rotatifs à soufflage par le haut (TBRC) ont été aussi utilisés dans le passé pour l'extration du cuivre primaire. Ils ne sont plus utilisé pour l'extraction primaire, essentiellement à cause des coûts d'exploitation élevés, mais ce type de four est utilisé pour l'extraction secondaire[29]. »
— G. Cusano et al., Best Available Techniques (BAT) Reference Document for the Non-Ferrous Metals Industries
En effet, le TBRC est un four idéal pour le recyclage de déchets cuivreux, qui brûlent très bien dans le four rotatif. Il est possible de constituer une charge composée à 25 % de mélanges cuivreux lors d'un fonctionnement à l'oxygène pur, ou de n'utiliser que des déchets en brûlant du fioul et de l'oxygène avec la lance[30]. Par ailleurs, ces déchets peuvent être de nature très variable, avec une teneur en cuivre descendant jusqu'à 10 %[41].
Les scories issues du recyclage du cuivre sont chargées en métaux lourds mais un petit TBRC dédié s'avère capable d'en récupérer le plomb et l'étain. Ainsi, un alliage plomb-étain peut être obtenu comme sous-produit du recyclage du cuivre[29],[32]. Dans ce petit TBRC, le plomb et l’étain sont extraits des scories par une réduction, en présence de ferrailles et de cannettes étamées. L'alliage est affiné ensuite dans d'autres outils dédiés qui ôtent le cuivre, le nickel et le fer[29].
Traitement du nickel
Étant données les similitudes entre la métallurgie extractive du nickel et du cuivre, les procédés mis au point pour l’extraction du nickel sont comparables à l'extraction de cuivre à partir de minerai concentré[40]. Le TBRC oxyde la matte de nickel, qui est généralement riche en cuivre, afin d'en retirer le soufre et le fer. Le retrait du fer prépare l'étape suivante d'extraction du nickel par carbonylation (procédé Mond)[42].
Comme pour l'extraction de cuivre, l'utilisation d'un TBRC pour le nickel est une alternative au procédé Manhès-David et au procédé Ausmelt. Mais sa capacité à effectuer une réduction lui permet de traiter plus efficacément des minerais complexes et d'extraire le métal des scories[43].
Traitement du plomb
L'extraction du plomb, industrialisée par l'entreprise suédoise Boliden AB en 1976 dans son usine de Rönnskär, consiste en trois étapes : la fusion, l'oxydation puis la réduction[31].
La fusion est oxydante. Suivant la nature de la charge, elle peut se faire de deux manières :
- pour la fusion de minerai concentré (à 72 %[44]), l'oxydation des minerais sulfurés avec l'oxygène apporté par la lance (air à 60 % d'O2[44]) est suffisante pour obtenir la fusion de la matte sans apport de combustible[30] ;
- pour le recyclage de déchets, une lance oxygène-gaz naturel chauffe la charge jusqu'à 1 050 °C[45].
L'oxydation du plomb, qui suit la fusion, prolonge cette chauffe car elle est exothermique. Le but de cette étape est d'oxyder un maximum d'impuretés. Dans le cas de la fusion de minerai concentré, il s'agit du soufre qui est évacué sous forme gazeuse (SO2). Les scories s'enrichissent en plomb, jusqu'à contenir 30 % de plomb sous forme de litharge (PbO)[30]. Dans le cas du recyclage de déchets, de l’oxygène pur est soufflé jusqu'à ce que le bain atteigne une température de 1 350 °C[45].
Après cette phase oxydante, qui élimine partiellement les impuretés, on termine dans le même four par une phase de réduction. Cette phase consiste à brûler[note 7] du poussier de coke de pétrole avec un déficit d'oxygène afin de produire le monoxyde de carbone chaud qui est le gaz réducteur[30]. La carboréduction transforme l'oxyde de plomb des scories en plomb métallique, qui retourne dans le bain de métal en fusion[45].
Malgré la consommation de 40 kg de coke et 30 L de fioul par tonne de plomb[29], ainsi que l'électricité nécessaire à la production d'oxygène, le TBRC est plus économe en énergie que les chauffes nécessaires aux procédés alternatifs[44]. Mais ce procédé n’est pas compatible avec de grandes capacités de production. Il est cependant flexible et peut traiter des matériaux très divers (batteries, scraps, etc.)[45].
Traitement de l'étain
L'utilisation du TBRC à la métallurgie extractive de l'étain, mise au point en 1974 par la Metallo-Chimique[21], consiste à extraire l'étain en deux étapes : une fusion réductrice de concentrés de cassitérite permet d'obtenir du zinc métallique en fusion, puis une sulfuration permet de créer du sulfure d'étain (SnS) gazeux, qui est capté par le système de traitement des fumées[32].
La lance brûle premièrement du combustible (mazout ou gaz) avec de l'oxygène pur, déficitaire vis-à-vis de la stœchiométrie afin d'obtenir une atmosphère réductrice. Après l'achèvement de cette phase de fusion réductrice du minerai concentré, l'étain métallique brut, qui s'est rassemblé au fond du convertisseur, est coulé[32].
La scorie restant dans le four est traitée par plusieurs additions de pyrite, tout en augmentant la vitesse de rotation et en maintenant un rapport O2/gaz naturel de 1,5/1 (de façon à maintenir l'atmosphère réductrice). L'étain de la scorie se combine alors au soufre afin de créer du sulfure d'étain. Ce composé, qui se volatilise au-delà de 1 180 °C, est expulsé hors du four par un jet d'air qui remplace le jet d'oxygène[note 8]. La vitesse de rotation est également accrue jusqu’à ce que la scorie ne contienne plus qu'une teneur en étain négligeable (jusqu'à moins de 0,1 % en masse)[32].
À la fonderie d'étain de Texas City, aux États-Unis, l'adoption du TBRC à l'extraction de l'étain en 1978 a permis de passer d'un procédé complexe combinant plusieurs fours, à une seule opération dans un TBRC tournant à grande vitesse[48]. Concentrer les opérations dans un seul outil a notamment simplifié la mise en conformité environnementale de l'usine[47].
Pour l'extraction de l'étain, l’emploi d'oxygène pur minimisant le volume des fumées, four rotatif peut transférer efficacement leur chaleur au bain[32].
Traitement des métaux précieux
L'extraction des métaux précieux, notamment ceux du groupe du platine, se caractérise par les faibles quantités de produits à traiter, notamment dans les étapes finales. Dans ce contexte, certains procédés ne sont pas adaptés : l'affinage des mattes concentrées en éléments précieux, obtenues lors du traitements de minerais sulfurés de nickel et de cuivre ne peut pas être fait classiquement dans un convertisseur Peirce-Smith car son soufflage sous le bain impose de mettre en œuvre une quantité minimale (plusieurs tonnes) de produit. Le TBRC est alors utilisé car, même miniaturisé, il reste efficace : la raffinerie de platine d'Acton opère ainsi un TBRC de 0,25 m3 tournant à 2 tr/min[43].
Les faibles quantités condamnent également les procédés continus. Le TBRC étant capable de refondre des lots de produits, il est systématiquement utilisé comme outil de fusion. Après un affinage pyrométallurgique, généralement oxydant et souvent suivi d'une réduction, il prépare la matte pour l'étape suivante de séparation des éléments par lixiviation[43].
Les TBRC sont adaptés au traitement d'une grande variété de produits contenant des métaux précieux : les précipités de Merrill-Crowe, les croutes de zinc issues de la désargentisation du plomb, les boues d'anodes issues de l’affinage électrolytique du plomb et du cuivre, des déchets électroniques, des chûtes et des déchets de pellicules photographiques[49], des cendres, des poussières, des boues[29]… Dans tous ces usages, ils ont remplacé les fours à réverbères traditionnellement utilisés, à cause de leur plus grande efficacité et productivité[49].
La valeur, la complexité et les volumes traités impliquent des méthodes de travail particulières. Par exemple, l'usine métallurgique de Rönnskär, en Suède, dont un des 3 TBRC qu'elle opère est dédié à la récupération des métaux précieux, isole cette activité dans une unité distincte[50].
Autres métallurgies

Le TBRC est un outil adapté au traitement des crasses d'aluminium[51]. Les procédés les plus courants consistent à refondre[note 9] à environ 800 °C dans un four rotatif les particules d'aluminium retirées des crasses de fonderie, les variantes consistant essentiellement à limiter l'oxydation du métal pendant cette fusion par l'amélioration de la méthode de chauffe (oxycombustion, arc électrique, torche à plasma,…) ou par la protection du bain (protégé par une couche de sel fondu)[52]. Pour cette application, cependant, le TRF (Tilting Rotary Furnace), un four similaire au TBRC mais doté d'un mécanisme de basculement plus simple et d'angle limité, est un choix industriellement plus économique[54].
Le TBRC peut-être également utilisé pour extraire des éléments par vaporisation. Le traitement des fumées permet de récupérer les poussières émises : le sélénium est, par exemple, efficacement récupéré par cette méthode[29].
Élaboration des aciers inoxydables
Le procédé Kaldo a eu une brêve descendance dans l'élaboration des aciers inoxydables, avec le procédé Kaldo-réacteur (ou Kaldo-Vac[55]) mis au point en 1955 par Ugine à son usine d'Aiguebelle[5]. En effet, la production d’aciers inoxydables présente des particularités qui rejoignent les points forts du procédé : élaboration à partir de ferrailles et obtention économique de hautes températures (plus de 1 700 °C). Il ne manque alors qu'à terminer l’affinage oxydant en raccordant la cornue à un générateur de vide, afin de décarburer sans oxyder le chrome, jusqu’aux très basses teneurs en carbone requises par les aciers inoxydables[55]. La combinaison entre ce convertisseur et l'installation de vide a abouti à un outil aussi original que performant :
« Cet appareil était un pur fruit de la culture uginoise, un vrai délire d'ingénieur : exploité en Kaldo durant la première partie du soufflage, la bétonnière était ensuite arrêtée et mise en position verticale ; une cloche à vide venait alors se clamper sur le bec afin de provoquer une décarburation sous vide. Le savoir-faire d'Ugine avait su faire porter la durée de la campagne d'un garnissage à 1 000 coulées[5]. »
— Olivier C. A. Bisanti, Un siècle d'oxygène en sidérurgie
Deux convertisseurs de 70 tonnes sont construits dans ses usines de Moûtiers et de L'Ardoise[5]. Ugine avait également projeté une installation identique à Fos-sur-Mer, pour élargir à la production d'acier inoxydable son usine démarrée en 1973 et dédiée principalement aux aciers à roulements. Mais la crise qui sinistre la métallurgie à partir du milieu des années 1970 a raison du projet. La généralisation du procédé AOD marginalise ensuite le Kaldo-réacteur : en 1982 l'usine de Moûtiers ferme, victime de sa faible taille et de son obsolescence[56], et l’usine de L’Ardoise s'équipe d'un convertisseur AOD[55] de 110 tonnes destiné à remplacer son Kaldo-réacteur qui s'arrête en 1986[5].
Usines construites
Sidérurgie
Nombre de fours | Emplacement | Propriétaire à la mise en service |
Capacité (t) | Date de mise en service | Date d’arrêt | Remarques |
---|---|---|---|---|---|---|
1 | Domnarvets Jernverk (Suède) |
Stora Kopparbergs Bergslags AB | 30 | 1956[13],[11] | 1974[60] | Démonstrateur industriel. Transformé en OBM de 35 t en 1974[60]. |
1 | Aciérie de Florange (France) |
Sollac | 110[5] porté à 140[12] |
1960 | 1980 | Arrêté en même temps que 4 convertisseurs Thomas de 65 tonnes modifiés en LWS, et 4 Martin, au moment de la mise en service des 2 convertisseurs LWS de 240 tonnes[12]. |
2 | Oxelösunds Järnverks (Suède) |
Gränges AB | 130 | 1961[13] | 1977[61] | En 1967, 2 Kaldos supplémentaires sont annoncés[62], mais un seul LD-LBE de 170 t à cornue remplaçable[61] remplace les 2 Kaldos en 1977[63]. |
2 | Roemer Works (États-Unis) |
Sharon Steel Corporation | 140 porté à 150[64] |
1962[13] | 1980[65] | Durée de vie du garnissage de 220 t[36] : 120 coulées. Charge constituée de fonte non phosphoreuse[34] et de 50% de ferrailles. Projet pour un 3e Kaldo en 1964[66]. Installation d'un LD 150 tonnes en 1977, puis d'un deuxième en 1980, qui remplacent les Kaldos[65]. Mais les 2 Kaldos sont « virtuellement supplantés » par un seul convertisseur LD dès 1977[67]. |
2 | Park Gate Works (Grande-Bretagne) |
Tube Investments | 75 porté à 80[13] |
1964 | 1975[68] | Premiers Kaldos britanniques[35]. |
2 | Aciérie de Consett (Grande-Bretagne) |
Consett Iron Company | 100 porté à 120[69] |
1964[13] | 1968-1971[70] | Aciérie équipée de 2 convertisseurs LD (et non pas LD-AC) et 2 Kaldos, tous de 100 tonnes de capacité. 2 Kaldos supplémentaires étaient prévus[71] mais ne furent jamais construits. En 1966, la production Kaldo est devenue marginale [72], les minerais à bas phosphore devenant bon marché tandis que les performances du LD s'améliorent. En 1968, un Kaldo est transformé en troisième LD de 150 tonnes et, en 1971, le dernier Kaldo transformé de la même manière[70]. |
2 | Shelton Bar (Grande-Bretagne) |
John Summers & Sons | 50 porté à 55[73] |
1964[13] | 1978[73] | Construction associée à celle d'une coulée continue de blooms[73]. |
1 | Norrbottens Järnverk (Suède) |
Norrbottens Järnverk AB | 70 | 1964[13] | 1974[63] | En 1971, décision de remplacer l'aciérie Kaldo par une aciérie LD et des coulées continues afin de retrouver la rentabilité[74]. L'investissement a été réalisé en 1974-1975[75] et a permis l'abandon de la filière Kaldo[63]. |
1 | Stanton Ironworks (Grande-Bretagne) |
Staveley Coal and Iron Company | 70 | 1965[13] | 1967[76] | Four destiné à l'affinage de fonte phosphoreuse. Procédé abandonné au bout de 2 ans[76]. |
1 | La Providence de Marchienne (Belgique) |
Forges de la Providence | 35[77] | 1965[11] | 1980[78] | Convertisseur LD-Kaldo, qui a été également utilisé comme outil de recherche. Seul le soufflage final déphosphorant est réalisé en mode Kaldo[79]. La combinaison des deux procédés permet de ménager les réfractaires tout en conservant les performances métallurgiques du Kaldo. Mais la disparition de la première phase de combustion du CO pénalise le recyclage des ferrailles[11]. |
2 | Domnarvets Jernverk (Suède) |
Stora Kopparbergs Bergslags AB | 80 porté à 100[80] |
1965[13],[81] | 1981[82] | Ces fours pouvaient réaliser une réduction directe du minerai de fer et une fusion. Le procédé, nommé Dored, n'a jamais atteint le stade industriel[83]. Le remplacement des Kaldos par des LD est évoqué dès le début des années 1970[63]. |
2 | Aciérie de Gandrange (France) |
Sacilor | 240 | 1969 | 1982[12] | Durée de vie du garnissage : 160 coulées. Plus grands convertisseurs Kaldo jamais mis en service[38]. Arrêtés après la modernisation des 2 convertisseurs OLP construits en 1971 dans la même aciérie[12]. |
Métaux non ferreux
Nombre de fours | Emplacement | Propriétaire à la mise en service |
Capacité (t ou m³[note 12]) |
Date mise en service | Date d’arrêt | Remarques |
---|---|---|---|---|---|---|
1 | Beerse (Belgique) |
Metallo-Chimique | 70 t de cuivre | années 1960[note 2] | Recyclage de déchets cuivreux. Production d'un cuivre noir pur à 98 %, ou d'un alliage cuivre-nickel à 10 % de nickel[85]. | |
1 | Chouteau Township (États-Unis) |
Chemetco | 70 t de cuivre | 1970[24] | 2001[86] | Recyclage de déchets cuivreux, procédé développé par la Metallo-Chimique[23]. Usine fermée pour pollution de l'eau[86]. |
2 | Copper Cliff (Canada) |
Inco | 20 m³ 50 t de nickel[20] |
1971[20] | 2002[87] | Premiers convertisseurs industriels Kaldos dédiés à la métallurgie des non ferreux et nommés TBRC par Inco. Ils sont dédiés à l'affinage de matte de nickel[20]. |
2 | Tennant Creek (Australie) |
Peko Wallsend | 25 t | 1973[88] | 1975[89] | Conversion de minerai cuivreux contenant du bismuth[88]. |
2 | Beerse (Belgique) |
Metallo-Chimique | 13 m³ 70 t de cuivre |
1974[21] | Traitement du laitier riche en étain, en plomb, en cuivre et en nickel, issu du recyclage du cuivre dans le premier TBRC[85],[90]. | |
1 | Beerse (Belgique) |
Metallo-Chimique | 10 t de plomb-étain | 1974[21] | Recyclage de déchets ou d'oxydes de plomb et d'étain[85]. | |
1 | Rönnskärsverken (Suède) |
Boliden AB | 13 m3 90 t de plomb[30] |
1976 | Premier Kaldo au monde affinant de la matte de plomb. Initialement dédié au traitement des poussières issues de la production de cuivre, puis est devenu un outil polyvalent, recyclant déchets de cuivre et de plomb[31]. | |
3 | Soroako (Indonésie) |
Inco | 20 m³ | 1977[91] | 1987-1988 | Conversion d'une matte à 32 % de nickel en ferronickel. 2 Kaldos remplacés par 2 convertisseurs Peirce-Smith, le 3e étant stoppé[91]. |
1 | Rönnskärsverken (Suède) |
Boliden AB | 13 m3 | 1978 | 1989 | Production de matte de cuivre riche (60-65% Cu) à partir de minerai concentré. Arrêté pour manque de disponibilité de minerai[30]. Revendu et redémarré en Inde en 2002[92]. |
1 | Mine d'Afton-Ajax (Canada) |
Teck Mining | 20 m³[84] 45 t de cuivre[93] |
1978[89] | 1983[93] | Fusion directe de concentrés de cuivre en blister. |
1 | Philadelphie (États-Unis) |
Franklin Smelting & Refining Company | 15 t | 1996[94] | Conversion de cuivre noir en blister (initialement). Usine fermée à cause des contraintes environnementales[94]. | |
1 | Philadelphie (États-Unis) |
Franklin Smelting & Refining Company | 25 t | 1996[94] | Conversion de cuivre noir en blister (initialement). Usine fermée à cause des contraintes environnementales[94]. | |
1 | Tex-Tin (États-Unis) |
Gulf Chemical and Metallurgical Company | ? | 1978 | 1991[48] | Fusion de concentrés d'étain et réduction des scories d'étain[32]. Abandonné en 1989 par pénurie de minerais concentrés importés compétitifs, et reconverti dans le traitement du cuivre. Arrêt définitif en 1991 à la suite de l'effondrement du convertisseur[48]. |
3[95] | Chouteau Township (États-Unis) |
Chemetco | 13 m³ 70 t de cuivre[96] |
1981-1982[96] | 2001 | Recyclage de déchets cuivreux riches à 50 %, ainsi que la récupération d'étain. Usine fermée pour pollution de l'eau[86]. Convertisseurs identiques aux 2 Kaldo de 70 tonnes de la Metallo-Chimique[90]. |
1 | Zanjan (Iran) |
National Iranian Lead and Zinc | 13 m³[97] | 1983[97] | 2013[98] | Coupellation de matte de plomb[97],[99]. Usine fermée en mi-2013 pour des raisons environnementales[98]. |
1 | Francfort-sur-le-Main (Allemagne) |
Degussa | 6 t | Coupellation de matte de plomb. | ||
1 | Rönnskärsverken (Suède) |
Boliden AB | 6 t | Coupellation de matte de plomb. | ||
1 | Columbus (États-Unis) |
Stillwater Mining Company | 7 m³[100],[note 13] 5 t de matte[102] |
1990[101] | Fusion d'une matte riche en platinoïdes et oxydation pour obtenir un métal blanc contenant 75 % Cu+Ni et 2,5 % de métaux précieux[101]. | |
1 | Marghera (Italie) |
SIMAR SpA | 1992[103] | 2000 | Affinage de cuivre. Fermé par manque de déchets cuivreux disponibles[104], tentative de relance en 2010[103]. | |
1 | Bharuch (Inde) |
SWIL | 13 m³[92] 60 t de cuivre[105] |
2002[104],[92] | Produit en 12 heures une matte d'environ 70% de cuivre à partir de déchets cuivreux. Il s'agit du convertisseur de Bolinden arrêté en 1989 et relocalisé en Inde[92]. Arrêté de 2009[106] à 2017[107]. | |
1 | Xiangguang Yanggu Smelter | Récupération de métaux précieux dans la matte de cuivre[108] | ||||
1 | Jiangxi Copper | 2009 | Recyclage de cuivre Cu>70%. Associé à un four à réverbère[109]. | |||
1 | Western Mining Co., à Xining (Chine) |
Qinghai Xiyu Nonferrous | 13 m³[110] | 2010[97] | Coupellation de matte de plomb[97]. Remplace des hauts fourneaux fermés à cause des contraintes environnementales. Technologie de Boliden[110]. | |
2 | Jinchuan smelter (Chine) |
Jinchuan Group | 13 m³[109] | 2011 | Recyclage de cuivre Cu>80%. Associé à un four à sole oscillante[109]. | |
1 | Lünen (Allemagne) |
Aurubis | 100 t de cuivre[111] | 2011 | Addition de déchets dans du cuivre noir (80% Cu) pour en faire du cuivre à 95 %. L'étain et le plomb y sont retirés avec le laitier[112] | |
1 | Rönnskärsverken (Suède) |
Boliden AB | 2012 | Recyclage de déchets électroniques cuivreux[113]. | ||
1 | Wuzhou Recycling Industrial Park (Chine)[114] |
Guangxi Non-ferrous Metals (en) | 2012 | Recyclage de cuivre 20%<Cu<90%. Associé à un four à réverbère[109]. Repris en 2018 après la faillite de Guangxi Non-ferrous Metals, pour recycler des déchets >10% Cu[115]. | ||
1 | Zijin Copper (Chine) |
Jinchuan Group | 2013[116] | Affinage de matte de cuivre issue d'un four de fusion flash[109]. | ||
4 | Richmond (États-Unis) |
Aurubis | 12 m³[117] | 2024-2026 (prév.)[118] | Recyclage de déchets électroniques cuivreux[118]. |
Évolutions et disparition
Sidérurgie
Au moment de son apparition, le procédé Kaldo combine beaucoup d'avantages : il traite les fontes phosphoreuses, permet de recyclage d'une grande quantité de ferrailles et permet un contrôle facile de l'affinage. Mais sa complexité le pénalise : c'est « un procédé élégant sur le papier mais d'une exploitation difficile »[5].
Partant de ce constat, des convertisseurs rotatifs contemporains du Kaldo ont été évalués comme alternative :
- le procédé Rotor, industrialisé au début des années 1950 à l'usine d'Oberhausen est également un convertisseur à l'oxygène rotatif[119]. Il s'agit d'un procédé plus simple et plus conventionnel : le four tubulaire s'incline peu et n'effectue qu'une rotation toutes les 2 minutes. La rotation est plus destinée à homogénéiser l'usure des réfractaires qu'à accélérer les réactions chimiques. Celles-ci sont gérées par deux lances à oxygène : une pour la décarburation, l'autre pour la post-combustion des fumées au sein du four[3],[120] ;
- le Kaldo-LD installé en 1965 dans l'aciérie de Marchienne-au-Pont est un Kaldo doté d'une lance et d'un dépoussiérage vertical de type LD. La combinaison des deux procédés permet d'améliorer la durée de vie des réfractaires tout en conservant la flexibilité et les performances métallurgiques du Kaldo. Le soufflage commence en mode LD, c'est-à-dire verticalement, puis la déphosphoration en mode Kaldo. Cependant, outre la complexité accrue, ce séquencement supprime la première phase de combustion du CO propre au Kaldo, et donc la possibilité de refondre de grandes quantités de ferrailles[11]. Et la suppression du trou de coulée latéral LD dégrade la qualité de la vidange de la cornue, qui est un point fort du LD[79].
Les limitations de ces procédés alternatifs les rendent moins attractifs que le Kaldo. Mais les inconvénients du Kaldo sont évidents. Outre la tenue des réfractaires, la chaleur dégagée par la combustion du CO sollicite également la carcasse métallique, notamment la piste de roulement circulaire[81]. À la fin des années 1950, les convertisseurs à l'oxygène soufflent des charges de 50 à 75 tonnes. Dans les années 1960, la plupart des nouveaux convertisseurs ont une capacité de 220 à 300 tonnes. Mais la taille des convertisseurs Kaldo plafonne alors à 100 tonnes : elle évolue donc beaucoup moins vite que celle des convertisseurs LD[66] et la tentative de rattrapage par l'aciérie de Gandrange sera un échec technique[19].
En fait, le Kaldo est condamné par l'évolution du métier. En effet, c'est un convertisseur où le métallurgiste s'efforce de réaliser à la fois la conversion de la fonte en fer, la mise à nuance et la chauffe exacte avant la coulée. Or, à partir des années 1950, les exigences croissantes dues à l'évolution de la métallurgie comme à la généralisation de la coulée continue condamnent progressivement cette approche : seuls des outils spécialisés peuvent atteindre les exigences requises. Ainsi se développe la métallurgie en poche : le convertisseur fournit un acier de composition et de température approximatives, que des outils en aval traitent de manière plus fine. La spécialisation de chaque outil permet d'améliorer la productivité et compense le coût entraîné par la complexification des aciéries. Dans cette évolution, la productivité du procédé LD l'emporte sur la polyvalence du Kaldo[121]. Et si le rendement thermique du Kaldo est séduisant, en sidérurgie, le gaz de convertisseur généré par les procédés alternatifs, comme le LD, est riche en CO et peut être avantageusement brûlé dans les fours de l'usine. Or après le premier choc pétrolier, ce type de gaz est devenu incontournable dans le bilan énergétique d'un complexe sidérurgique[5].
Métaux non ferreux
Dans les non ferreux, le TBRC a failli disparaitre avant de rencontrer, après les années 2010[122], un regain d'intérêt dans la fusion des déchets, notamment cuivreux, où sa flexibilité lui permet de s'adapter à des charges très variables[30]. Sa compacité et son aptitude à traiter des minerais contenant beaucoup d'impuretés le rendent également intéressant dans les fonderies de petites tailles ou pour des augmentations incrémentales de production dans des usines existantes[123]. Des TBRC sont ainsi régulièrement installés : par exemple, au début du XXIe siècle, l'entreprise SMS Group revendique avoir installé plus de 40 convertisseurs[124], et son concurrent Outotec en compte 17[125].
Au-delà du cuivre, l'aptitude du TBRC à traiter la plupart des métaux les non ferreux est reconnue mais il s'est révélé inadapté à la production de masse[126]. Mais les petits TBRC, d'une capacité de 0,5 à 10 tonnes, sont des outils sans équivalents dans la récupération de métaux précieux[49]. Leur petite taille et une conception simplifiée font disparaitre les soucis mécaniques qui ont handicapé les engins sidérurgiques. La possibilité de réaliser beaucoup d'opérations successives dans le même réacteur limite les pertes et la pollution. La compacité et l'efficacité thermique du four ont amené le TBRC à remplacer les derniers fours à réverbères[49].
Notes et références
Notes
- Le soufflage d'oxygène pur par le fond ne sera mis au point que dans les années 1970, avec les procédés de type OBM (Oxygen-Bottom Maxhütte).
- Il est difficile de déterminer la date précise de mise en service du premier Kaldo de la Metallo-Chimique. Le convertisseur rotatif y a été adopté pendant les années 1960 pour se généraliser en 1974[21], mais le premier brevet (n° CA979224A) ne date que de 1970. Celui-ci traite de principes généraux sur l'affinage de métaux non ferreux, tout en évoquant des cas industriels relatifs à un convertisseur de 70 tonnes. Par ailleurs, ce brevet, comme les suivants, est déposé uniquement au Canada et aux États-Unis. Il vise donc à éviter tout blocage de la part du concurrent Inco, dont les brevets pourraient gêner une pratique discrètement mise au point[22], mais aussi à protéger les activités de la Chemetco, créée cette année-là sous l'égide des Belges[23].
- Ce sont les ingénieurs Paul Queneau et John Feick, responsables de l'exploitation des convertisseurs Peirce-Smith d'Inco, aidés par John Thompson, ingénieur chimiste et directeur général qui, en 1958, vont explorer la conversion à l'oxygène pur des mattes de nickel. Les TBRC d'Inco deviennent la première étape de la transformation de composés métalliques complexes, jusqu'à l'obtention de nickel pur à 99,98 % par le procédé Mond[20].
- L'affinage de la fonte au convertisseur est facile car la combustion des éléments indésirables est fortement exothermique : l'oxydation du silicium et du carbone y produit respectivement 32,8 et 10,3 kilojoules par kilogramme[26]. À l'inverse, pour affiner une matte de cuivre, il faut d'abord dissocier le fer du soufre, ce qui consomme 6,8 kilojoules par kilogramme de FeS, avant que leur oxydation, qui ne produit, respectivement, que 5,9 et 9,1 kJ/kg, puisse commencer[27].
- L'oscillation de la lance peut être utile en début de soufflage, pour balayer les réfractaires afin d'éviter qu'une croute isolante de laitier se forme et limite l'échange de chaleur entre le métal et le revêtement réfractaire.
- rappeler la chimie du procédé thomas
- Le carbone n'est pas injecté directement dans les scories car la réaction est endothermique. La réaction entre le coke et le PbO se décompose en effet ainsi : C (s) + CO2 (g) → 2 CO (g) consommant 165,4 kJ/mol de CO PbO (s) + CO (g) → Pb (l) + CO2 (g) produisant 95,8 kJ/mol de PbO Le bilan thermique de ces deux réactions est déficitaire : il est alors nécessaire d'apporter de la chaleur[46].
- La fonderie d'étain de Texas City avait initialement envisagé d'extraire l'étain vaporisé sous la forme de dioxyde d'étain. Mais cette extraction s'est avérée lente et pénalisante la productivité. Quelques mois plus tard, l'extraction sous la forme de sulfure d'étain a été mise au point, multipliant la productivité par quatre[47].
- Certains auteurs qualifient l'utilisation du TBRC de centrifugation[52]. Mais la vitesse de rotation, de 1 tr/min, est bien trop faible pour produire cet effet[51]. Surtout, la description détaillée du procédé ECOCENT indique que les crasses d'aluminium sont centrifugées dans un outil distinct[53].
- Les convertisseurs expérimentaux ne sont pas détaillés. Dans cette catégorie, on peut signaler le Kaldo prototype initial de Domnarvet d'une capacité de 3 tonnes et celui du MEFOS (sv) à Luleå de 5 tonnes. Les convertisseurs qui n'ont pas connus d'histoire industrielle, notamment les 2 Kaldos de 60 tonnes que la Sanyo Special Steel Co. a commandé à Krupp pour l'aciérie d'Himeji en 1965, soit au moment de sa faillite et de son passage à la production au four à arc électrique, et pour lesquels aucune production n'a été relevée[57],[58], ne sont pas retenus. De même, le Kaldo-LD 70 tonnes qui aurait été installé en 1973 à Cockerill-Marcinelle[11], qui n'apparait dans aucune archive relative à l'usine et dont la date de construction correspond en fait à la fermeture de l’aciérie Thomas où il aurait dû être installé, a certainement été abandonné au profit du procédé OBM[59].
- Les convertisseurs expérimentaux ne sont pas détaillés. Dans cette catégorie, on peut signaler le Kaldo prototype d'INCO à Port Colborne de 7 tonnes qui a servi à généraliser le TBRC à la métallurgie extractive du cuivre[20], celui du Warren Spring Laboratory à Stevenage de 200 kg, celui du Colorado School of Mines à Golden de 200 kg[84], etc. Les très petits convertisseurs sont également omis, comme celui de 0,25 m3 de l'Acton Pt Refinery à Londres[43].
- En raison de la diversité des produits traités par un même convertisseur, et de leurs densités (de 4 pour une matte pauvre en cuivre, à 11,3 pour le plomb), il est parfois préférable de n'évoquer que le volume de métal traité.
- Une source évoque une taille de TBRC de la Stillwater Co. de 0,15 m3, soit 1,5 t de matte[101].
Références
- (en) F. Wallner et E. Fritz, « Fifty years of oxygen-converter steelmaking », Revue de Métallurgie, no 10, , p. 825-837
- H. Lecompte, Cours d'aciérie, Éditions de la Revue de métallurgie, , 309 p.
- (en) Donald Garmonsway, « A survey of oxygen steelmaking », New Scientist, no 244, , p. 153-155 (lire en ligne)
- (en) D. J. O. Brandt, « British steelmaking today and tomorrow », New Scientist, vol. 2, no 38, , p. 14-17 (lire en ligne)
- Olivier C. A. Bisanti, « Un siècle d'oxygène en sidérurgie », Soleil d'acier,
- Leroy et al., « Soufflage d'oxygène pur par le procédé LWS », La revue de métallurgie,
- (de) Roman Sandgruber, « Das LD-Verfahren erobert die Welt (Les LD conquièrent le monde) », Oberösterreichische Nachrichten,
- (en) James Albert Allen, Studies in Innovation in the Steel and Chemical Industries, Manchester University Press, , 246 p. (ISBN 0678067902 et 978-0678067901), p. 138
- Kalling et al., « Emploi d'oxygène-acide carbonique au lieu d'air pour le soufflage final dans le procédé Thomas », La revue de métallurgie,
- (es) Bo Kalling et Folke Johansson, « Procedimiento Stora Kal-Do de fabricación de acero con oxígeno en aparato rotatorio », dans Problemas de la industria siderúrgica y de transformación de hierro y acero en América Latina, vol. 2, Organisation des Nations unies, (lire en ligne [PDF]), p. 86-88
- (en) B.P. Bhardwaj, Steel and Iron Handbook, Niir Project Consultancy Services, , 472 p. (ISBN 978-9381039304), p. 302-313
- Monique Thouvenin, « De Wendel-Sidélor à Sacilor-Sollac : 1968-1980. 13 années de mutations difficiles en Lorraine. », Revue Géographique de l'Est, vol. 21, no 1, , p. 37-63 (lire en ligne)
- Allen 1967, p. 141
- Allen 1967, p. 140
- (sl) « Zgradili Bomo Kaldo Konvertor », Železar, , p. 5-7 (lire en ligne [PDF])
- Allen 1967, p. 196
- Allen 1967, p. 202
- Jean-Yves Debost et Bernard Réal, Les rapports des industries de la manutention avec l'évolution des processus de production et des moyens de transport dans le cours de l'internationalisation du capital, Université des Sciences Sociales de Grenoble, Institut de Recherche Economique et de Planification, (lire en ligne [PDF]), partie 2, p. 48
- Michel Freyssenet, La sidérurgie française 1945-1979 : L'histoire d'une faillite. Les solutions qui s'affrontent., Paris, Savelli, coll. « Documents critiques », , 241 p. (ISBN 9782859300302, OCLC 417353871, BNF 34648522, présentation en ligne, lire en ligne [PDF]), p. 81-82
- (en) Paul E. Queneau et Samuel W. Marcuson, « Oxygen Pyrometallurgy at Copper Cliff—A Half Century of Progress », The Minerals, Metals & Materials Society, (lire en ligne)
- « Historique de Metallo Chimique N.V. »
- (en) « Process for recovering copper from copper-bearing materials (CA 979224 A) »
- (en) « Chemetco closing today », The telegraph, Alton, , p. 1 ; 9 (lire en ligne)
- (en) L. R. Verney, « Pyrometallurgy », Journal of The Minerals, vol. 29, , p. 16–18 (ISSN 1543-1851, DOI 10.1007/BF03354304, lire en ligne)
- (en) « Nickel refinery in Canada optimizes the process of rotary converter exchange », Vale,
- Adolf Ledebur (trad. Barbary de Langlade revu et annoté par F. Valton), Manuel théorique et pratique de la métallurgie du fer, Tome I et Tome II, t. 2, Librairie polytechnique Baudry et Cie éditeur, [détail des éditions], p. 472
- Paul Louis Weiss, Le Cuivre : Origine, Gisements, Propriétés physiques et chimiques, Métallurgie… Marché du cuivre, Principales applications… Alliages industriels, J.-B. Baillière et fils, , 344 p. (ASIN B0019TU3SK, lire en ligne), p. 191-193
- Pierre Blazy et El-Aid Jdid, « Pyrométallurgie et électroraffinage du cuivre - Pyrométallurgie », dans Techniques de l'ingénieur, Éditions techniques de l'ingénieur (lire en ligne)
- (en) Gianluca Cusano, Miguel Rodrigo Gonzalo, Frank Farrell, Raine Remus, Serge Roudier et Luis Delgado Sancho, Best Available Techniques (BAT) Reference Document for the main Non-Ferrous Metals Industries, EUR 28648,, Union européenne, (ISBN 978-92-79-69655-8, ISSN 1831-9424, DOI 10.2760/8224, lire en ligne [PDF])
- (en) Lennart Hedlund, « Lead and copper recycling in the Boliden Kaldo », EMC'91: Non-ferrous metallurgy - Present and future, Elsevier, , p. 293-298 (ISBN 1851667156, lire en ligne)
- (en) « Rönnskär's history », Boliden AB (consulté le )
- Jacques de Cuyper, « Métallurgie et recyclage de l’étain - Traitements métallurgiques », dans Techniques de l'ingénieur. Élaboration et recyclage des métaux, Éditions techniques de l'ingénieur,
- Daniel Rivet, L'acier et l'industrie sidérurgique, Paris, Presses universitaires de France, coll. « Que sais-je? » (no 561), , 128 p. (ISBN 2 13 035632 X), p. 37
- (en) F. Johansson, « The Kaldo Process »,
- (en) Fred Wheeler, « Computer chain of command in a steelworks », New Scientist, vol. 23, no 399, , p. 83-84 (lire en ligne)
- (en) R. N. Merk et D. R. Berg, « Sharon Steel's Kaldo Furnaces first in US », JOM (Journal of the Minerals, Metals & Materials Society), vol. 13, , p. 635-636 (lire en ligne)
- Allen 1967, p. 203-205
- Jean Rivet, « La sidérurgie, des origines à nos jours » [PDF],
- (en) Friedrich August Karl Lüth et Horst König, The Planning of Iron and Steelworks, Springer-Verlag, , 193 p. (ISBN 978-3-662-28160-4 et 978-3-662-29671-4, lire en ligne), p. 79
- (en) Background Information For New Source Performance Standards Primary Copper, Zinc, and Lead Smelters Vol I Proposed Standards, vol. 1, EPA, (lire en ligne [PDF]), p. 3-115 ; 3-117
- (en) « Outotec Kaldo furnace for copper and lead » [PDF], Outotec,
- Krundwell et al. 2011, p. 271-275.
- (en) Frank K. Krundwell, Michael S. Moats, Venkoba Ramachandran, Timothy G. Robinson et William G. Davenport, Extractive Metallurgy of Nickel, Cobalt and Platinum Group Metals, Elsevier, , 610 p. (ISBN 978-0-08-096809-4), p. 579-581
- (en) A. Christian Worrell et Mary A. Taft, Overview of foreign nonferrous smelter technology, EPA, (lire en ligne [PDF]), p. 38
- Pierre Blazy et El-Aïd Jdid, « Métallurgie du Plomb - Procédés modernes et sources secondaires - Procédés BSF », dans Techniques de l'ingénieur. Élaboration et recyclage des métaux, Éditions techniques de l'ingénieur,
- (en) H. Y. Sohn et M. Olivas-Martinez, Treatise on Process Metallurgy, vol. 3, Elsevier, (ISBN 978-0-08-100000-7, lire en ligne), A, p. 686-688
- (en) « State v. Associated Metals & Minerals Corp., No. A2408 », (consulté le )
- (en) Superfund record of decision : Texas Tin Corporation Site OU 1, Texas City, TX., EPA, (lire en ligne [PDF]), p. 17
- (en) J.G. Cooper, J.W. Matousek et J.G. Whellock, « Bulk oxygen use in the refining of precious metals », dans George Kachaniwsky, Chris Newman, The impact of oxygen on the productivity of non-ferrous metallurgical processes, vol. 2 : Proceedings of the Metallurgical Society of the Canadian Institute of Mining, Winninpeg, Pergamon Press, (ISBN 0-08-035767-9, lire en ligne), p. 116-118
- (en) Jane Mulenshi, Mapping of settling processes at Boliden Rönnskär and Harjavalta smelters (thèse), Université de technologie de Luleå, (lire en ligne [PDF])
- (en) Stefan Wibner, Helmut Antrekowitsch et Thomas C. Meisel, « Studies on the Formation and Processing of Aluminium Dross with Particular Focus on Special Metals », Metals, MDPI, vol. 11, , p. 1108 (DOI 10.3390/met11071108, lire en ligne)
- Simon Langlois, Revue des technologies de traitement des écumes des écumes d'aluminium et applicabilité dans un cadre de développement durable au Québec (thèse), Sherbrooke, Université de Sherbrooke, (lire en ligne [PDF])
- Brevet CA 2915784A1 "Aluminium dross processing", Frank Pollmann, 2014.
- (en) « Rotary-tilting furnace of the company INTEC (Germany) with the liner of the company "Spetsogneuporkomplekt" » (consulté le )
- Jean Saleil, Marc Mantel et Jean Le Coze, « La production des aciers inoxydables : Histoire de son développement et des procédés de fabrication : Partie II. Évolutions de l’élaboration des aciers inoxydables au four électrique à arc. La tentation de la fonte au chrome et la production d’aciers inoxydables dans l’usine intégrée », Matériaux & Techniques, Société Chimique de France, vol. 108, no 1, (DOI /10.1051/mattech/2020017, lire en ligne [PDF])
- Louis Chabert, Histoire de l'électrochimie et de l'électrométallurgie en Savoie, Chambéry, Société savoisienne d'histoire et d'archéologie, , 36 p., p. 19-36
- (en) « History », Sanyo Special Steel
- (en) « World Kaldo steel plants », Metal Bulletin Journals, , p. 57
- H. Jacobs, A. Marlot, L. Philippe et E. Lété, « L’aciérie OBM de Cockerill-Sambre à Marcinelle », Revue de Métallurgie, Paris, vol. 79, no 1, , p. 13–27 (DOI 10.1051/metal/198279010013, lire en ligne)
- (en) Year Book - Association of Iron and Steel Engineers, , p. 83
- (en) Year Book - Association of Iron and Steel Engineers, , p. 439
- (en) John W. Thatcher, Mineral yearbook, (lire en ligne [PDF]), p. 601
- (sv) Handelsståls industrin inför 1980-talet, Stockholm, (ISBN 91-38-03332-1, ISSN 0375-250X, lire en ligne [PDF]), p. 92-93 ; 97
- (en) Basic oxygen process furnaces, United States Environmental Protection Agency, (lire en ligne), p. 3-5
- (en) Joseph K. Stone et Eduard M. Michaelis, « Worldwide LD steelmaking capacity shows pause », Year Book - Association of Iron and Steel Engineers, , p. 225
- (en) Robert A. Whitman, Mineral yearbook, (lire en ligne [PDF]), p. 619
- (en) Development of thechnology for controlling BOP charging emissions, United States Environmental Protection Agency, (lire en ligne), p. 11 ; 18 ; 21
- « Informations économiques », Revue de métallurgie, vol. 72, , p. 237
- Allen 1967, p. 191
- (en) Louis Cassier, « Consett », Iron and Steel, IPC Science and Technology Press, vol. 45,
- (en) « Consett Iron Company Limited », sur derwentside.com
- (en) John L. Griffith, Some aspects of the effect of atmospheric pollution on the Lichen Flora to the West of Consett Co. Durham, (lire en ligne), p. 14
- (en) « 150 years of the Shelton Works », sur thepotteries.org, p. 29-33
- (en) F. E. Brantley, Mineral yearbook, (lire en ligne [PDF]), p. 617 ; 619
- (sv) Nisl G. Åsling, « om kapitaltillskott till Norrbottens Jämverk AB » [PDF], , p. 4
- (en) « Stanton Ironworks Demolition », Industrial Aperture
- (en) J. Ledune et p. Nilles, « The LD-Kaldo process », Journal of Materials, , p. 485–490 (DOI 10.1007/BF03378430, lire en ligne)
- (de) « Forges de La Providence », (consulté le )
- Affinage des fontes phosphoreuses en une phase avec décrassage en cours de soufflage, Communauté européenne du charbon et de l'acier, (lire en ligne [PDF])
- « Cahiers d'informations techniques », Revue de métallurgie, vol. 77, , p. 284
- (en) Robert A. Whitman, Mineral yearbook, (lire en ligne [PDF]), p. 524 ; 525 ; 528
- (de) « SSAB, Borlänge »,
- (en) Amit Chatterjee, Ramesh Singh et Banshidhar Pandey, Metallics for Steelmaking: Production and Use, Allied Publisher Ltd., (ISBN 81-7764-130-1, lire en ligne), p. 409
- Sauf mention contraire, la liste des TBRC et leurs caractéristiques sont issues de [1]
- (vls) « Besluit van de deputatie van de provincie Antwerpen » [PDF], Metallo-Chimique NV,
- (en) « Case Summary: Settlement reached at the Chemetco Superfund Site », Environmental Protection Agency
- (en) « Tennant Creek »,
- (en) P. J. Mackey et G. C. Balfour, « Pyrometallurgy », JOM (Journal of the Minerals, Metals & Materials Society), vol. 30, , p. 36-43 (ISSN 1543-1851, DOI 10.1007/BF03354363, lire en ligne)
- (en) « Lodged consent decree - Appendices A through O - Case 3:00-CV-00670-DRH-DGW » [PDF], EPA, , p. 205 ; 292-298
- (en) C. M. Diaz, C. A. Landolt, Anthony E. M. Warner et Ahmed Vahed, « A Review of Nickel Pyrometallurgical Operation », JOM (Journal of the Minerals, Metals & Materials Society), (DOI 10.1007/BF03258548, lire en ligne [PDF])
- (en) « Turnkey Process Plant Solutions » [PDF], Furnace Fabrica,
- (en) J. D. Robertson et C. J. Price, « An Assessment of Mercury Emissions from the Afton Copper Smelter, British Columbia, Canada », Journal of the Air Pollution Control Association, (ISSN 0002-2470, DOI 10.1080/00022470.1986.10466115, lire en ligne)
- (en) Janice L. Jolly, 2012 Technical Report : The U.S. Copper-base Scrap Industry and Its By-products, Copper Development Association Inc, (lire en ligne [PDF]), p. 24 ; 85
- (en) M. K. Snyder et F. D. Shobe, Source Category Survey: Secondary Copper Smelting and Refining Industry, EPA, (lire en ligne), p. 45
- (en) « Top Blown Rotary Converter (TBRC) Détails »,
- (en) « Lead », dans Alistair Davidson, Jessica Ryman, Charles A. Sutherland, Edward F. Milner, Robert C. Kerby, Herbert Teindl, Albert Melin, Hermann M. Bolt, Ullmann's Encyclopedia of Industrial Chemistry, Wiley-VCH, (DOI DOI: 10.1002/14356007.a15_193.pub3)
- (en) « Iran's Lead and Zinc Overview », Metal News, (lire en ligne)
- (es) Ricardo Arteaga Rodriguez et al., Manual de evaluación técnico-económica de proyectos mineros de inversión, Instituto Tecnológico Geominero de España, , 2e éd. (ISBN 8478403051 et 9788478403059, lire en ligne), p. 510
- (en) Rodney Jones, « JOM World Nonferrous Smelter Survey, Part II: Platinum Group Metals », The journal of the Minerals, Metals & Materials Society, no 56, , p. 59-63 (DOI 10.1007/s11837-004-0238-8, lire en ligne [PDF])
- (en) Greg K. Roset, Jan W. Matousek et Paul J. Marcantonio, « Converting practices at the stillwater precious metals smelter », Review of Extractive Metallurgy, JOM, vol. 44, , p. 39–42 (lire en ligne)
- (en) Greg Roset, Dayle Flynn et Jacob Bummer, « Granulation as it pertains to electric furnace matte, converter slag, and converter matte in a PGM smelter », dans Jerome P. Downey, Thomas P. Battle, Jesse F. White, International Smelting Technology Symposium: Incorporating the 6th Advances, The Minerals, Metals & Materials Society, (ISBN 978-1-11829-116-0, lire en ligne), p. 23-30
- http://ricerca.gelocal.it/nuovavenezia/archivio/nuovavenezia/2010/04/04/VMHPO_VMH01.html?refresh_ce
- http://pratclif.com/mines/kamoto/copperDirectory02-Jan.pdf
- http://www.tcs.com/sitecollectiondocuments/case%20studies/tcs_innovation_case_jhagadia-copper.pdf
- (en) « Gujarat Copper Project (GCP) at Bharuch, Gujarat », Hindustan Copper
- (en) « Kaldo Furnace inauguration », Hindustan Copper,
- http://www.xiangguang.com/esalegy.asp
- (en) Tang Xulong, « The technological developments of scrap copper smelters in China », ENFI
- (en) « Boliden awarded a SEK 40 million Contract in China », Boliden,
- https://docplayer.org/55975548-Sms-siemag-fuehrend-in-sekundaermetallurgie.html
- https://www.aurubis.com/binaries/content/assets/aurubis-en/dateien/responsibility/updatedenvironmstatem-hh_luenen_2013.pdf
- (en) « 2012 annual report » [PDF], Boliden AB, p. 48
- (en) Pui-Kwan Tse, 2012 Minerals Yearbook, USGS, (lire en ligne [PDF]), p. 8.7
- (en) « Present situation and Prospect of Guangxi Copper Industry chain in 2020 », SMM, (consulté le )
- https://docplayer.net/amp/36105792-Greetings-from-outotec-smelting.html
- (en) « Aurubis Richmond LLC SIP Permit Application », Aurubis, (consulté le )
- (en) « Aurubis doubles U.S. investment in multimetal recycling facility », Aurubis, (consulté le )
- |langue= de |format= pdf |Périodique= Echo der Arbeit |date= 26-11-1956 |numéro= 21 |titre= Neue Wege zum Stahl |passage= 244-245 |lire en ligne= https://www.archive.nrw.de/sites/default/files/media/files/Echo%20der%20Arbeit%2021.1956.pdf}}
- (en) Colin J. Smithells, Metals Reference Book, Butterworths, , 1582 p. (ISBN 0408706279, lire en ligne), p. 1432 ; 1434
- Bernard Trentini, « Aciéries - Évolution des procédés », dans Techniques de l'ingénieur. Élaboration et recyclage des métaux, Éditions techniques de l'ingénieur,
- (en) Marc E. Schlesinger, Matthew J. King, Kathryn C. Sole et William G. I. Davenport, Extractive Metallurgy of Copper, Elsevier, , 5e éd. (ISBN 978-0-08-096789-9, lire en ligne), p. 393
- (en) Heinrich R. Traulsen, John C. Taylor et David B. George, « Copper Smelting - An Overview », JOM (Journal of the Minerals, Metals & Materials Society), no 34, , p. 35–40 (DOI 10.1007/BF03338071, lire en ligne [PDF])
- (en) « Top blown rotary converter – TBRC and Kaldo », SMS Group (consulté le )
- (en) Markus A. Reuter, « Review of Metal Recycling » [PDF], Outotec, (consulté le )
- (en) Vincent Rich, The International Lead Trade, Woodhead Publishing, (ISBN 1855731037, lire en ligne), p. 50