Plastique renforcé de fibres naturelles
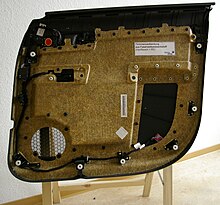
Un plastique renforcé de fibres naturelles est un composite fibre-plastique fabriqué à partir d'un plastique (par exemple résine polyester, résine époxy ou polyamide) et de fibres naturelles. Au sein des biomatériaux, le plastique renforcé de fibres naturelles fait partie des biocomposites. Il est utilisé à la fois comme plastique renforcé de fibres longues et comme plastique renforcé de fibres courtes. Les plastiques renforcés de fibres naturelles bénéficient d'un niveau de stabilité grâce aux fibres naturelles incorporées, ce qui ne serait pas possible sans elles. Le principal domaine d'application est la construction de véhicules, en particulier dans la construction de composants de panneaux dans les intérieurs de véhicules.
Histoire[modifier | modifier le code]

Les plastiques renforcés de fibres naturelles ont été utilisés pour la première fois au milieu du XXe siècle sous forme de composites de fibres naturelles avec des liants chimiques tels que les résines phénoliques. En 1941, le constructeur automobile Henry Ford présente une voiture avec une carrosserie en fibres liées à la résine, la Soybean Car.
Jusqu'aux années 1980, les matériaux principalement thermodurcissables, équipés de fibres de bois et de coton, étaient utilisés comme matériaux dans la construction automobile. Bien qu'ils aient été utilisés à l'échelle internationale principalement pour les pièces intérieures des véhicules, ils ont constitué le matériau des panneaux de la carrosserie de la Trabant en RDA. À l'internationale, les cabines des camions sont également constituées de matériaux en fibre de coton noyés dans de la résine phénolique pour gagner du poids.
Aujourd'hui, de nombreux composants à l'intérieur des voitures particulières sont en plastique renforcé de fibres naturelles, y compris, par exemple, les garnitures de porte, les composants du tableau de bord, les garnitures de pied et autres. Différentes fibres telles que le chanvre et le lin, l'abaca mais aussi le coton et le bois sont utilisées. Les plastiques tels que le polypropylène et le polyéthylène servent de matrice.
Matériaux utilisés[modifier | modifier le code]
Polymères[modifier | modifier le code]
En principe, une distinction est faite entre les polymères thermodurcissables et thermoplastiques lorsqu'il s'agit de polymères. Ce que les deux ont en commun, cependant, c'est que leur tâche principale est de transférer uniformément les charges qui se produisent à l'élément de renforcement, la fibre naturelle. Une bonne connexion entre la fibre et la matrice est pour cette raison une exigence de base. Dans les composites à fibres naturelles, il est souvent difficile d'assurer cette liaison, car les fibres naturelles ne permettent souvent que de faibles interactions avec les polymères en raison de leur hydrophilie, qui est due au grand nombre de groupes hydroxyle dans la cellulose. Cependant, une mauvaise adhérence entre le polymère et la fibre conduit à des propriétés mécaniques significativement plus faibles du matériau composite. Pour cette raison, des promoteurs d'adhérence (de) sont ajoutés à la plupart des polymères, qui peuvent former des liaisons chimiques fortes avec le plastique et la fibre naturelle.
Les thermodurcissables se caractérisent par une forte réticulation irréversible des molécules individuelles. Sous l'influence de la température, ils ne ramollissent pas, mais commencent à se décomposer. Par conséquent, les matériaux thermodurcissables renforcés de fibres naturelles ne sont généralement pas recyclables et ne peuvent donc être recyclés que thermiquement. Les polymères les plus couramment utilisés sont les résines phénoliques et époxy.
Les thermoplastiques se déforment sous l'influence de la température, ce qui signifie que le processus de fusion et de solidification devient réversible et que les matériaux deviennent formables et recyclables. Les thermoplastiques les plus couramment utilisés sont le polypropylène et le polyéthylène, le polystyrène et les polyamides.

Fibres naturelles[modifier | modifier le code]
Une variété de fibres naturelles différentes peut être utilisée pour la production de composites de fibres naturelles. Les fibres diffèrent parfois considérablement par leur forme et leur longueur, ainsi que par leur composition chimique et leurs propriétés mécaniques[1]. Cela a à son tour un impact majeur sur les options de traitement des fibres et les propriétés des matériaux composites.
Les fibres les plus fréquemment utilisées pour la production de matériaux composites renforcés de fibre (de) sont les fibres domestiques de lin et de chanvre, ainsi que les fibres subtropicales et tropicales telles que les fibres de jute, de kénaf, de ramie ou de sisal. Les fibres de bois sont également utilisées comme matériau de remplissage et de renforcement dans les composites renforcés de fibres. Dans certains processus, ces fibres sont spécifiquement modifiées par désintégration aux ultrasons de manière qu'elles reçoivent des propriétés techniques reproductibles grâce au traitement standardisé. Pour mieux les distinguer des autres fibres naturelles et en raison de leur importance quantitative, les matériaux composites avec du bois comme matériau de remplissage ou de renforcement sont appelés composites bois-plastique.
Biopolymères[modifier | modifier le code]
Les recherches dans le domaine des biopolymères se sont récemment fortement intensifiées. En utilisant ces plastiques, des matériaux composites biodégradables et inoffensifs pour la santé peuvent être produits[2], qui ont souvent des propriétés comparables aux polymères à base de pétrole naturels et renforcés de fibres de verre.
Un grand nombre de polymères thermodurcissables et thermoplastiques sont maintenant disponibles et peuvent être utilisés comme matrice pour les matériaux composites. L'un des bioplastiques les plus couramment utilisés est le polylactide (PLA), fabriqué à partir d'amidon de maïs. Dans la plupart des cas, cependant, le prix de ces polymères est nettement supérieur à celui des plastiques à base de pétrole, c'est pourquoi ils sont beaucoup moins utilisés à des fins industrielles.
En traitement[modifier | modifier le code]
Étant donné que les fibres naturelles diffèrent considérablement des fibres de verre et de carbone, il est souvent nécessaire d'adapter les procédés de fabrication courants des composites de fibres aux caractéristiques particulières des fibres naturelles.
Ceux-ci incluent, par exemple, leur stabilité thermique limitée, qui limite également fortement le choix des thermoplastiques possibles, et leur forte hydrophilie. Néanmoins, il est aujourd'hui possible de traiter des composites de fibres naturelles avec une variété de méthodes différentes en adaptant les procédés de fabrication existants et en développant de nouveaux procédés. L'une des méthodes de traitement les plus importantes pour le plastique renforcé de fibres naturelles est le moulage par compression, dans lequel des nattes de fibres sont utilisées et des composants et plastiques thermoplastiques et thermodurcissables utilisés. Les nouvelles méthodes de traitement, dont on dit qu'elles ont un grand potentiel de croissance, comprennent le moulage par injection de fibre naturelle (en) et l'extrusion de fibres naturelles. Les autres procédés de traitement du plastique renforcé de fibres naturelles sont la pultrusion, le moulage par transfert de résine ou le préimprégné en feuille.
Caractéristiques[modifier | modifier le code]
Les composites de fibres naturelles ont un certain nombre de propriétés qui les rendent intéressants en tant que matériau.
Les fibres naturelles ont généralement une densité inférieure à celle des fibres de verre ou des charges minérales, ce qui, avec une proportion élevée correspondante de volume de fibres, peut entraîner un gain de poids significatif pour un composant. Cependant, étant donné que les fibres naturelles sont comparativement rigides et robustes, il existe un grand potentiel pour remplacer les plastiques renforcés et chargés de fibres de verre. Un problème majeur avec ces matériaux, cependant, est leur résistance aux chocs souvent relativement faible, qui peut être améliorée en ajoutant des fibres naturelles à haute élasticité.
De plus, les fibres naturelles et donc aussi les matériaux composites sont moins nocifs d'un point de vue santé, ce qui améliore la sécurité au travail. Les composites de fibres naturelles sont également moins sujets aux éclats que les plastiques renforcés de fibres de verre.
Le prix des fibres naturelles étant relativement stable, indépendamment de la forte fluctuation du prix du pétrole, les coûts de production de ces matériaux peuvent être mieux planifiés. De plus, les fibres naturelles nécessitent moins d'énergie lors de la production que les fibres de verre ou de carbone, ce qui, outre des coûts de production plus faibles, conduit également à un bilan carbone nettement amélioré des matériaux. Les fibres naturelles brûlent presque sans CO2 et sans résidus.
Outre l'aspect santé au travail, il existe d'autres avantages lors du traitement de ces matériaux. Les fibres naturelles provoquent une usure moins abrasive de l'outil et, en raison de la réduction nécessaire des températures de traitement, les temps de cycle de production sont plus courts et la consommation d'énergie est plus faible.>>>F/NF
NF-EP : fibres de lin en combinaison avec de la résine époxy avec une teneur en fibres de 60 % (volume), douze couches, processus de moulage par compression.
CF-EP : fibres de carbone combinées à de la résine époxy, procédé de moulage par compression.
Caractéristiques | Unité | NF-EP | Aluminium (alliages) | CF-PE |
---|---|---|---|---|
Masse volumique | g/cm3 | 1,31-1,33 | 2,7 | 1,5 |
Résistance à la traction | MPa | 330-365 | 49 (-700) | 2 850 |
Résistance spécifique à la traction | MPa | 248-278 | 18 (-259) | 1 900 |
Module de Young | GPa | 35 | 70 (-73) | 225 |
Module de Young spécifique | GPa | 26,3 | 25,9 (-27) | 150 |
Application[modifier | modifier le code]
L'industrie automobile est le principal domaine d'application des composites en fibres naturelles thermoplastiques et thermodurcissables.
Dans les années 1999 à 2005, l'utilisation de matériaux a augmenté de quinze mille tonnes à trente mille tonnes, enregistré dans l'industrie automobile allemande, soit une quantité moyenne d'environ 3,6 kg de plastique renforcé de fibres naturelles par voiture[3]. Les matériaux composites à base de fibres naturelles sont utilisés par pratiquement tous les constructeurs automobiles connus. Les domaines d'application typiques sont, outre les panneaux de porte intérieurs, également les garnitures de toit, les tableaux de bord ou les plages arrière.
La quantité de plastiques renforcés de fibres naturelles utilisées pour des applications non automobiles en Allemagne est d'environ deux mille tonnes[3]. Cependant, étant donné que les applications de ces matériaux ne sont pas toujours activement diffusées, il est difficile d'enregistrer tous les produits contenant des plastiques renforcés de fibres naturelles. Les applications les plus connues incluent un porte-meule en polypropylène et chanvre, des urnes, une coque de téléphone portable, divers matériaux d'emballage, des jouets pour enfants, des valises, des distributeurs de savon à main bio et des meubles.
Un autre exemple d'application est la construction de bateaux[4].
Bibliographie[modifier | modifier le code]
- Michael Carus, Jörg Müssig et Christian Gahle, Naturfaserverstärkte Kunststoffe. Pflanzen – Rohstoffe, Produkte. Fachagentur Nachwachsende Rohstoffe e. V., Gülzow 2008 (Lire en ligne [PDF].
- Jörg Müssig et Michael Carus, Bio-Polymerwerkstoffe sowie holz- und naturfaserverstärkte Kunststoffe. In: Marktanalyse Nachwachsende Rohstoffe Teil II. Fachagentur Nachwachsende Rohstoffe e. V., Gülzow 2007, fnr-server.de [PDF].
- A. K. Bledzki, O. Faruk et V. E. Sperber, Cars from Bio-Fibres. Macromolecular Materials and Engineering Ausgabe 291, 2006, S. 449–457.
- Kim L. Pickering (Hrsg.), Properties and performance of natural-fibre composites. Woodhead Publishing, Cambridge, 2008 (ISBN 978-1-84569-267-4).
- Amar K. Mohanty, Manjusri Misra et Lawrence T. Drzal (Hrsg.), Natural fibers, biopolymers, and biocomposites. Taylor & Francis Group, Boca Ranton FL 2005 (ISBN 0-8493-1741-X).
- Tim Huber, Jörg Müssig, Erwin Baur et Frank Otremba, Verstärkung aus der Natur, dans Kunststoffe, 2008, Ausgabe 98 (7), S. 97–101.
- Produktkatalog Naturfaser-Spritzguss. nova-Institut, Hürth, 2007 (ISBN 978-3-9805840-9-8), S. 10–13.
- K. Van de Velde et P. Kiekens, Material Properties, Biopolymers: overview of several properties and consequences on their applications. In: Polymer Testing, Ausgabe 21, 2002, S. 433–442.
- P.A. Fowler, J.M. Hughes et R.M Elias, Review Biocomposites: technology, environmental credentials and market forces. In: Journal of the Science of the Food and Agriculture, Ausgabe 86, 2006, S. 1781–1789.
- Walter Michaeli, Einführung in die Kunststoffverarbeitung, 2006.
Notes et références[modifier | modifier le code]
- (de) Cet article est partiellement ou en totalité issu de l’article de Wikipédia en allemand intitulé « Naturfaserverstärkter Kunststoff » (voir la liste des auteurs).
- (en) Paulo Peças, Hugo Carvalho, Hafiz Salman et Marco Leite, « Natural Fibre Composites and Their Applications: A Review », Journal of Composites Science, vol. 2, no 4, , p. 66 (ISSN 2504-477X, DOI 10.3390/jcs2040066, lire en ligne, consulté le ).
- (en) Lina Altomare, Lorenzo Bonetti, Chiara E Campiglio, Luigi De Nardo et Lorenza Draghi, « Biopolymer-based strategies in the design of smart medical devices and artificial organs », The International Journal of Artificial Organs, vol. 41, no 6, , p. 337–359 (ISSN 0391-3988, PMID 29614899, PMCID 6159845, DOI 10.1177/0391398818765323, lire en ligne, consulté le ).
- Michael Carus, Christian Gahle, Cezar Pendarovski, Dominik Vogt, Sven Ortmann, Franjo Grotenhermen, Thomas Breuer et Christine Schmidt, Studie zur Markt- und Konkurrenzsituation bei Naturfasern und Naturfaserwerkstoffen (Deutschland und EU), Fachagentur Nachwachsende Rohstoffe (FNR), 2008.
- (de) Soenke Schierer, « Öko-Bootsbau: Auf der grünen Welle », sur faz.net (ISSN 0174-4909, consulté le ).